As in most countries, wind generation projects in Tunisia tend to be situated close to the sea, typically on elevated plateaus to capture prevailing winds. The Sidi Daoud Wind Park, for example, was commissioned in 2009 and is located on an 800m high peninsula surrounded on both sides by the Mediterranean. The coastline is only 2 km away.
INMR, along with engineers from Tunisia’s national power utility, Société Tunisienne de l’Electricité et du Gaz (STEG), visited the 90/30 kV substation in September 2010, at the end of a long dry summer and coinciding with the onset of the first seasonal rain. What followed was a display of arcing usually observed only in a controlled laboratory setting.
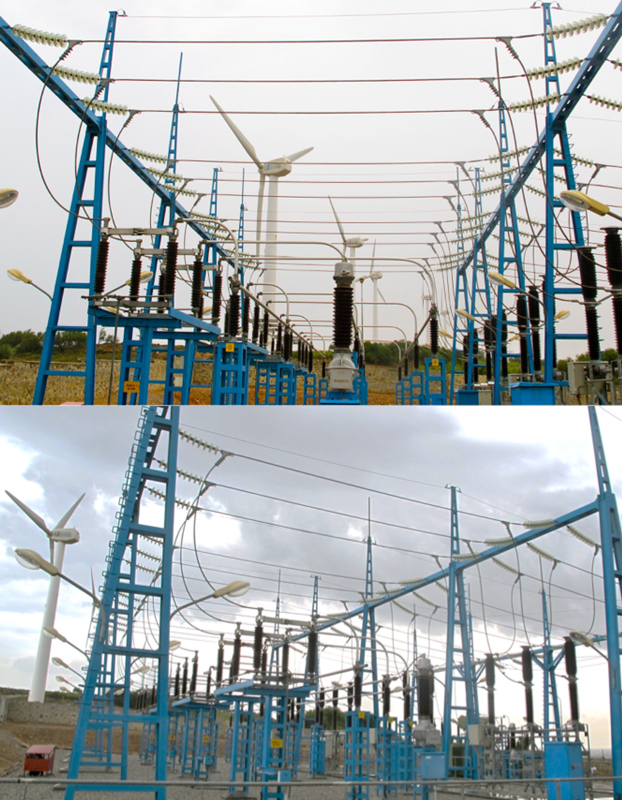
The porcelain housings and support insulators at this digital control system substation were designed with a specific creepage of 32 mm/kV. However, in only its second year of operation and just moments after the start of the first sustained rainfall in 5 months, there was a sudden rapid increase in noise level. This was followed immediately by a period of sustained intense corona and arcing that affected almost every porcelain insulator at the substation.
Substations such as Sidi Daoud are normally washed twice a year, once before and then again after the long summer. Because of such precautions, this type of event was completely unexpected.

INMR Contributor, Raouf Znaidi, who after a long career at STEG has been involved in testing insulator profiles and materials under desert, maritime and industrial pollution, was less surprised. “Past research,” he said, “has shown that dust and sand blown up onto insulators in Tunisia can have a salt content of as high as 18 percent. If you combine this with the exposure of this substation to winds from the sea, mostly blowing from only one direction, this substation is highly vulnerable.”
Znaidi also observed that the fact that none of the glass insulators at the station experienced arcing suggests that their insulation level was sufficient for the high pollution level and that the real problem here was unsuitable profiles and dimensioning of the porcelain. Znaidi also noted that such intense arcing, even if not leading to flashover, might well cause irreversible damage to the glaze and diminish mechanical properties.
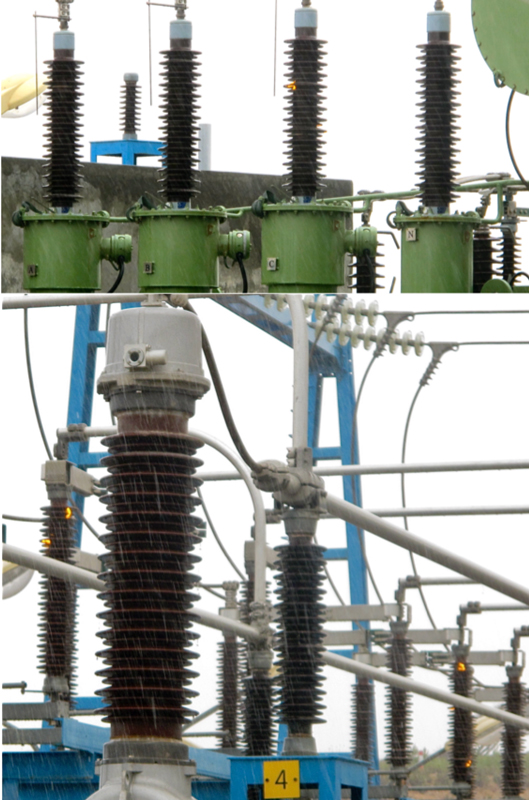
As it turns out, the dramatic arcing under the first rainfall in early September 2010 was not the first problem affecting porcelain at the wind park’s substation. According to local staff, one of the support insulators for a 90 kV live tank breaker had to be replaced due to a broken shed next to the flange. The process of carrying out the replacement then damaged two sheds directly below it. Also, one of the instrument transformers suffered a broken shed. It was not clear what caused this damage but burn marks near the break suggest it may have been related to a power arc.
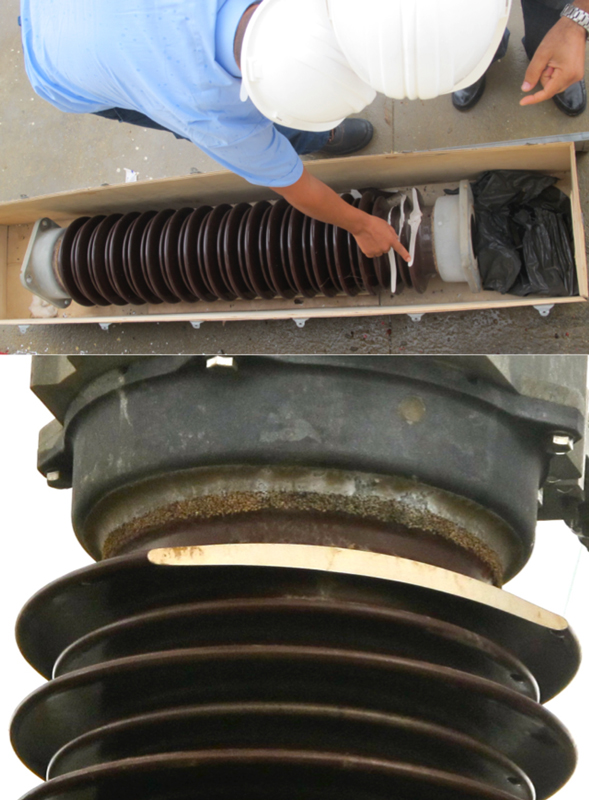
This experience prompted a technical review to discuss the phenomenon observed after the rainfall and to plan what remedial measures would have to be undertaken. One of these would be to apply RTV silicone throughout the substation, something that had already been proposed even before this event occurred.
Another key issue was to establish why the specifications given to suppliers of equipment for this substation did not ensure that the insulation could withstand the stresses imposed by the challenging service environment. Said a STEG Operations & Maintenance Manager, “probably, we should have thought more about the dimensions necessary for the porcelain installed here or even whether a GIS would have been a better choice given the combination of severe pollution exposure and lack of self-cleaning.”
Apparently, one of the problems that may have contributed to this situation is that technical specifications for substations are usually handled by a different department and not by technical maintenance staff. This meant that there was the possibility that full knowledge of the local pollution environment may not have been made available to those involved in procurement.
This type of problem emphasized the need to better know the pollution class of a substation through detailed analysis of ESDD levels and site pollution severity. These types of parameters need to be studied and fully understood before deciding on choice and dimensioning of insulation installed. According to Znaidi, better knowledge of site pollution would have also contributed to establishing the true requirements for laboratory acceptance tests and thereby avoid similar future problems due to inadequate dimensioning. “This was an appointment with corona and arcing that was just waiting to happen”, he remarked. “It was a natural diagnostic allowing quick observation of all the insulation weaknesses at this substation.”
________________
RELATED ARTICLES:
Cooling Tower Pollution Impact on Substation Insulation
Designing Insulation for Harsh Service Environments
[inline_ad_block]