Application of RTV silicone coatings to porcelain and glass insulators in order to increase their pollution performance has been available for decades. Yet not everyone in the industry still appreciates how this coating technology operates and what factors will determine performance and effective service life.
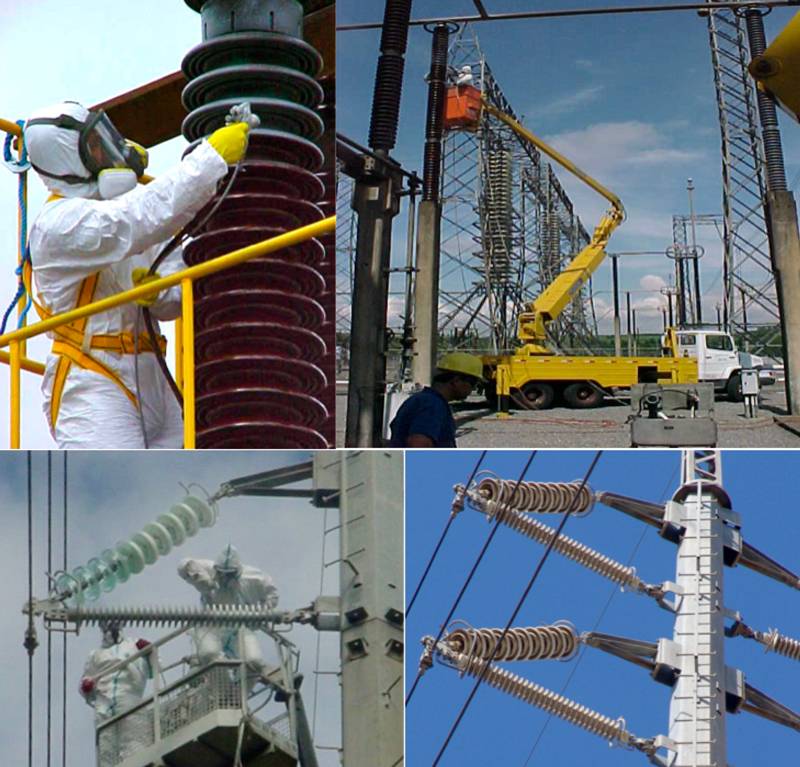
Why the Need for RTV Coatings?
The simple answer is that the large share of existing power infrastructure across the globe – even operating in zones of high contamination – is equipped with porcelain and glass insulators. Depending on how well designed these insulators have been for their operating environment and on the efficacy of natural cleaning by rain or wind, they should require little maintenance beyond periodic inspection.
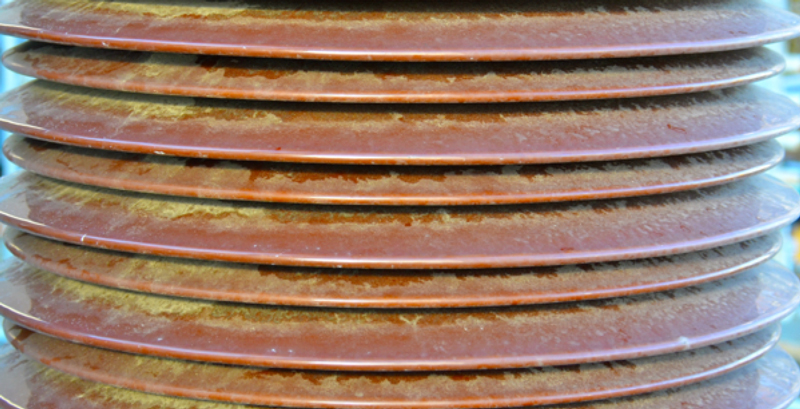
There are however many situations where substations or lines operate in areas where the pollution exposure has increased over time, due for example to construction of nearby industrial areas and highways. This type of human activity can dramatically impact the level of pollution affecting a line or substation. Something must be done or there will be elevated risk of flashovers.
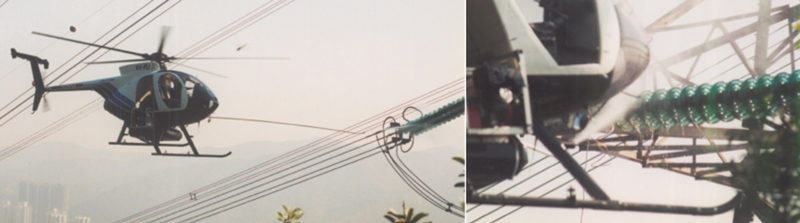
Another consideration promoting growing interest in coatings is the high cost of washing insulators in polluted service areas. With fresh water an increasingly scarce resource and labor costs of washing from truck or helicopter going up as well, the relative economic benefit of applying RTV coatings versus periodic cleaning has grown significantly. Yet another factor behind more utilities opting for RTV is because it offers a combination of the electrical performance of silicone with the long-term reliable mechanical performance of porcelain and glass. Finally, not all power utilities are yet comfortable with the long-term behavior of composite insulators, especially in highly polluted areas with frequent wetting, persistently high UV or where bird pecking is a serious problem. In some countries there is also concern that composite insulators can be damaged by workers who cross them to carry out maintenance on conductors.
>What is the Principle Behind RTV Coating?
A thin layer of RTV material adhering to porcelain and glass insulators vastly increases pollution withstand since the silicone imparts hydrophobicity to what would otherwise be a hydrophilic surface. Moreover, since the silicone contains low molecular weight chains that continually migrate from the bulk coating to the surface, the ceramic insulator will remain hydrophobic even when covered by a layer of pollution.
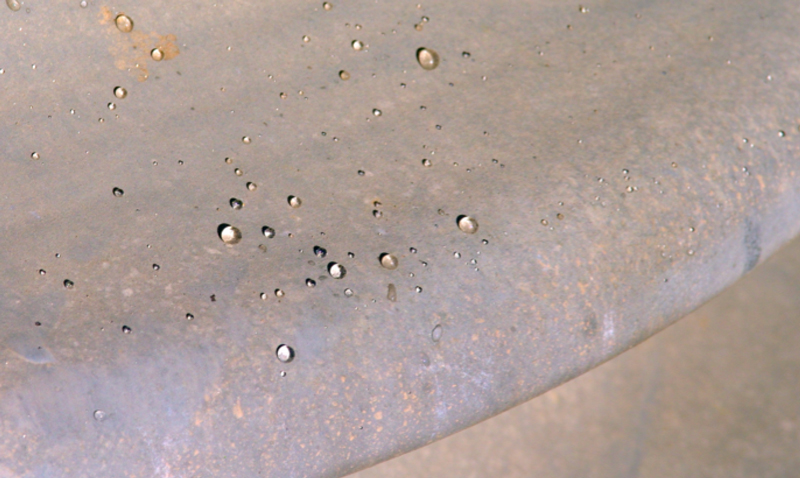
How Long Does an RTV Coating Remain Effective?
That of course is the key question when comparing the relative costs of coating by RTV silicone material versus alternatives such as washing or using silicone grease. Unfortunately, there is still no standard answer since much will depend on the quality of the coating material and particularly on how it has been applied. Fortunately, these variables are both under the control of maintenance personnel.
Assuming the RTV silicone material has been formulated by a competent supplier and is applied by trained personnel under controlled conditions, it is certainly reasonable to expect at least 10 to 12 years of effective service life, possibly longer. For example, coatings applied in the late 1980s/early 90s on bushings at a highly polluted 230 kV substation in Ontario, Canada operated for much longer than had originally been anticipated.
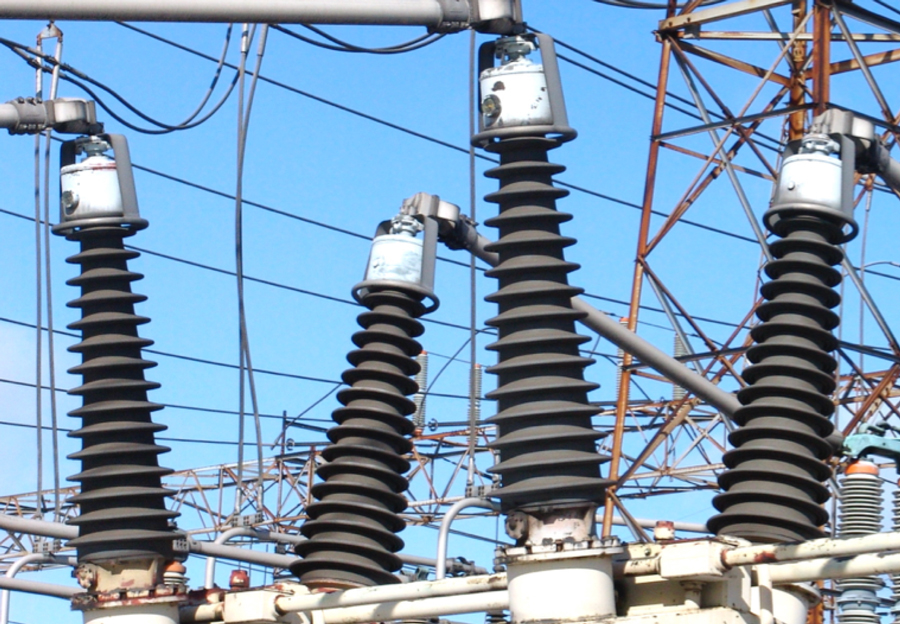
What is Required for Effective Coating Application?
In the best of circumstances, RTV coating would be applied under ‘factory conditions’, with careful control of ambient temperature and humidity as well as application thickness. This however is clearly not feasible for most substation applications and therefore the key is good coating practice. This includes thorough cleaning of the ceramic insulator surface to remove any dust or grit prior to coating to ensure optimal adhesion. Surface preparation is critical and therefore should be monitored closely. Since conventional adhesion tests employed by the coatings industry do not apply for silicones, other methods such as the cross-hatch test or water blast adhesion test are used.
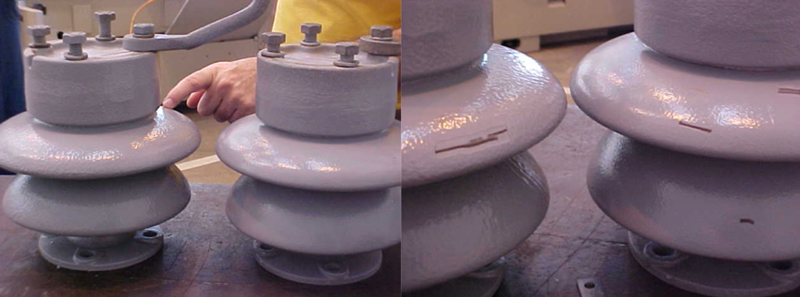
It is also necessary to ensure optimal spray thickness along with consistent coverage to avoid uneven voltage distribution developing along the insulator surface under wetting conditions. Too thin or too thick a layer are both less than optimal. That is why some suppliers of coatings recommend using their own experienced staff to carry out application.
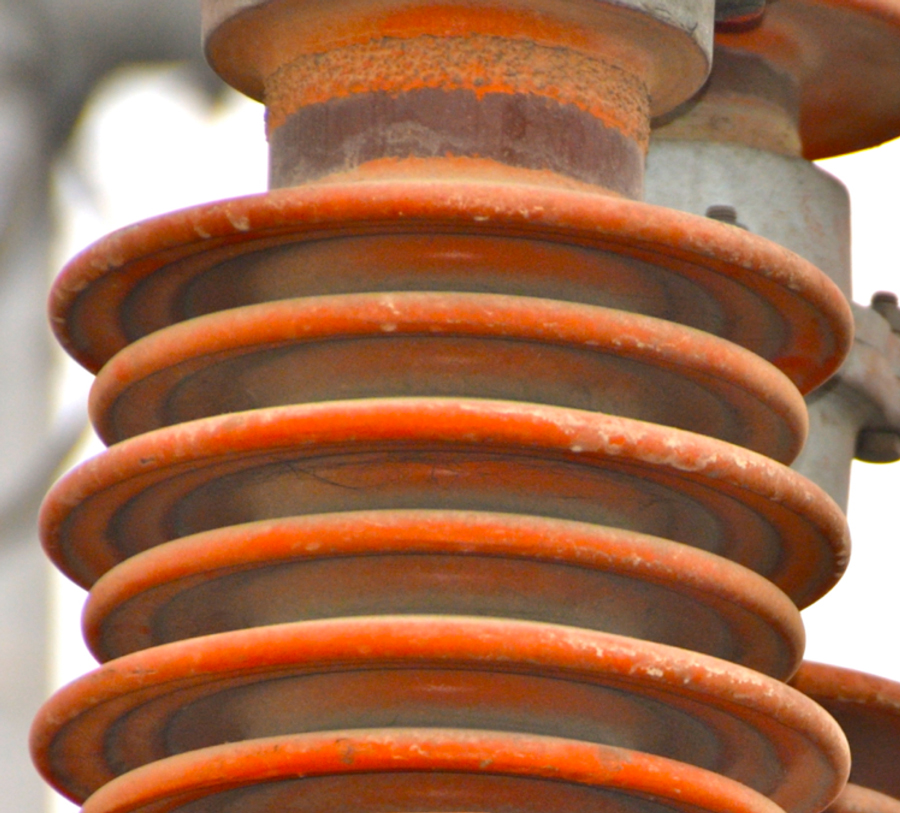
Do RTV Coatings Need to be Cleaned?
Much will depend on the type and rate of pollution that accumulates on them. If there is an exceptional event that deposits a great deal of pollution at one time, cleaning may be advisable since hydrophobicity could temporarily be reduced or even lost. High pressure washing, however, should be avoided since this can damage a coating. Obviously, if RTV coated insulators required cleaning nearly as frequently as uncoated insulators, there would be little logic in using this solution.
What Are Signs of End-of-Life?
Simple visual inspection may provide clues as to the condition of the coating, especially is there is evidence of large portions flaking off.
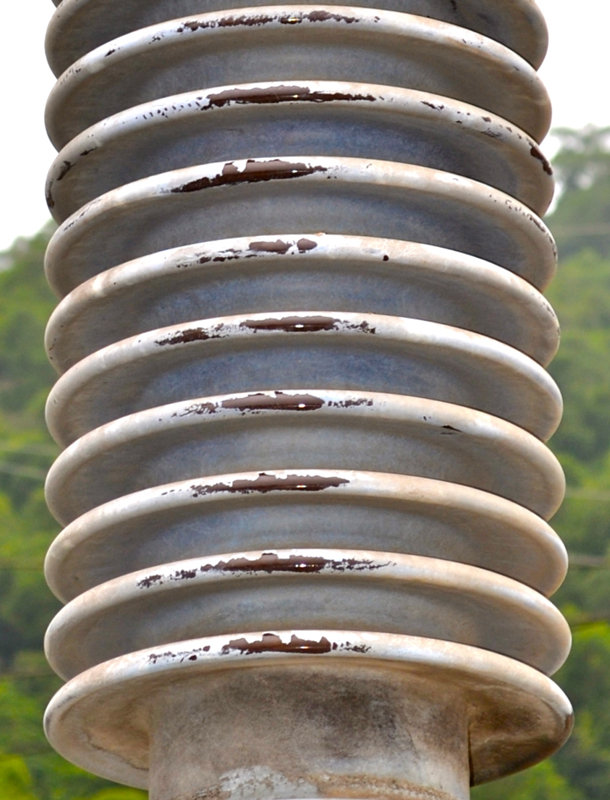
Also since the major benefit of the coating lies in transforming a previously hydrophilic ceramic surface to one that has hydrophobicity, one useful measure of end of life would be permanent loss of hydrophobicity. This can easily be monitored by simple hydrophobicity measurements conducted during routine station maintenance shutdowns. End of life can also be monitored via direct leakage current measurements and indirectly via thermal imaging, best taken during periods of light surface wetting. Since the goal of the coating is to limit leakage current, indirect thermal imaging gives an indication of the presence of surface currents.
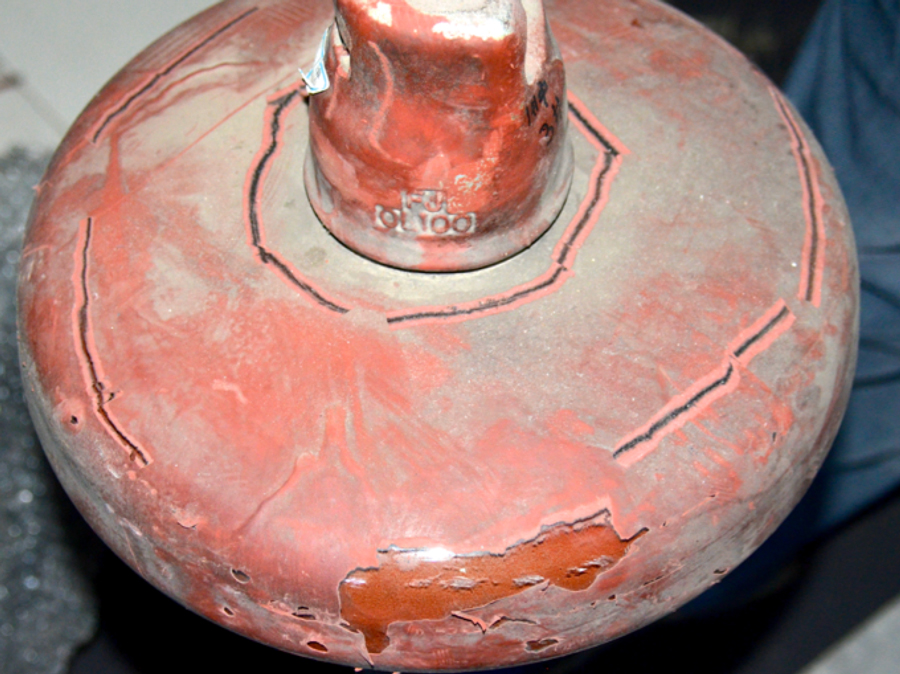
Monitoring end of life of RTV coatings on overhead line insulators is more challenging. Close-up inspection of sample insulators removed at random from different sections of line will provide useful information on coating condition as well as on its residual hydrophobicity.