Introduction
The need for high voltage testing at has increased dramatically over the last few years. Typically test objects include HVDC valves, AC and DC cables, line insulators, cable accessories, wall and transformer bushings, optical instrument transformers and station post insulators for different applications.
Part of this increase comes from manufacturers of high voltage equipment and part from an increased demand from transmission system operators (TSOs). There are a number of factors that has triggered the increased demand from TSOs. One factor is that TSOs today do not have the deep knowledge in the design and testing of high voltage components as they have had. This means for example that they do not have the knowledge to evaluate test reports from many different high voltage laboratories. One result of this is that some TSOs have put as a requirement that type testing of a specific product should be done in one laboratory or under the surveillance of one laboratory. Another factor is that the requirements in the standards today are not stringent enough compared to the experience from service. This leads to an increase in for example test duration, new test methods and more stringent requirements. Also some TSOs want to qualify products that are of significant importance to their network thus performing the tests either together with the suppliers or without them.
In this paper we highlight some measures and investments that STRI have made in order meet these trends and demands.
Investments
STRI has unique facilities allowing full scale dielectric and pollution testing of ±800 kV DC and AC components for transmission lines and substations. Also some equipment for 1100 kV has been tested in the laboratory. Type and development tests have been done on a great variety of products such as HVDC valves, high voltage circuit breakers, bushings, current and voltage transformers, insulators and accessories, high voltage AC and DC cables.
STRI has during the last ten years extended its testing capabilities three times. A little more than 10 years ago an investment was made in a site for long term testing of equipment for UHVDC, see Figure 1. This is where all types of station and apparatus insulation for ±800 kV DC project were long term tested and the installed equipment included: wall bushing, optical current transformer, voltage divider, surge arrester, smoothing reactor capacitor, RI capacitor, disconnector and by-pass breaker. The insulators and apparatuses were full-scale tested during more than 2 years at 850 kV and elevated voltages, and later were tested for 2 more years. All components withstood the test with success [6]. Some new insulator options for ±800 kV, e.g. hybrid insulator combining porcelain core and silicone rubber sheds has also been verified at this test station.
In 2011 a new high voltage test hall was inaugurated which primarily function is type testing of HV AC and DC cables (see section 4). As the demands continued to change and increase it was decided to further invest in more test equipment and laboratories. This new investment was inaugurated in 2015 (see section 5).
Prequalification testing of DC Cable systems
Today there are no DC cables for UHV but there are XLPE cables on the market for 525 kV DC. Testing of these cable systems intended for EHV DC-applications is in many cases a delicate task. There are several parameters that can complicate the interpretation of the result. For this reason it is of outmost importance that the testing is done in an accredited lab with experienced personnel and HV equipment that has stable long term performance. All measured parameters should be registered in a computer that allows for post processing and inspection.
In 2016 four German TSOs (50hertz, Amprion, TenneT and Transnet) issued an open tender for prequalification testing of HVDC cables on 525 kV. STRI won part of this tender and started the test in August 2017. The consequence of the order was that the test site for long term testing of HVDC equipment as seen in figure 1 needed to be disassembled. The reason is that the TSOs had several specific requirements on the test site that goes far beyond the requirements of the technical brochure from CIGRE (TB 496 “Recommendations for testing DC extruded Cable Systems for power transmission at a rated voltage up to 500 kV”) [1]. Firstly, the cable should go through different media (tunnel, sand and pipes), see figure 2. Secondly the situation at site should be simulated as much as possible which means that everything should be covered with 1,3 m of moraine, see figure 3. Thirdly, for the temperature regulation the requirement was that the dummy cable should go through, from a temperature aspect, the most critical media i.e. sand and pipe. In order for this to be done the dummy cable needed to be over 60 m long. The consequence of this was that an investment needed to be done in current transformers and in the temperature regulation system (regulating transformers).
After performing the 1-year prequalification test, the guidelines from CIGRE requires that superimposed impulse testing on a 30 m section of the cable shall be done. However, the requirements of the TSOs are that the complete 120 m cable system with all the accessories should be tested. Applying superimposed impulses on DC-voltage with full length cable system puts extremely high requirements on the test circuit and on the individual components such as the DC-generator and the impulse generator.
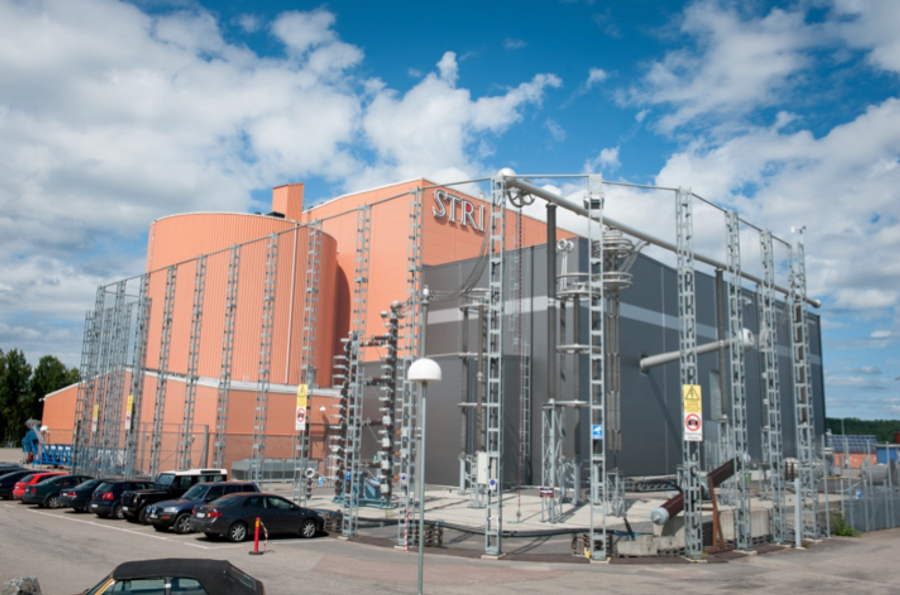
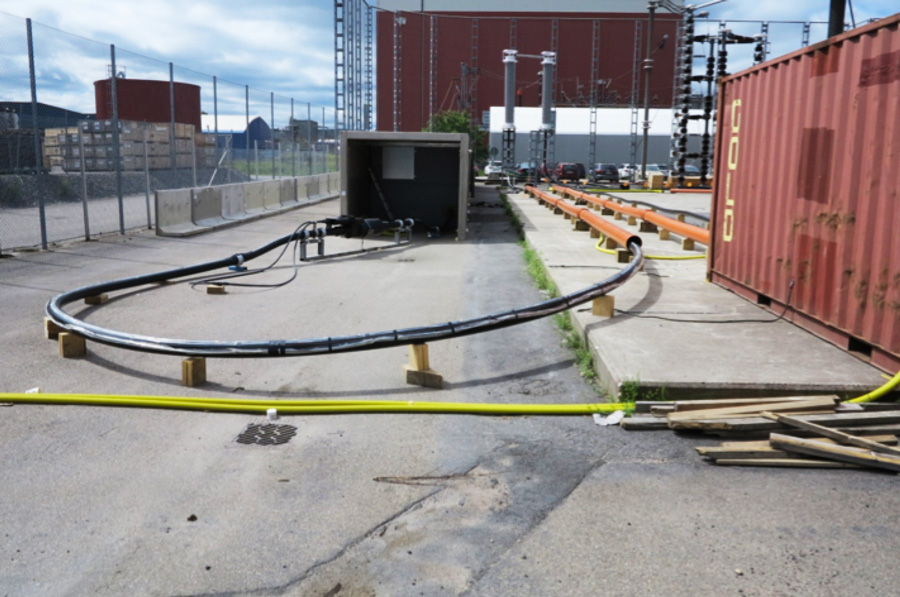
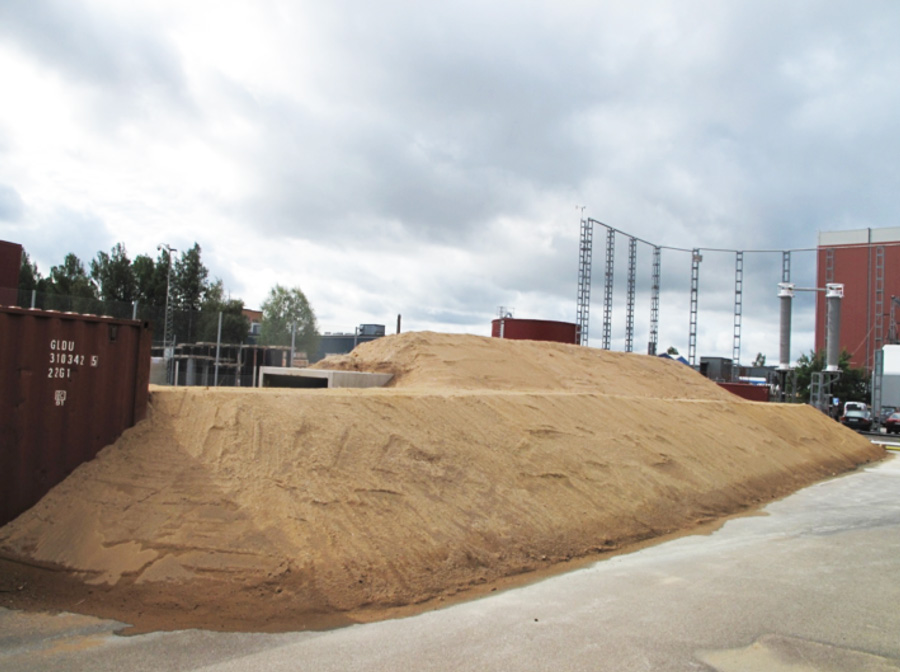
Requirements on testing of cables
Due to the increased need for new investments by TSOs in HVAC and DC cables STRI invested in 2011 in one more high voltage test hall, see figure 4. The test hall is fully equipped in order to be able to test high voltage equipment with system voltages up to 500 kV. The investment consisted of a high voltage hall, 600 kV resonance transformer and a 2 MV, 200 kJ, impulse generator. The test hall has since it was inaugurated been more or less fully occupied, in particularly for testing of high voltage DC and AC cables.
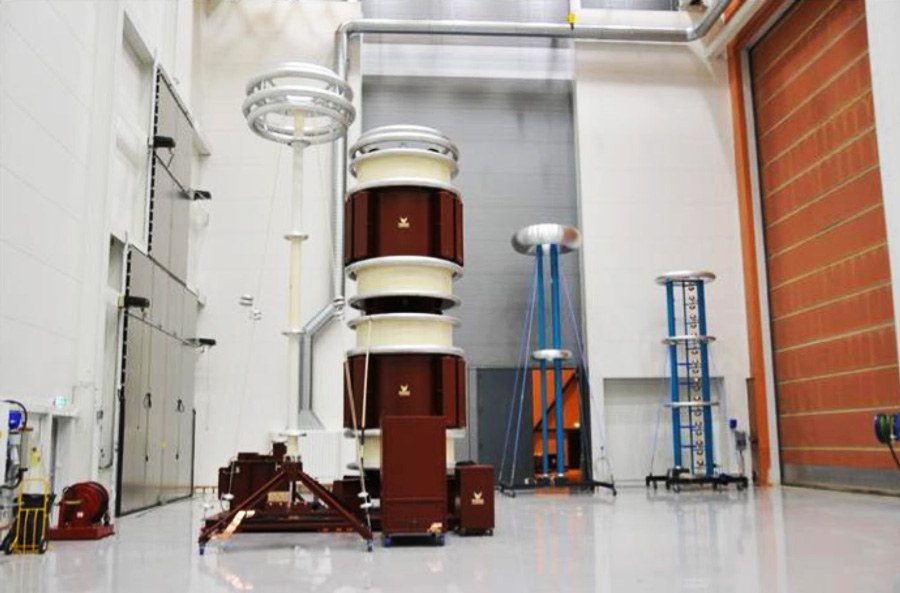
Requirements on testing in one laboratory
There is a trend that some utilities and manufacturers require that all testing in accordance with the standards are performed in one laboratory. These requirements led to further investments at STRI in 2015. One is to build test equipment for bending test on cables. The requirement was that cables of all voltages and cross section could be tested irrespective of the bending radius. The result can be seen in figure 5. In this machine we have recently performed bending tests on cables from 145 kV AC up to 525 kV DC. Another was to build a laboratory for non electrical testing of cable material. In this laboratory we can perform different material tests such as e.g elongation at break, carbon black content, resistivity etc.
We have also in the last few years seen an increase in test requests for prequalification tests on HVAC cables. For this reason it was decided to expand the testing capabilities with an additional test site (see figure 7). Also it was decided to invest in test equipment such as 650 kV AC resonance transformer (see figure 8) and current heating system (see figure 9). The resonance transformer is designed to meet the requirements of the future cable systems.
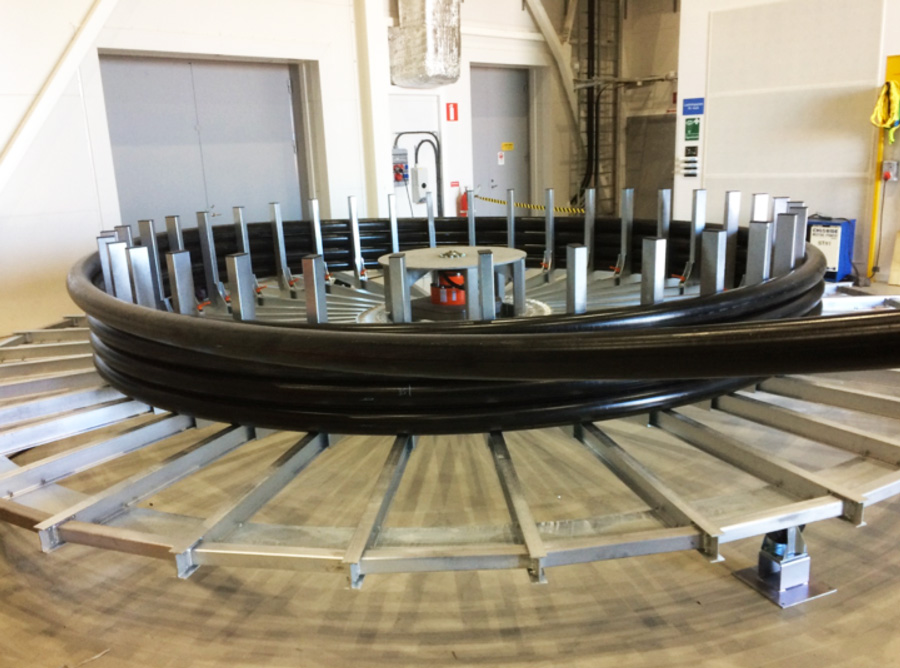
(this photo shows the bending test on a 525 kV DC cable).
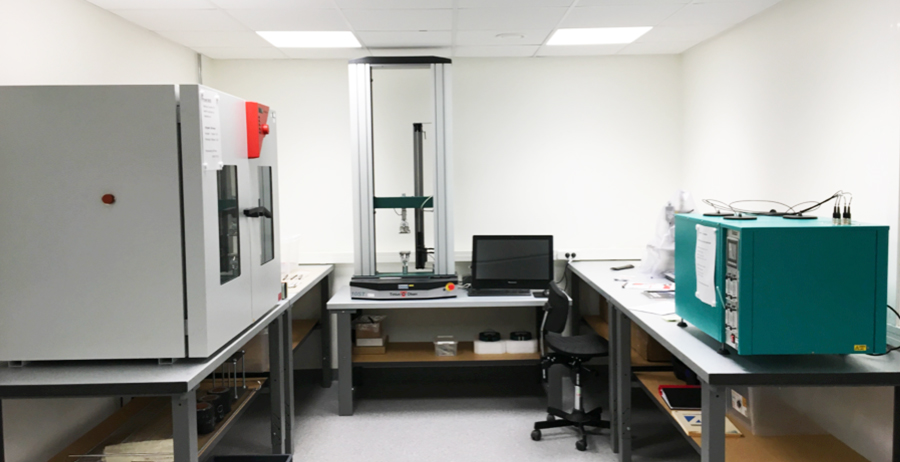
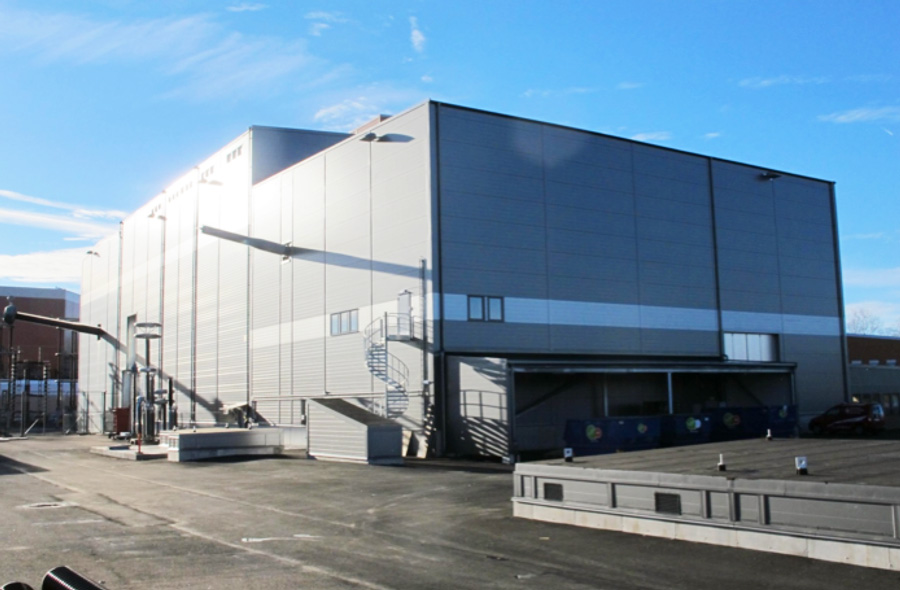
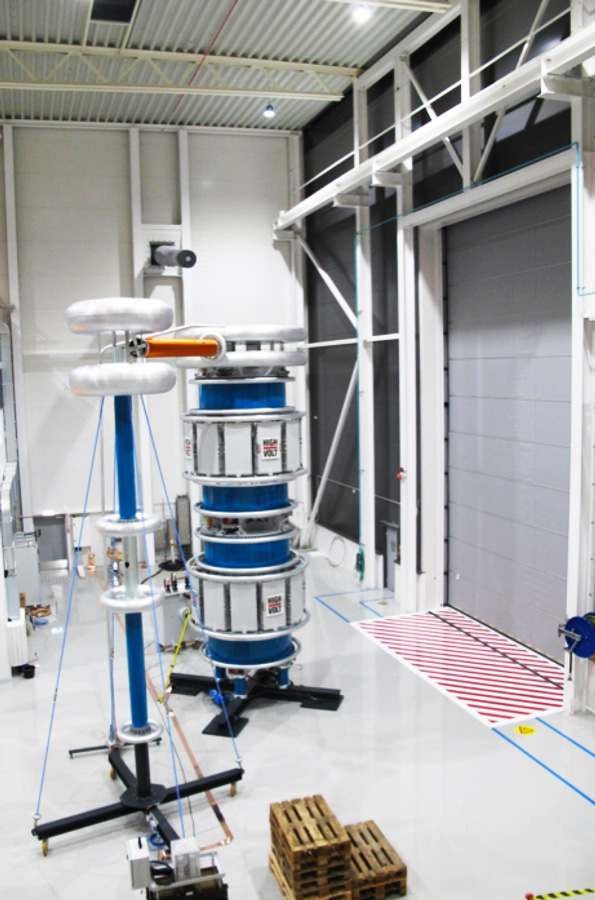
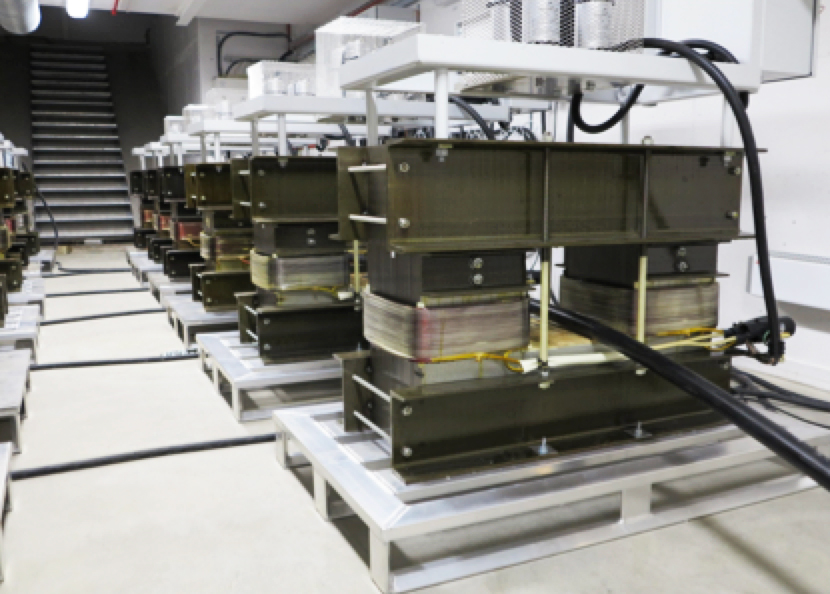
Requirements on testing of bushings
As for cables there was a decision to invest in testing of HV bushings. STRI has earlier focussed on performing dielectric testing of bushings. However, the type test also includes mechanical and temperature rise tests. For this reason STRI invested in tooling so that e.g. cantilever tests can be performed on bushings of all sizes.
In order to be able to meet the increased requirements on current for temperature rise tests STRI has invested in and upgraded the current heating systems so that currents up to 9000 A AC and 8400 A DC can be tested. Some customers require that the bushing is tested in a test hall with 50C ambient temperature. This is a requirement for some customers in China. One of STRIs test halls for temperature rise test has the capability to perform tests at these elevated temperatures. Recently ABBs wall bushing rated for 1100 kV DC was tested at STRI with 50C surrounding temperature and with a current of 5839 A DC (see figure 10).
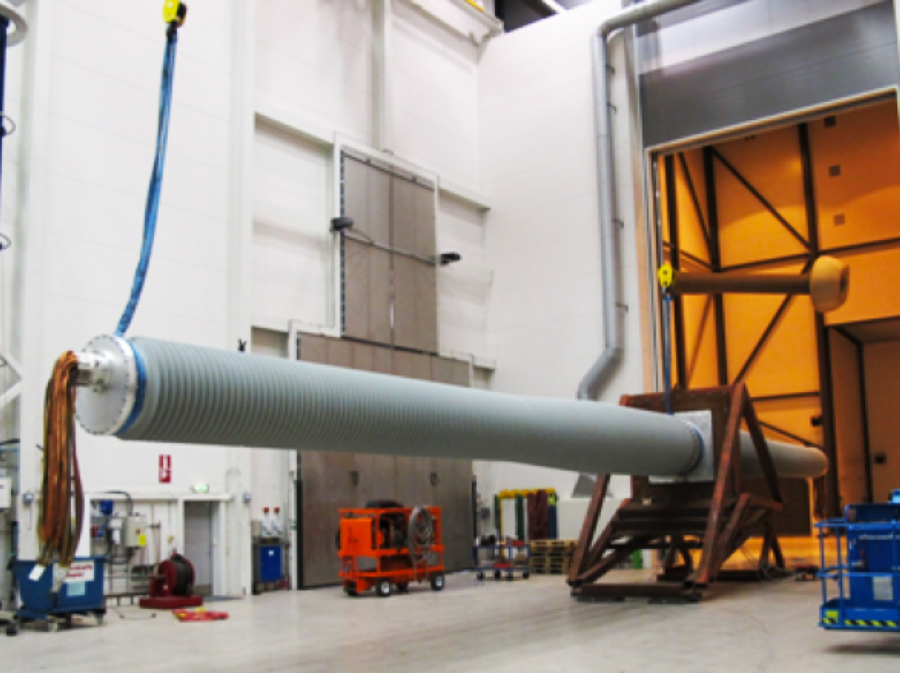
Summary
This report summarises some of the investments and other measures STRI has made in order to adapt to a changing market. It is clear that the development on the market will continue to push further development and investments in new test equipment and test methods.
References
CIGRE TB 496 “Recommendations for testing DC extruded Cable Systems for power transmission at a rated voltage up to 500 kV