[inline_ad_block]
Most application of RTV silicone material has traditionally been as a remedial measure to mitigate pollution-related flashovers of insulators suffering poor service performance. Indeed, coatings have been viewed for years mainly as a maintenance product applied to substation insulators in polluted areas in place of greasing or washing. By contrast, in situ application of RTV material to cap & pin strings on overhead lines has always been perceived as problematic due not only to the working height but also because of the difficulty in applying the coating evenly to the underside of each disc. But recently there has been growing interest to coat toughened glass cap & pin insulators at the time of their manufacture so as to give them a uniform, highly adherent hydrophobic surface before being put into service. This solution is now being applied with good results, as illustrated for example in papers published by IEEE DEIS Outdoor Insulation Technical Committee and by Committee members on DEIS IEEE Transactions. The authors estimated that several million RTV coated cap & pin insulators are already in service. Of these, more than one million are factory pre-coated glass discs – of which hundreds of thousands are installed on AC HV and EHV lines belonging to Italian grid operator Terna. In addition, thousands of such insulators were part of a field trial on Terna’s HVDC lines. Service experience has been positive and at those sites where pre-coated insulators replaced conventional glass strings, regular washing is no longer deemed necessary. Similar experience has been reported in the Americas (e.g. U.S. and Peru), the Middle East (e.g. Qatar and Saudi Arabia) and China, where these insulators are installed in heavily polluted areas.
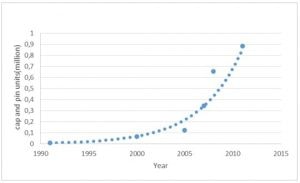
CLICK TO ENLARGE
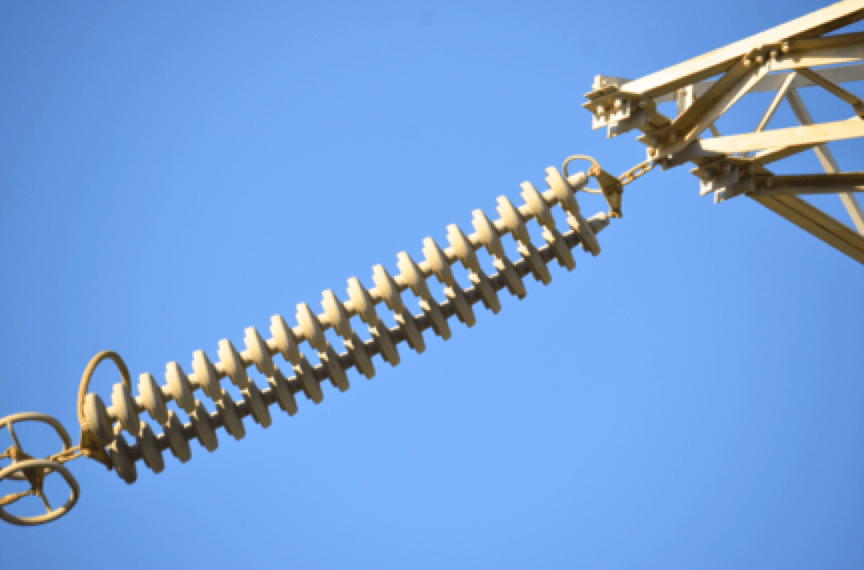
CLICK TO ENLARGE
The growth of such installations worldwide appears exponential, indicating positive market response and positioning pre-coated glass insulators as an alternative to silicone composite types. It should be noted, however, that the number of strings corresponding to about one million pre-coated cap & pin discs is still less than 100,000. This is orders of magnitude lower than the current market for composite insulators. Up to now, pre-coated ceramic insulators have been used mainly as a remedial measure for refurbishing existing lines with unsatisfactory pollution performance. Expanding their application to new projects will therefore require comparing life cycle costs of insulator alternatives and listing the pros and cons of each in terms of acquisition cost, maintenance costs (including diagnostics and live-line work) and replacement cost at end of life.
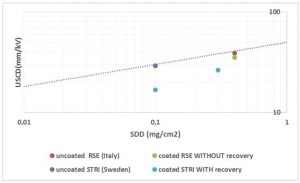
CLICK TO ENLARGE
As emphasized in the IEEE papers, coating quality is critical to assure good service performance. This means that the formulation of ingredients must assure good tracking and erosion resistance while also maintaining long-term hydrophobicity. Final quality is also determined during the production phase since every glass disc must be perfectly clean before applying the RTV material. Moreover, the coating should be sufficient as well as uniform in thickness, i.e. more than 280 μm at the bottom of each glass disc and more than 350 μm on the upper surface. Post-application curing of the layer must also be conducted under proper temperature and humidity. Lastly, quality should be verified by suitable tests based on available guidelines. In particular, in 2002 IEEE issued Standard 1523 “IEEE Guide for the Application, Maintenance and Evaluation of Room Temperature Vulcanizing (RTV) Silicone Rubber Coatings for Outdoor Ceramic Insulators”). Similarly, CIGRE has issued Brochure 478-2011 dealing with “Important Material Properties of RTV Silicone Rubber Insulator Coatings”. The above Guidelines, however, are not yet directly applicable to pre-coated insulators and no internationally agreed specification is yet available for qualifying such insulators.
The IEC 62896 Technical Specification “Hybrid Insulators” that deals with insulators consisting of an insulating mechanical load-bearing core protected by a defined polymeric housing geometry explicitly excludes RTV coated ceramics. Still, useful indications for specifying pre-coated insulators are given in the above-mentioned IEEE papers. These include visual inspection as well as tests to verify adhesion and thickness of the coating and also tracking and erosion properties. Guidelines are also provided for suitable packing, shipping, installation and subsequent maintenance. In particular, reproducible and representative pollution tests have yet to be defined for coated insulators, as is still the case for polymeric insulators as well. Tests are being looked at that best simulate real service conditions since quite different results can be obtained depending on test conditions.
Alberto Pigini