Today, distribution arresters are typically viewed as a commodity where technology has reached the point where there are few failures due to poor materials, design or quality control. In such an environment, it has become increasingly difficult for manufacturers to differentiate their products from those of competitors since buyers are often not prepared to pay a premium for superior materials or quality. At the same time, some utility customers who in the past purchased arresters based only on price were not always satisfied with what they received and experienced higher failure rates, unplanned replacement costs, unprotected lines or damaged equipment. Especially in developing countries looking to attract ‘high-tech’ industries, utility engineers look carefully into expected performance of critical components such as arresters and are not influenced solely by price.
This contribution compiles articles and information reported in past issues of INMR.
Technology Development
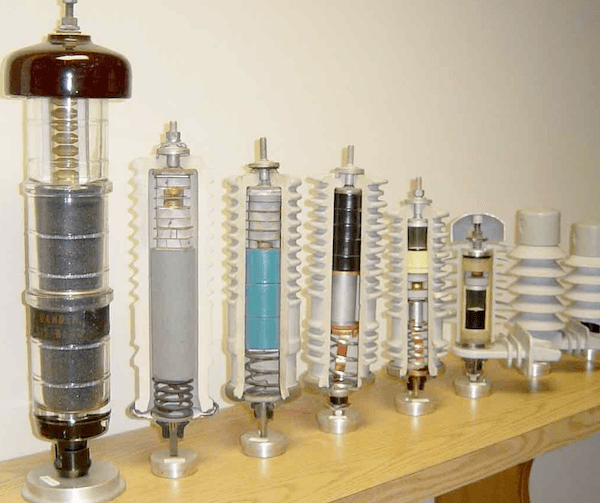
There have been two fundamental shifts in technology for distribution arresters over the past 30-40 years years. One has seen substitution of metal oxide varistors in place of the silicon carbide gap-type designs dating from the 1950s. The second has consisted of virtually total replacement of porcelain by polymeric materials as the external housing. Together, these changes have completely transformed the appearance and performance of modern day arresters at distribution voltages.
1. Changeover to MOV Technology
Application of metal oxide varistors to power systems was the outgrowth of discovery of this technology for low voltage electronic applications. As has been the case for many breakthroughs, this was an accidental discovery during research into linear resistors. Initial utilization of zinc oxide varistors for arresters focused on higher voltages and particularly for station arresters since it eliminated the complexity of manufacturing the series gaps for equivalent silicon carbide units. Due to the economic benefit in replacing the gaps with this new technology, by 1976 metal oxide arresters had begun to replace silicon carbide gap technology for most station applications. However, transition toward metal oxide technology at distribution voltages took longer and began only during the mid 1980s. The reason for the delay was the need to re-engineer the technology to make it simpler so that it could become an economic alternative to gap type units under the less demanding requirements of most distribution applications.
But once metal oxide technology had been successfully transferred to distribution arresters, the gap design was quickly replaced in these applications. This was because it was not economically practical for manufacturers to have separate production lines employing such different technologies. Suppliers were forced to make a choice among the two and history demonstrated that those who made the investment to change over to MOV technology prospered; those who continued to produce only gap designs soon disappeared from the market.
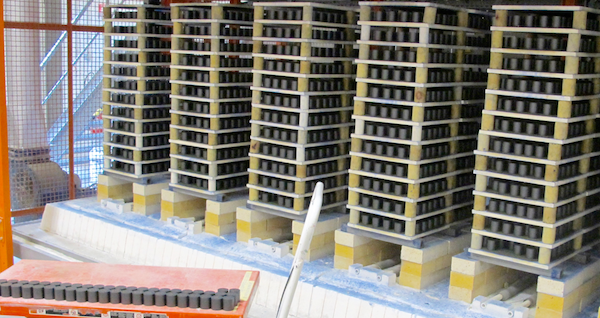
Metal oxide varistor blocks are the key component in modern day distribution class arresters. These consist of a mixture of metal oxides, with ultra pure zinc oxide being the primary constituent. The other metal oxides exist in far smaller concentrations, down to only a few parts per million. These various metal oxides and other ingredients are mixed together in spray drying equipment designed to ensure a highly homogenous mixture and then compressed into blocks under great pressure. Considerable know-how is required to adjust the compressive forces to ensure that blocks maintain their perfect homogeneity during this critical step. After pressing, subsequent production steps vary somewhat from one manufacturer to the next. Typically, blocks pass through a tunnel kiln at high temperatures in a process known as sintering and where their volume can be reduced by as much as 20 per cent. The blocks are subjected to acid treatment and electrodes are sprayed onto their surface. Finally, a high quality crystalline glass is applied followed by more treatment in the kiln.
Due to the specialized equipment and technical know-how required to produce consistently high-quality blocks at competitive cost, the business of producing these and the business of producing the final arresters have taken divergent roads. Only the largest suppliers of arresters could justify the investments needed to set-up sophisticated production lines for blocks while the remainder found it more practical to purchase blocks externally. There is a market barrier to entry into the block supply field due to the capital required and the fact that it is difficult to maintain consistently high quality. This pattern of purchasing blocks on the open market does not always apply to arrester manufacturers in some countries where there is still a philosophy of being self-sufficient in strategic components.
In some countries, there are domestic arrester manufacturers who make their own metal oxide blocks in processes with less automation and sometimes less sophistication than found among major suppliers. To a large extent, local arrester price levels combined with lower labour rates make it difficult for such suppliers to buy blocks from sources outside the country and still remain competitive. Today, while metal oxide varistors can more or less be regarded as a commodity, the technical characteristics of blocks from different suppliers are not identical. There remains need for close technical relationship between block supplier and arrester manufacturer.
Ironically, the superior protection offered by metal oxide arrester technology means that these arresters are more vulnerable to one type of line overvoltage problem – ferroresonance. This phenomenon of prolonged overvoltage occurs on some networks comprised of relatively long lines with non-synchronous switching. In south-east Asia, for example, at the time of conversion to metal oxide arresters, there was one incident where all new MOV arresters on one phase of a 30 km line failed at the same time. Researchers analyzing the situation concluded that a lightning strike triggered prolonged overvoltage due to ferroresonance. Older spark gap units on this line were unaffected since, notwithstanding the overvoltage, the critical sparkover voltage was not reached. Therefore, they offered no protection in this type of situation. While the spark gap units survived, the equipment which they were intended to protect was subjected to unnecessary stresses, possibly causing premature ageing. MOV arresters well-dimensioned for their application are almost always sacrificed under ferroresonance because they are more sensitive to such incidents. But this situation is rare and can be controlled by line designers using circuit breakers as well as resistors to dampen the phenomenon.
2. Transition to Polymeric Housings
The second major technological development in distribution arresters has been the complete shift from porcelain to polymeric housings – a trend that began by the late 1980s. In fact, the complete changeover to polymers in this application is nothing short of remarkable given that the utility industry is conservative and requires a lot of field experience before adopting any new technology. The relatively fast conversion is testimony to the fact that this technology really addressed the problems experienced in the field. Polymeric insulators have been available for much longer than polymeric-housed arresters yet have still not achieved such conversion away from traditional ceramic materials. Industry experts agree that polymers in this application have no real disadvantage compared to porcelain and are superior in terms of pollution performance, safety and sealing against moisture ingress.
Polymeric Housing Materials
Once the transition from porcelain to polymeric housings for distribution arresters had become complete, the topic of interest became the relative performance of alternative polymers. Basically, major categories of polymeric materials used as housings for distribution arresters include: silicone rubber, ethylene propylene diene monomer (EPDM) and ethylene vinyl acetate (EVA). Data on which material dominates sales are difficult to obtain, however silicone rubber is likely the housing found on the majority of distribution arresters. While the relative performance of these polymeric housing alternatives is still debated, most feel that silicone rubber has ideal properties that justify its use in spite of a higher cost. For example, silicone has a higher bonding energy than EPDM making it less vulnerable to being broken down by UV radiation and ozone. Moreover, due to long-term hydrophobic properties, it performs better under conditions of high contamination.
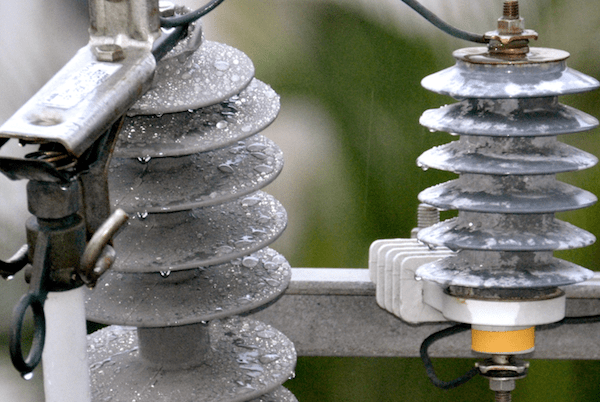
Arresters made with EPDM and blends also have a share of the market due to cost. Many utilities have a philosophy that a distribution arrester can be allowed to fail in which case it is simply replaced. Moreover, some countries change distribution systems relatively rapidly with the re-configuration of growing cities and a 10-15 year life expectancy may be considered acceptable. This contrasts with other places such as Europe where utilities expect a distribution arrester to stay in service for over 30 years.
In the early days of polymeric arresters, silicone suppliers did not always compound materials for an optimal mix of dielectric performance, hydrophobicity and speed of its recovery after stress. Today, these issues have been resolved and most silicones have excellent properties in all respects. The same point can also be made about the evolution of EP rubbers. First generation polymeric arresters made with EPDM or similar materials were sometimes adversely affected by UV, high pollution and humidity. Material suppliers looked at how formulations had to be adjusted to avoid such problems. As for hydrophobicity, which EPDM loses rapidly and never recovers, this may not be a serious issue for all distribution arrester applications because specific creepage distances are often more than sufficient. Also, voltage stresses are not there across such an arrester. Any chalking or discolouration of EPDM arresters after some time in the field is due to the aluminum trihydrate (ATH) filler and does not indicate tracking or erosion. EVA is a proprietary housing material that has not changed much in composition for years.
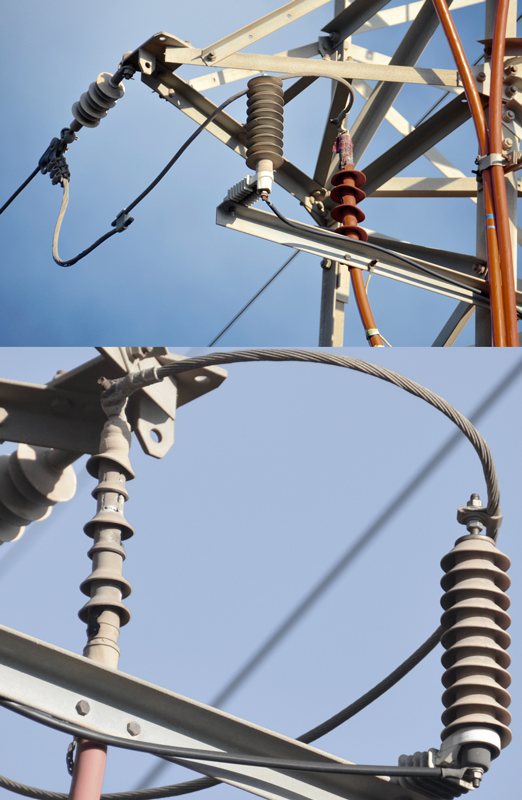
In the early days of polymeric arresters, silicone suppliers did not always compound materials for an optimal mix of dielectric performance, hydrophobicity and speed of its recovery after stress. Today, these issues have been resolved and most silicones have excellent properties in all respects. The same point can also be made about the evolution of EP rubbers. First generation polymeric arresters made with EPDM or similar materials were sometimes adversely affected by UV, high pollution and humidity. Material suppliers looked at how formulations had to be adjusted to avoid such problems. As for hydrophobicity, which EPDM loses rapidly and never recovers, this may not be a serious issue for all distribution arrester applications because specific creepage distances are often more than sufficient. Also, voltage stresses are not there across such an arrester. Any chalking or discolouration of EPDM arresters after some time in the field is due to the aluminum trihydrate (ATH) filler and does not indicate tracking or erosion. EVA is a proprietary housing material that has not changed much in composition for years.
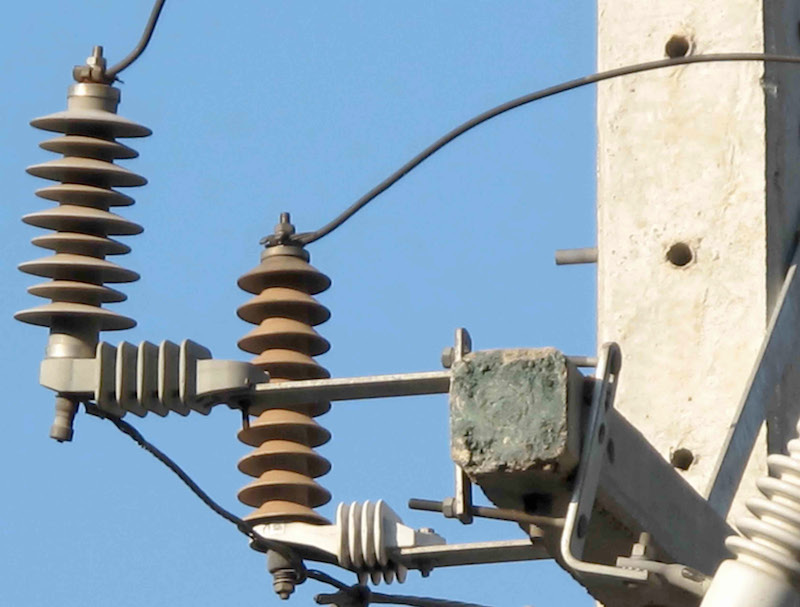
It is difficult to demonstrate that one housing material will always outperform another, whatever the service environment. Moreover, even if this were possible through some controlled test, the value of such findings would be questionable because other parameters in arrester design also play a role. To put the whole issue of alternative housing materials into context, discussion in the past focused mainly on polymers versus porcelain. Suppliers of polymeric arresters were highlighting how these housings offered superior properties to porcelain. Now, however, it is other variables that are important. Performance of an arrester in the field depends not only on material but also on design and how it has been finished in the production process. A good material is not a substitute for bad design while an inferior material with greater creepage may perform equally well. When arresters have the same housing material and same creepage, performance is mostly a question of design.
Design Features
The failure of a polymeric arrester is rare, estimated at less than one failed unit per 1000 per year. However, since millions of such arresters are in service, that still means a high number will fail each year. The most important variable determining failure rate is level of isokeraunic activity in the region where the arrester is installed. In this respect, the arrester will have operated and absorbed an overvoltage from a direct strike and failure (or sacrifice) of the arrester is not related to quality. However, other factors that are controllable also influence failure and, more significantly, failure mode. Typically, these relate to arrester design and construction.
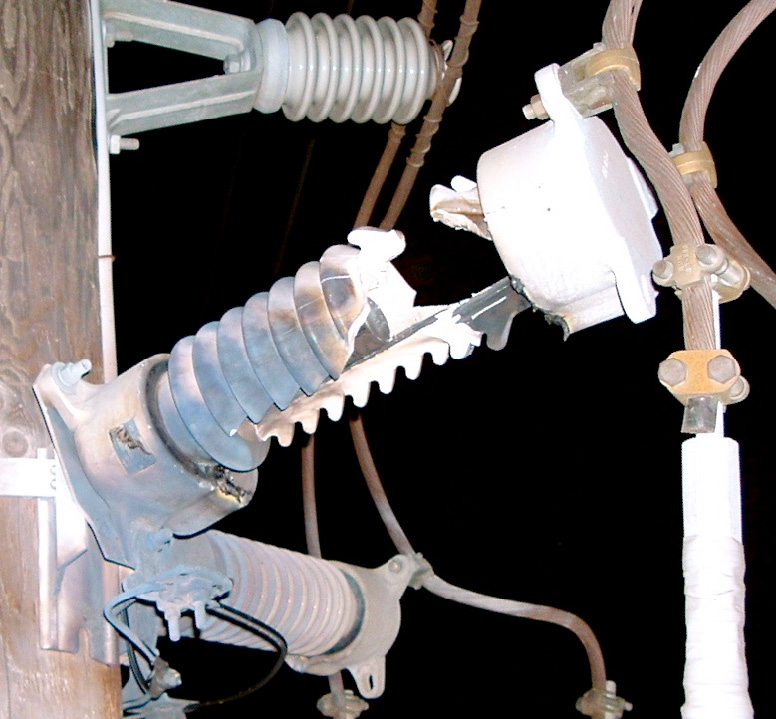
In the realm of construction, one of the key features in design is how the metal oxide blocks that comprise the varistor column are bound together mechanically. A second is how the external polymeric housing is applied over this column. Production methodology used to mechanically contain the varistor column can greatly influence pressure relief behaviour in event of internal short-circuit. This is one of the most critical performance characteristics and explosive shattering of porcelain-housed units was in fact one of main reasons this material was so quickly replaced.
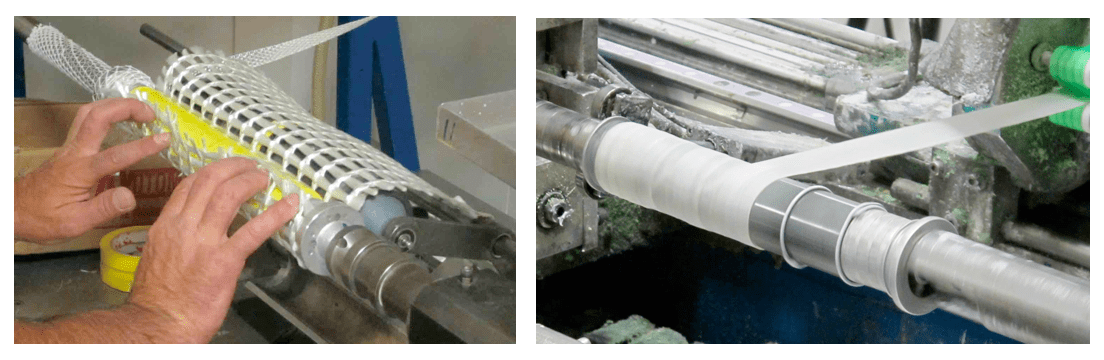
Two general methods of metal oxide column containment are utilized, although the specifics of each vary among suppliers. In the more widely utilized of the two – the wrapping approach – a fiber glass cloth impregnated with uncured epoxy resin is wound over the blocks in a number of layers and under high tension. Some suppliers take this filament wound process a step further by overlaying a polymeric tape over the cloth, also under tension. The wrapped column is heated in an oven so that the resin within the tape will cure. In the case where a polymeric tape is also used in the overwrap process, this shrinks from the heat and applies great compressive forces to the column, thereby squeezing the now less viscous resin through the cloth. This is intended to push out any air that may have become trapped during initial wrapping.
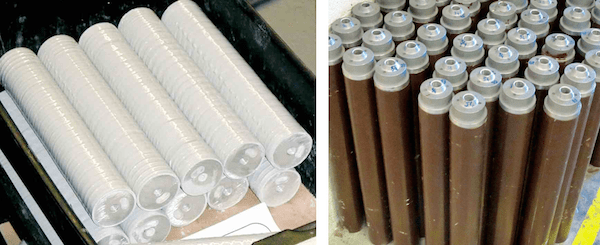
The glass fibers are now bonded directly onto the sides of the metal oxide blocks, resulting in high mechanical strength under cantilever and allowing the arrester to support a heavy load under tension. In a variant of this approach, other suppliers compress blocks in an axial direction and dip them into dry powdered epoxy. A fiber glass reinforcing cloth is applied and the whole unit impregnated and bonded into a cylinder.
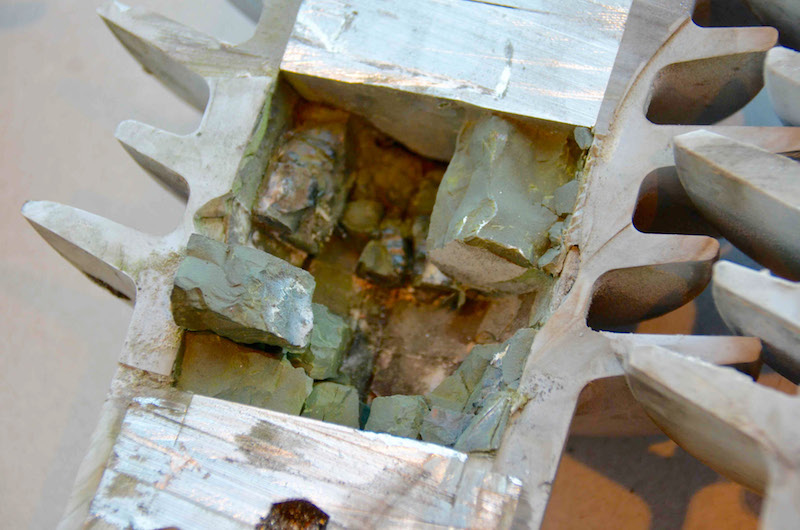
One potential problem with wrapping the blocks this way is that should a short-circuit develop within the blocks, the internal pressure and gases generated cannot easily escape. This can result in violent explosion with the possibility that parts of the cured epoxy resin or of the blocks themselves can be ejected at high velocity. Manufacturers who employ this method defend the wrapped column design stating that the open weave in the wrapping fabric permits pressure generated from an internal arc to be released without explosion. Actually, there is a compromise when using the wrapping technique since it is desirable for modules to be as strong as possible, implying using a lot of wrap. But if there is too much wrap, gases generated from an internal short circuit will not be able to escape. In this respect, more openness is preferred. Ultimately, the arrester supplier must look for a package which offers good axial capability while also allowing gases to escape.
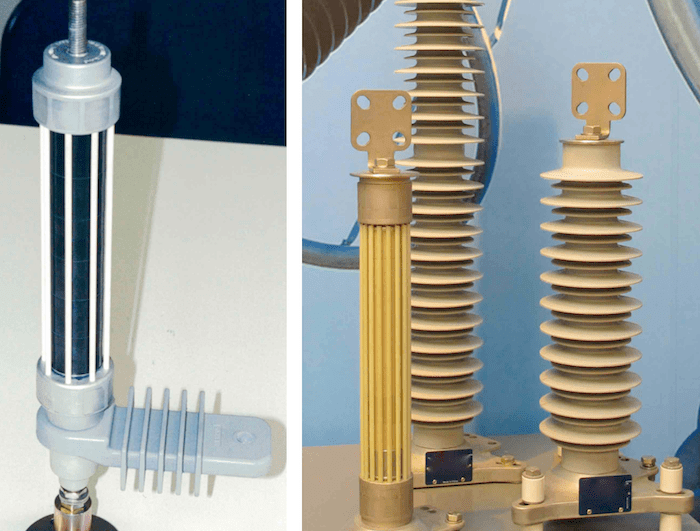
A second methodology for block containment – the cage approach – sees fiber-reinforced straps bound tightly around the varistor column, forming a cage for both the column and the two end electrodes. According to suppliers who employ such a construction, this design is an effective way to maximize safety against explosion since a power arc simply burns through the external housing without possibility for significant build-up of pressure. Yet another block containment philosophy utilized by smaller manufacturers involves use of a pre-fabricated fiber glass tube to surround the blocks, much as was done in the past with porcelain. The tube is attached to the contacts at either end of the varistor column and the polymeric housing is slipped over. In such a design, some form of venting must be allowed to deal with pressures generated by internal power arcs.
Role of Disconnector
Most distribution arresters sold today – especially those in the Americas – are equipped with a disconnector device that separates the ground lead to ensure that arrester failure does not necessarily cause a permanent outage. Also, there is visible indication for maintenance staff of the need to replace the arrester. Not all utilities throughout the world want this feature, however, some preferring to have the line taken temporarily out of service in the event of arrester failure due to factors such as a direct lightning strike. This is the case in a number of European countries.
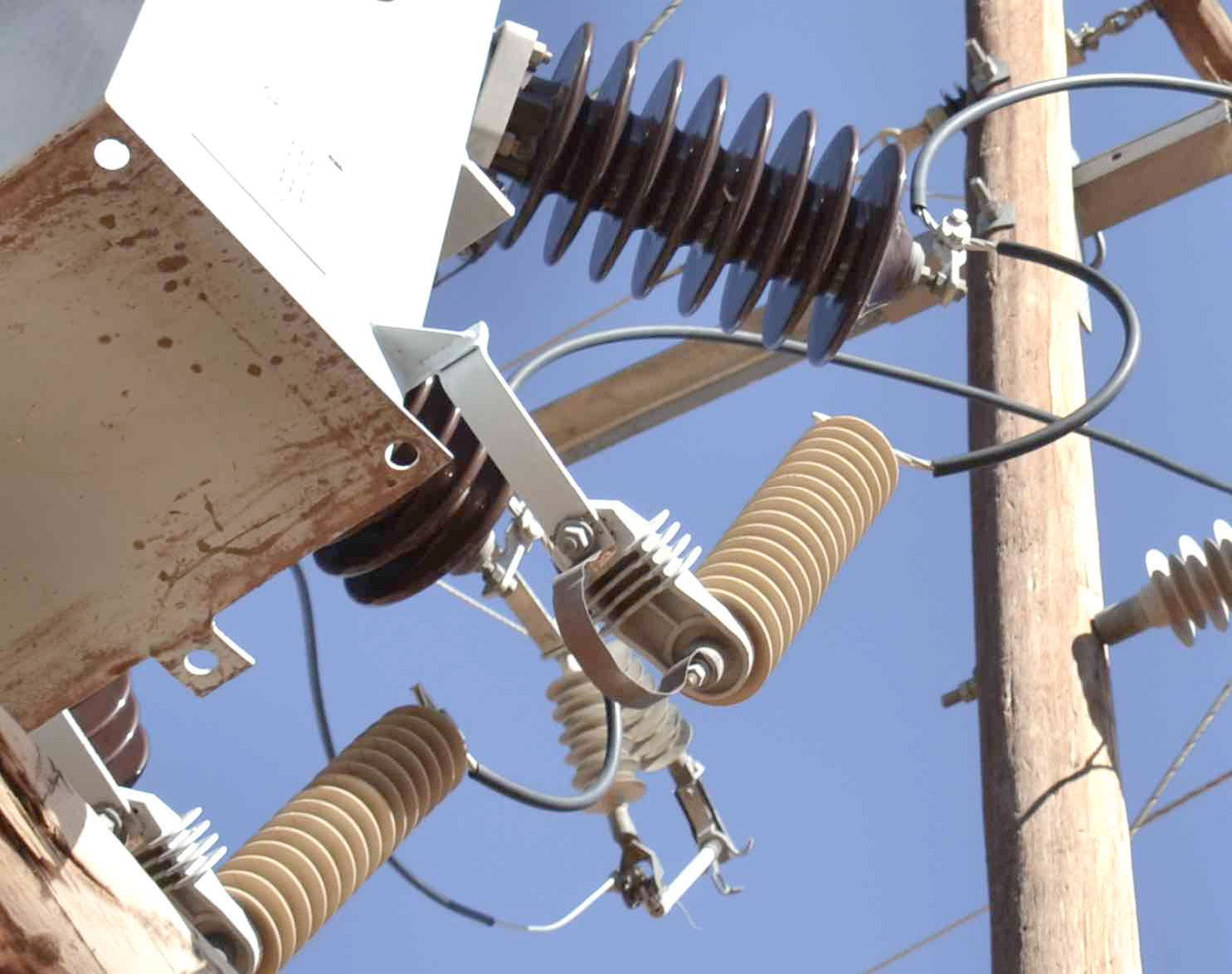
The disconnector on a distribution arrester is specialized and should not be regarded as a standard accessory. Rather, its design must incorporate features to meet the operating requirements of utilities, which emphasize not only lower numbers of interruptions but also interruptions of shorter duration. The disconnector unit must be strong enough to withstand normal surges yet operate quickly whenever these are of a magnitude that overwhelms the arrester. Indeed, disconnectors are a point of differentiation between various suppliers and a key design element of a distribution arrester. For example, some power utilities have looked to change their arrester supplier solely because they were dissatisfied with the slow operation (i.e. less than optimal time/current curve) of the disconnectors that were part of the units purchased. As a result, overvoltage situations that resulted in arrester failure often triggered operation of breakers – a situation they did not want. One of the past concerns of the arrester industry related to the fact that disconnectors operate on the basis of a temperature-triggered tiny explosive charge and can present difficulties in being shipped using normal channels.
Alternative Manufacturing Processes
Apart from different philosophies for containment of the metal oxide blocks, the second major construction variable in a distribution arrester is how the polymeric housing is applied to the bound internal varistor column during final production. Two principal types of production technologies have emerged. The more widely utilized could be referred to as the slip over technique since it sees a pre-manufactured hollow cylindrical polymeric housing pulled or stretched over the contained blocks. The second method could be called the direct mold technique since here the housing is molded directly over the column under some combination of pressure and temperature. These two manufacturing technologies play a fundamental role in many variables since they influence relative production costs, consistency of quality and production lead times.
Slip Over Technique
The specifics of how polymeric arresters are manufactured utilizing the slip over technique depend on the production technology and experience of the supplier. They are also, to some extent, determined by the type of polymer from which the housing is made. For example, some manufacturers stretch a pre-manufactured silicone housing over the smooth varistor module. EPR materials such as EPDM are claimed not have sufficient ‘stretchiness’ to allow such a process. Another production technology sees the varistor module inserted into the polymeric pre-molded housing while it is being inflated and as a silicone grease-like compound is pushed through. This is similar to a process used in insulator manufacturing where an FRP rod replaces the module.
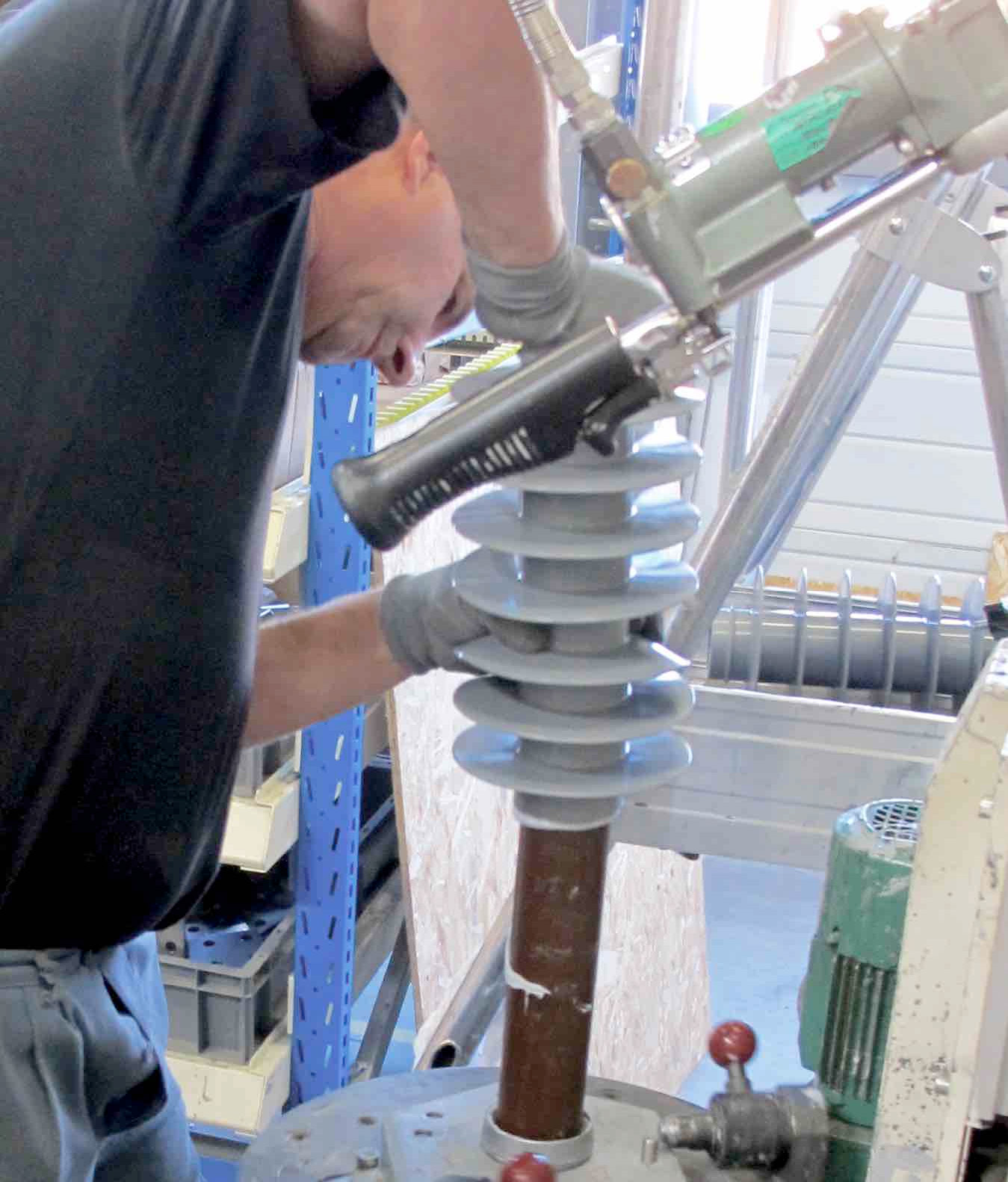
One of the key features of this process is ensuring that no voids are created between module and housing. Yet another variant of the slip over methodology sees the polymeric housing heat shrunk directly over the wrapped metal oxide column. When performed properly, this process ensures that there is no trapped air. Running a molding process for housings separate from the final production of the arrester is said to contribute to efficiency, flexibility to achieve different configurations and creepages and shorter lead times. Suppliers who follow this methodology look to ensure full utilization of the pre-molded housings, typically made in long sections and cut to fit the specific arrester. This contrasts with direct molding over the varistor where different molds might be needed for every different housing geometry.
Direct Mold Technique
The second general method for applying housings to an arrester is to mold them directly onto the varistor column. Direct molding was the alternative selected by most suppliers who changed their product lines from porcelain to polymeric housings. A manufacturer that possesses the competence to produce silicone in a mold is in a position to use this manufacturing approach, although it requires large investment in molding machinery. Production volumes must therefore be high since it may not be economically feasible to mold special, low volume designs.
Silicone is the polymeric material said to best lend itself to the direct mold approach since pure EPDM typically has higher stiffness that can make it difficult to remove from the mold cavity, especially for special shed profiles. Two types of silicone are utilized: high temperature vulcanized (HTV) and liquid silicone rubber (LSR). The electrical performance and ageing characteristics of the two are similar and choice as to which any direct mold arrester manufacturer will employ depends on process requirements. HTV is more viscous and requires higher temperatures as well as greater pressures. Although less costly than LSR, the equipment and molds necessary to process it are more expensive. In this regard, machinery and know-how available to the manufacturer determine which grade of silicone is preferred. Since direct molding typically means using a silicone housing and since this material has a relatively high water diffusion rate, it is critical to manage the molding process to ensure complete absence of internal voids. Partial discharge testing of units is then a mandatory part of production control.
Given the division within the arrester industry among the two alternative production technologies, i.e. slip over versus direct mold, there are differing opinions as to their relative advantages and disadvantages. According to some, since the rubber mass must reach high temperatures, molding hollow housings on a hot steel mandrel for use in slip over production makes it easier to obtain consistently well-cured parts. This may be more difficult when molding directly over a cold varistor module. Another challenge in direct molding is maintaining good bonding along the entire length of the varistor column. Direct molders counter that during arrester production it is critical that no air gaps form between internal column and housing. Since slip over methodology is less automated than direct molding, suppliers using this method must master the process and quality depends greatly on worker skill. In the end, from the user point of view, what is more important is not which manufacturing methodology is used but rather how well the process is monitored and controlled. Final finishing of the arrester after manufacture is another area requiring attention. The supplier should ideally clean off any mold lines from the housing after removal from a mold to ensure they do not become an area where pollution can become trapped. If so, a conductive pathway could eventually be formed possibly leading to flashover. Moreover, with whatever production methodology, the interface between polymeric housing and metallic end hardware must be made completely impervious. Moisture getting inside and causing tracking between rubber and blocks is a main cause of arrester failure.
Future Expectations
There is a consensus that distribution arrester technology is mature and that the basic design of these arresters has reached the state-of-the-art in terms of cost-effective manufacturing and high quality of materials. Although this technology has been employed since the mid 1980s, there do not appear any breakthroughs in displacing basic components such as zinc oxide blocks or polymeric housings. Rather, the emphasis by suppliers will remain focused on issues such as more automated manufacturing and testing for high volume production and also refining processes for reduced cost, higher yield and better reproducibility.
Suppliers that succeed in this field will be those that have mastered the process and control all the costs. This may involve looking into material formulations to identify opportunities for faster curing and reducing cycle times. Also, developing a more flexible manufacturing process will enable major global suppliers to offer a single platform technology that, while using the same basic components, can modify design to meet special user needs.

One area where industry observers see opportunity for product development is enhancing performance of metal oxide blocks, e.g. developing greater energy absorption capability in an existing volume of metal oxide varistors. Another goal of product development might consist of better matching arrester function to the special requirements of each application. A logical final step might even be transfering the voltage limiting property of the arrester to equipment itself. For example, rather than being located outside, the varistor elements could somehow be placed inside the transformer or within its internal insulation to allow for discharge in case of overvoltage. In this manner, the insulation itself would take on voltage limiting properties. But there would be a need to solve certain technical issues such as how the excess energy would be dissipated and new materials would have to be designed to absorb this excess energy.
Looking back on what has been achieved in the area of distribution arresters, silicon carbide gap designs were around for a long time. Given the fact that discovery of the metal oxide technology that ultimately replaced was a serendipitious event, replacing this technology in the future may well require another such ‘accident’.