When composite insulators first arrived on the scene about 50 years ago, they were sometimes promoted as ‘indestructible’. Such a designation may have seemed reasonable at the time given that pliable rubber housings might be expected to better resist impact than brittle materials such as porcelain or glass.
By the early 1990s, however, it had become widely apparent that mishandling composite insulators was one of leading causes of irreversible damage. This risk was all the more severe since such damage might occur below the surface and remain undetected visually, meaning that damaged insulators could still be put into service. By the late 1990s, Eskom in South Africa, one of the first utilities to adopt composite insulators on a broad scale, began to document more and more cases of damage from mishandling and developed an internal Guide to instruct workers on how to prevent this. These days, many power system operators installing composite insulators on overhead lines or at substations have published protocols on how best to transport, store and handle them in the field. Nonetheless, cases of damage are still being observed.
Crews installing silicone insulators on a new ±525 kV HVDC line operated by Norwegian TSO, Statnett, in southwest Norway were issued specific instructions on proper handling to avoid risk of damage. This DC line was the first at Statnett equipped entirely with composite insulators whereas, until then, these types had only been used as supports in jumper loops. Correct handling was regarded as especially critical for this project due to the 6m lengths of the insulators, which would make them especially vulnerable to damage from mishandling during transport or installation. A seminar was held for the stringing and installation team and, to avoid misunderstanding due to language, based on photos and illustrations displaying proper and improper handling of the insulators. At the end of the seminar, positive feedback from the work force made it clear that workers were surprised at just how vulnerable these insulators were to handling damage due to factors such as the small thickness of the silicone rubber housing.
Since no cranes could be used in the tough terrain, all insulator and fitting installation was done by helicopter. String fittings were pre-assembled with the insulators at a location close to the towers before being transported to towers by helicopter. This posed a risk to the insulators due to their relatively long length and easy bending of the core rod which, according to the manufacturer, should not be allowed to exceed 20°. Due to this, special attention had to be taken when insulators were lifted from the ground by helicopter.
Installation of tension strings were particularly critical due to the installation method. Tension fittings were installed, together with the composite insulators, to the tower in a vertical position. Each string was then raised with help of a winch system to a horizontal position. This could bend the insulator more than the allowed 20° due to the weight of fittings at the end of the insulator. This risk was resolved by introducing a supporting plastic sheath that surrounded insulators before installation.
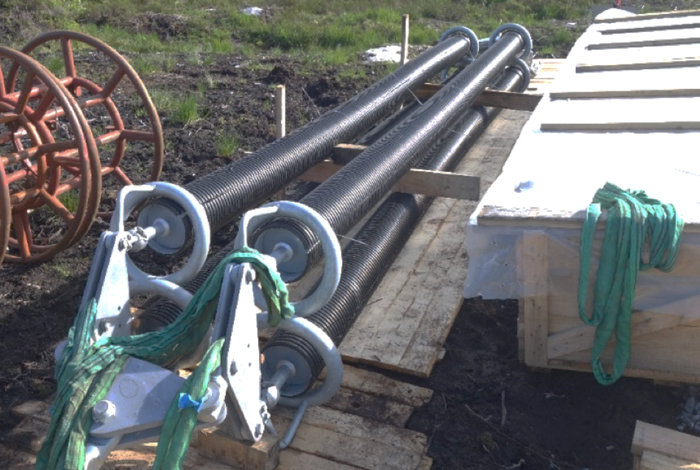

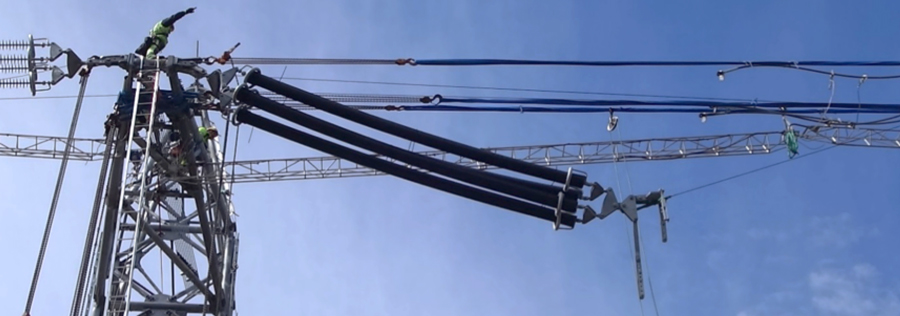
While much of the focus on avoiding mishandling damage to composite insulators has been placed on long rod types due to their much greater population, the problem of handling damage has also extended to hollow core types. Ongoing examples of such insulators that have sustained handling damage suggest that correct handling for these types of products is still not universally understood and respected.
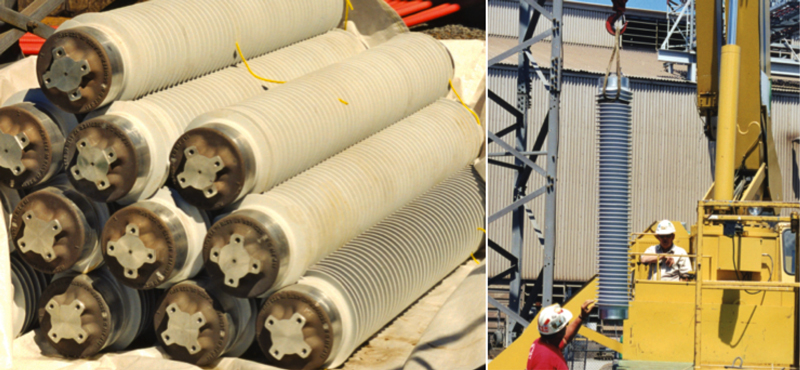
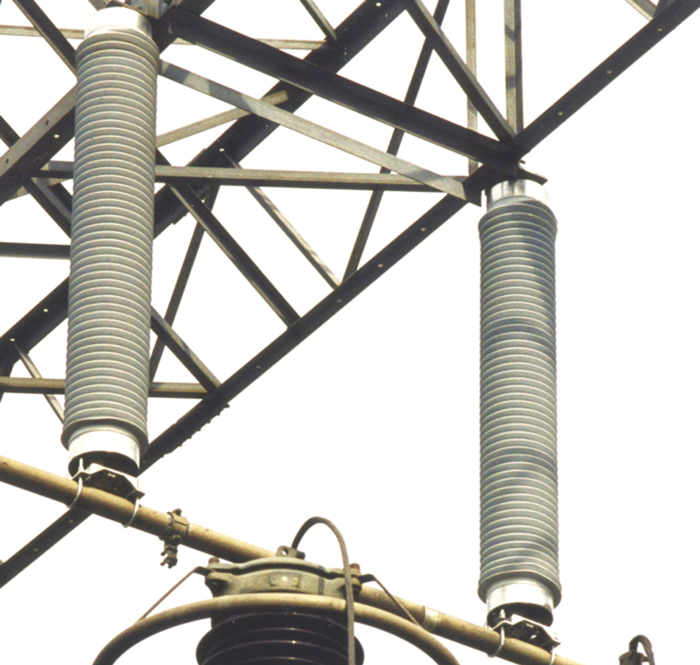
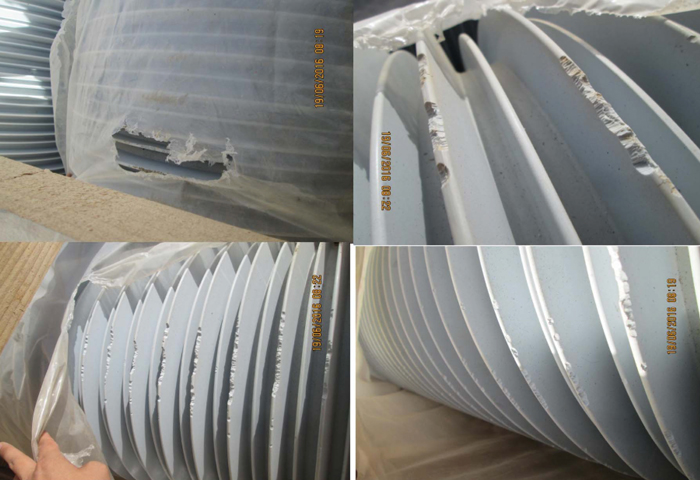
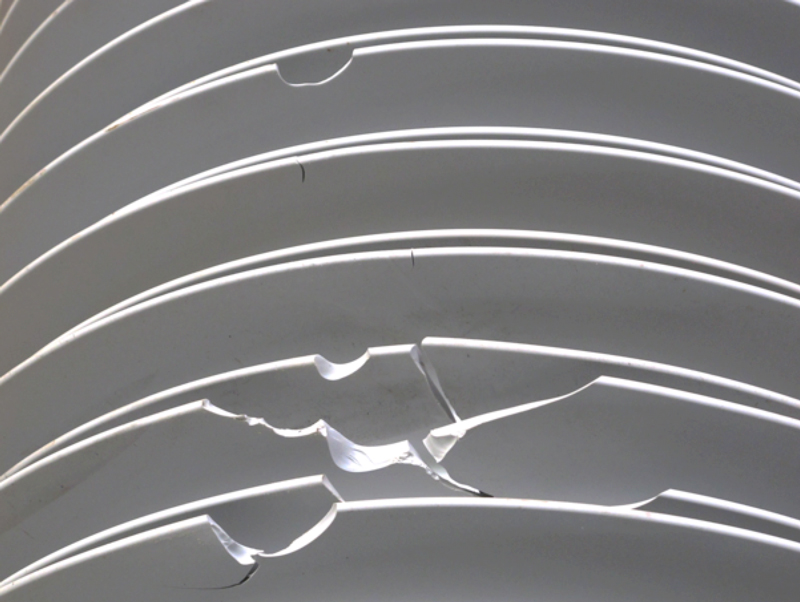
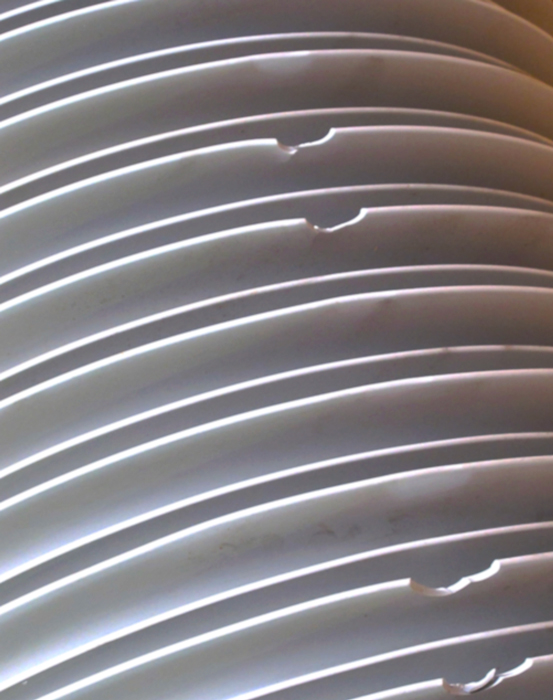
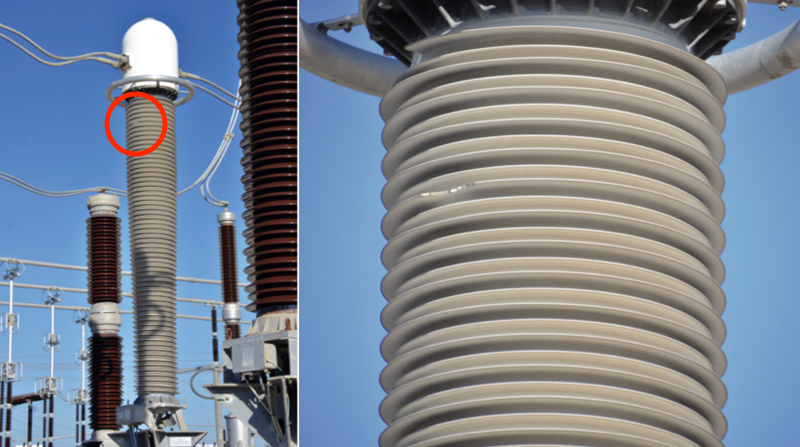
Fortunately, most gouges and tears to the sheds of silicone housings do not signal irreversible damage and can be repaired in the field following instructions of their manufacturer. But the ongoing incidence of such cases understandably remains an area of concern for their successful application.
Even after decades of rapid growth in application of composite insulators, no user should take for granted the need to always handle them with the proper care.