Transmission system operators in many countries are searching for solutions to meet growing demand for electrical power and also for integration of renewables into their networks. The only realistic option will be more HV, EHV as well as UHV AC and DC systems – all of which mean a growing population of bushings placed into service. Stringent international regulations are also pushing utilities to rely on testing as one of the most effective means to demonstrate that they are working with due diligence whenever specifying such equipment. This requirement becomes all the more important if one considers the growing numbers of substations and electrical installations located near population centers as well as the accompanying push to reduce substation ‘footprints’. Both trends represent increased risk factors in terms of danger to public safety as well as economic consequences of collateral damage should there be catastrophic failure.
It is therefore increasingly important to look for possible upgrades in technology while also decreasing failures at the early stages of service life. The latter can only be achieved through more detailed installation practices in which all critical functions are well defined and where greater attention is paid to the skills required of the workers involved
According to ISO/IEC Guide 51 safety is ‘freedom from unacceptable risk’. This can be achieved by reducing risk to some tolerable level that takes into account that there will always be some residual risk, i.e. the risk that remains after all possible protective measures have been undertaken. This risk is then determined by arriving at some optimal balance between the ideal of absolute safety and the demands met by the product, which includes benefits to the user, suitability for purpose and cost effectiveness. Safety criteria must be considered first in order to be able to specify the required safety level and to perform any related risk assessment. One way to do this is to combine all the technical as well as non-technical, e.g. social and economic, parameters that play a role in evaluating failure probability and its consequences. For example, to reduce residual risk and also to lower the cost of consequences, explosion-free bushings are increasingly being specified.
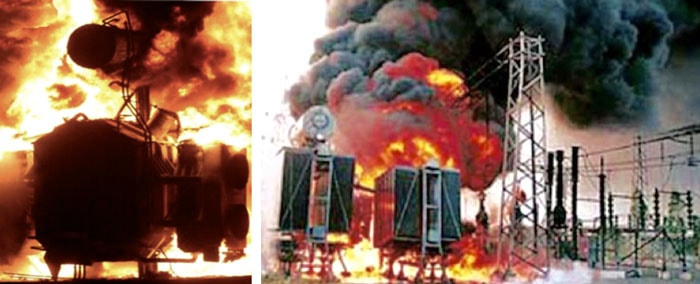
Failures of bushings are responsible for a significant proportion of all transformer failures and can be violent. Although often regarded as only accessories, bushings are in fact the cause of roughly 80% of failures and fires involving transformers filled with insulating mineral oil – even if fire actually occurs in less than 15% of all transformer failures.
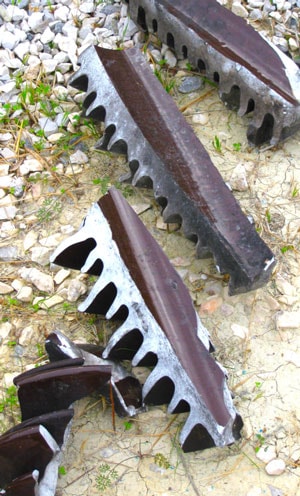
Failures of bushings can result in the porcelain housing shattering into shards and other fragments that are projected at high velocities over a wide area. Moreover, oil that is sprayed out through the cracked unit can be ignited by the arc associated with the fault. In extreme cases, fireballs higher than the transformer itself have been observed following explosive failure of a bushing. Physical protection against explosions and fires involving HV bushings in service are difficult or even impossible to put in place due to the size and location of the equipment. Whenever a particular type of bushing is regarded as being at unacceptably high risk of such failure, access to the site should be limited, during which time design changes to improve safety can be discussed with the manufacturer. Because of the considerations discussed above, explosion-free designs of HV bushings – sometimes still seen as a comparatively new technology – are increasingly used to obtain lower risk solutions in applications where substations are located in urban areas with buildings in the vicinity. While testing explosive behavior may not yet be mandatory, it is increasingly being conducted to enhance reliability and reduce risk – irrespective of location of a power installation.
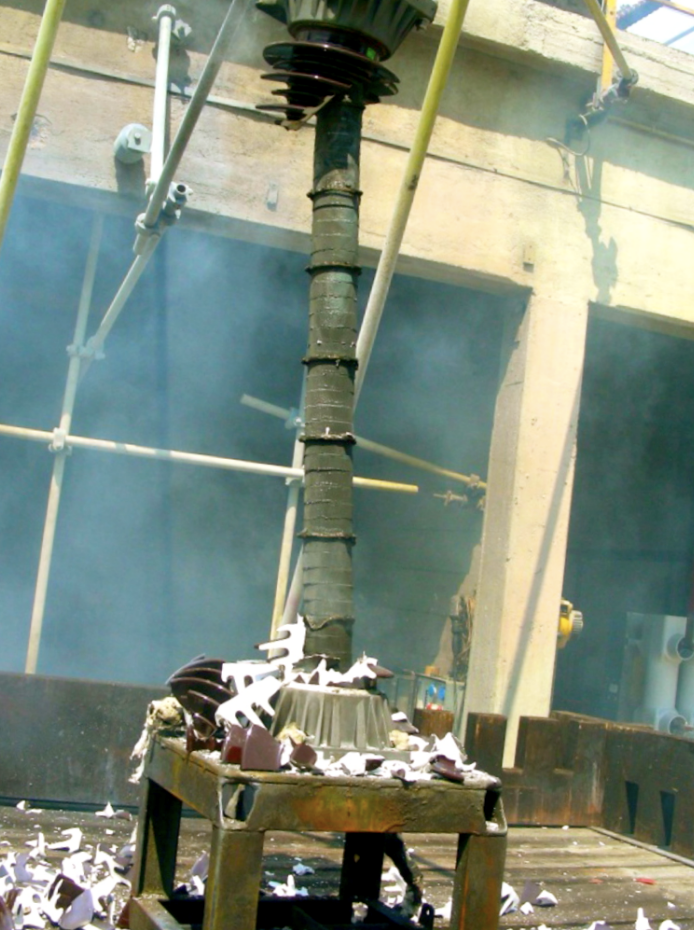
Procedures for Internal Arc Testing
Testing and certification are important tools to assure the safety and reliability of electrical networks. Among the HV components most often submitted to testing for safety reasons are bushings, cable terminations and arresters. The main difference when testing these components lies in the applicable situation in respect to the norms. While IEC and IEEE standards already exist for arresters, there are no international standards available for HV bushings and cable terminations. Rather, technical specifications for these have been prepared by major national utilities while European standards are also available. The HD standard, for example, prescribes triggering the internal arc in a termination by drilling a hole in the main insulation. A 1.5 mm2 copper wire then connects to the screen/metal sheath or a piece of metal is connected to the shield/sheath in order to simulate failure. Later, a short circuit current is applied, whose values (kA and seconds) are chosen according to the maximum short circuit current of the circuit where the HV termination is to be installed. In spite of the fact that the scope of this standard is limited to cables and accessories up to 170 kV, the same test modalities are also now being used for higher ratings of terminations as well as for bushings. Based on past experience from such tests, an internal arc test on bushings is demanding both for the power laboratory and the manufacturer involved, since:
• test set-up and auxiliary electrical facilities such as power source connections, etc. need to be expressly installed and then dismantled after the test;
• demanding protection measures have to be put in place to avoid environmental problems;
• ejected parts from violent shattering can damage the test chamber and even surroundings;
• smoke and noise are harmful to test staff and the environment, which, taken together with the high test ratings, may require overnight tests.
These challenges will only become greater in the future if one considers the increasing market demand for higher values of short circuit current.
Summary & Conclusions
Worldwide demand for power networks will only increase, pushing utilities to install growing populations of HV bushings and other equipment vulnerable to catastrophic failure. At the same time, attention to safety and the environment is also growing. Proper selection of the ratings and characteristics of these components together with high quality levels will be key to reducing the probability of failures even though risk of such events can never be disregarded. Therefore, laboratory tests to simulate internal fault remain a useful tool to help select those products that have safe performance during failure and reduce risk of violent explosion or fire on the network. Requirements for safety of substation equipment will only become more stringent. As such, it will also become important to harmonize and standardize testing requests coming from utilities across the globe.
[inline_ad_block]