Dielectric type tests on insulator sets have been performed for decades to ensure satisfactory electrical performance on distribution and transmission lines. Four internationally-recognized and accredited high voltage laboratories, including EGU HV Laboratory in the Czech Republic, the Graz University of Technology in Austria, FGH Engineering + Test/CESI Group in Germany and STRI in Sweden, performed a Round Robin Test (RRT) on a 400 kV double suspension set with polymeric insulators according to procedures outlined in IEC 60383-2 and IEC 60060-1. The insulator set was circulated and participant laboratories performed standard dielectric tests over a one year period. Maximum differences from the measured values obtained by participants were calculated for each test. Such values allow investigating reproducibility of measurements. Furthermore, HV Laboratory No. 1 performed certain tests several times so as to study repeatability of measurements.
There are several methods to statistically calculate repeatability and reproducibility of measurements, including Range & Average Method, Analysis of Variance Method, etc. However, the number of measurements done within the RRT did not allow using those methods. Rather, relative differences and standard deviations of measurements were calculated, allowing repeatability and reproducibility to be assessed for most practical purposes. Results were evaluated according to ISO/IEC 17043, which is a method based on comparing assigned values considered as reference with actual measured values. Since none of the participating laboratories could be considered as reference, assigned reference values were instead calculated as the arithmetic means of the measurements obtained by each.
The main aim of this testing was not only to quantify differences in measurements but also to analyze key factors that can affect measured values. These variables included: test set-up; rain parameters for the test under wet conditions; voltage source parameters; and correction factors. J. Lachman and M. Brosch at EGU HV Laboratory, U. Schichler and W. Lick at Graz University of Technology, W. Schwardt and H. Jahn at FGH Engineering + Test and D. Windmar and B. Engström from STRI discuss these aspects.
Test Set-up
Participating laboratories were asked to follow a standard mounting arrangement, according to IEC 60383-2 cl. 12 (see Fig. 1 to 4). Test set-up parameters were:
• bundle consisting of three sub-conductors (tubes)
• diameter of each sub-conductor: 35 mm – 36 mm
• length of bundle: 8 m
• height of bundle above ground: 7 m
• distance between axis of set and a structure simulating tower body: 6 m
• distance of lower corona rings to rain tower: 7 m
• distance of end terminating corona spheres to HV source: 7 m
Tests Performed
The following dielectric tests according to IEC 60383-2 were performed:
Dry Lightning Impulse Voltage Tests According to IEC 60383-2 cl. 9 (Dry LI)
Standard 1.2/50 μs lightning impulses of both polarities were used according to IEC 60060-1 cl. 7 and by the ‘up and down method’ with 30 impulses of both polarities. The 10% dry lightning withstand voltage (U10) was calculated from the 50% dry lightning impulse flashover voltage (U50).
Wet Switching Impulse Voltage Tests According to IEC 60383-2 cl.11 (Wet SI)
Standard 250/2500 μs switching impulses were used, according to IEC 60060-1 cl. 8. The insulator set was tested under wet conditions according to IEC 60060-1 cl. 4.4.1. The same procedures above were used to obtain and calculate withstand voltage and flashover voltage values.
Wet Power Frequency Voltage Tests According to IEC 60383-2 cl.10 (Wet AC)
The insulator set was tested under wet conditions according to IEC 60060-1 cl. 4.4.1. The maximum withstand voltage test (i.e. a one minute test) and the flashover voltage tests were performed according to IEC 60060-1 cl. 6.3.1 and cl. 6.3.2. Note: The wet AC test is not a standard type test for external insulation above 300 kV.
Test Results
Test results are summarized in Tables 1 to 3. Intensity of red shading in the grid highlights differences in measured values. All values were corrected to standard reference atmosphere, according to IEC 60060-1 cl. 4.4.2. Participating HV laboratories were randomly assigned numbers. To study repeatability of measurements, Laboratory No. 1 performed dry LI tests and wet SI tests on the same 400 kV double-suspension set repeatedly (marked as 1A, 1B, 1C) on different dates. Two measurements were done in 2015, then a historical result from 2001.
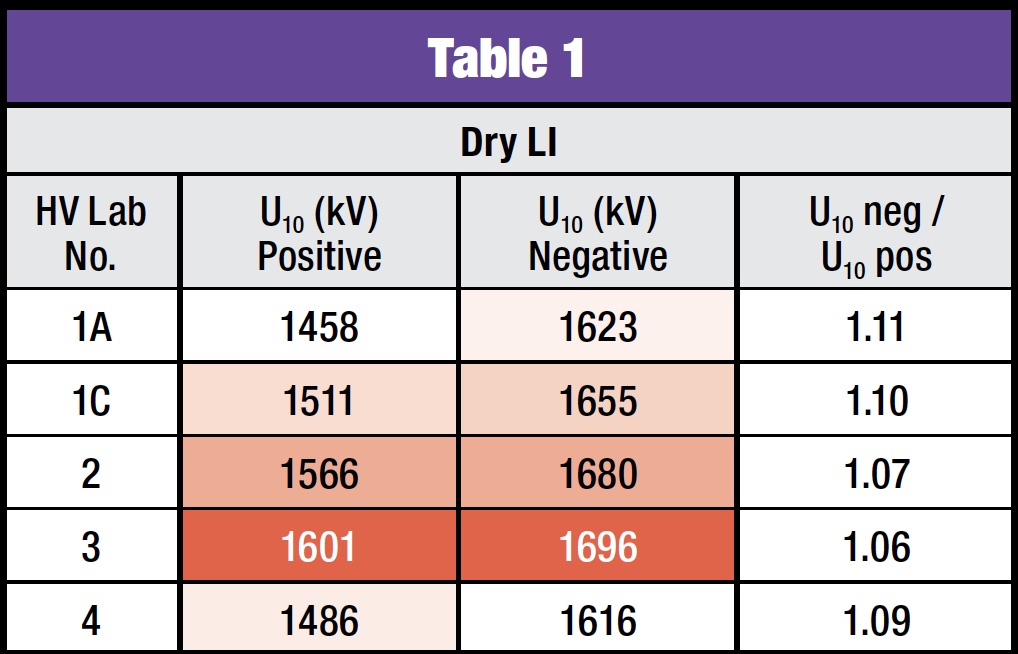
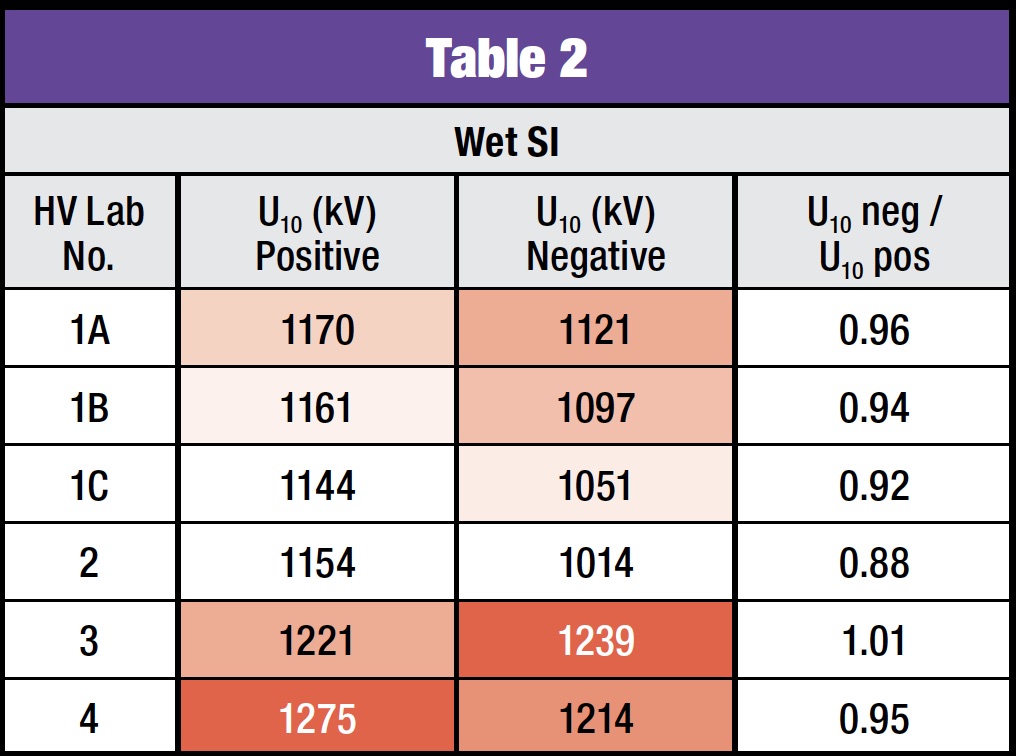
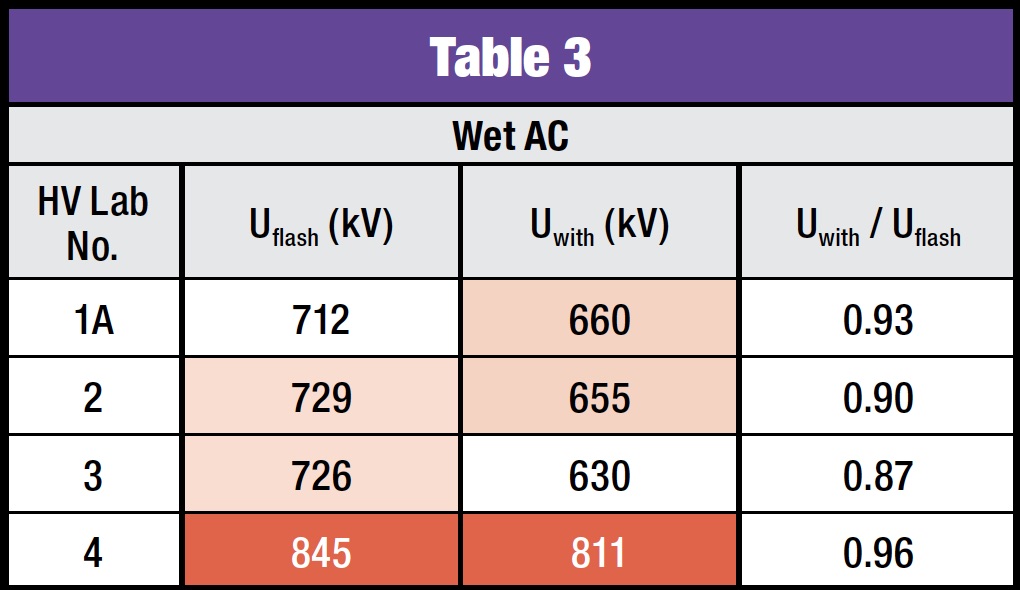
For each test, maximum relative differences were calculated from the highest and the lowest measured voltages measured at all laboratories. Then, standard deviations for each measurement were calculated. These values are summarized in Table 4. Maximum relative differences from measurements done within the same HV laboratory No. 1 are also summarized.
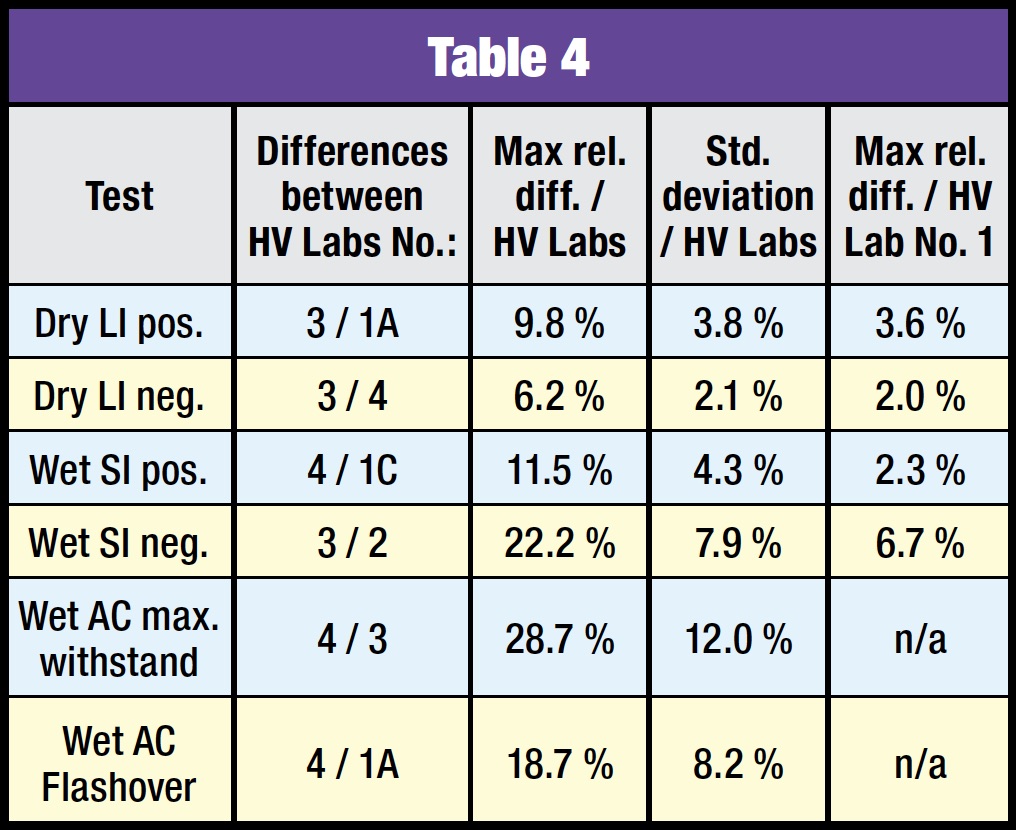
CLICK TO ENLARGE
Maximum relative differences representing reproducibility (between the different HV laboratories) and repeatability (at HV laboratory No. 1) of measurements are shown in Fig. 5.
The greatest differences were indicated in: Wet SI test (negative polarity); Dry LI test (positive polarity) and Wet AC tests, i.e. maximum withstand and flashover voltages. Differences in switching impulse testing under wet conditions done at the same laboratory can be as high as nearly 9%. As seen in Fig. 5, the same trends in maximum difference curves can easily be identified and therefore tests can be considered as representative.
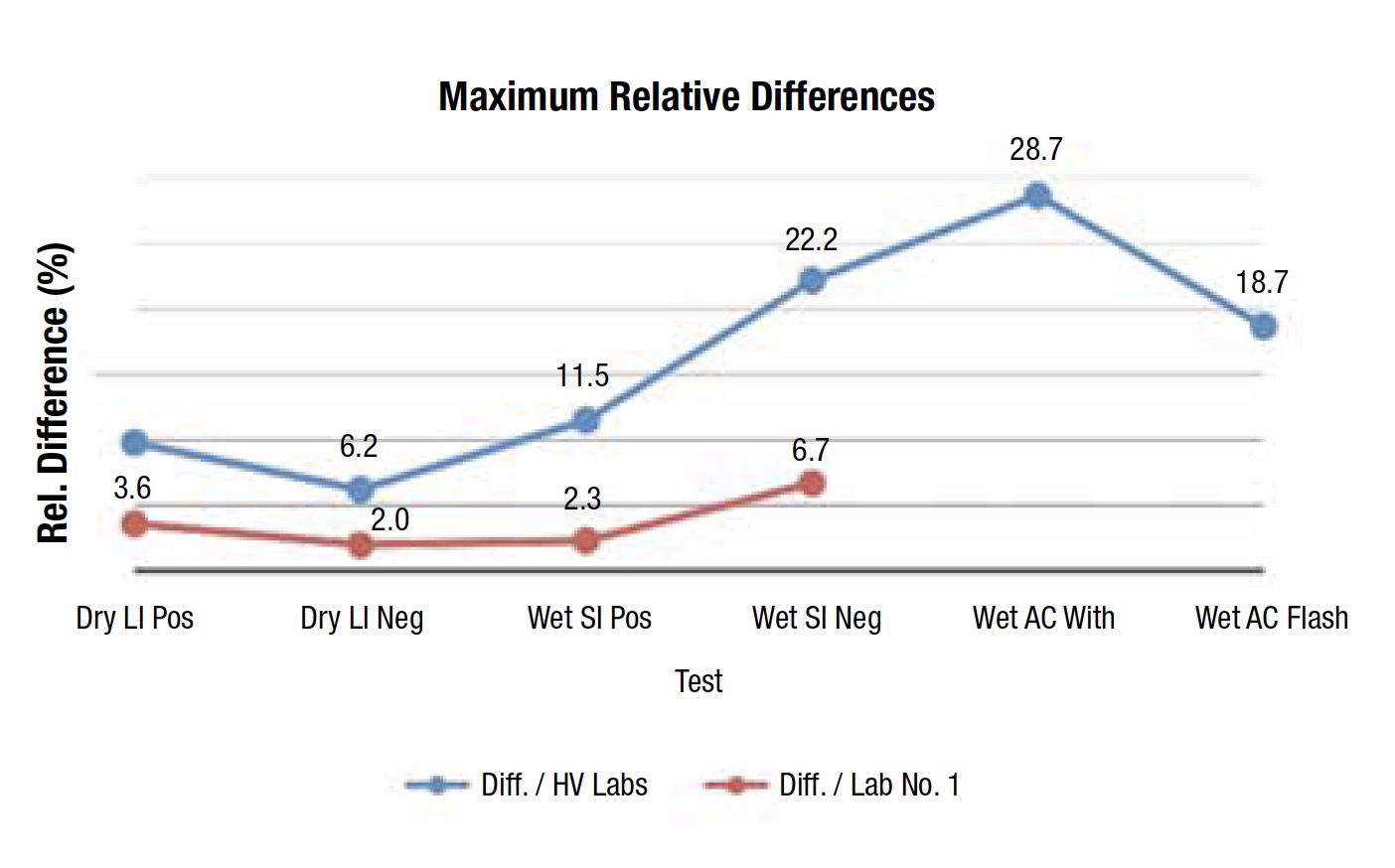
CLICK TO ENLARGE
Evaluation of Test Results
Statistical evaluation of test results was carried out according to ISO/IEC 17043. This method is based on comparing assigned values considered as reference with measured values. Since none of the laboratories could be considered as reference, reference values were calculated instead as arithmetic means from each test done by participants. Such an approach has its limitation in the number of tests done and, in this case, population was not statistically strong. Evaluation of measured values was done from z score calculation:
where x is participant result, X is assigned value, i.e. a mean value, and σ is standard deviation. Standard deviations were calculated from participant results.
Evaluation of z scores:
|z| ≤ 2.0 indicates satisfactory performance
2.0 ≤ |z| ≤ 3.0 indicates questionable performance
|z| ≥ 3.0 indicates unsatisfactory performance
One set of measurements showing highest deviations in measured values (done in HV laboratory No. 1 at the same date in 2015) was chosen to eliminate influence of repeated measurements on z score calculation. Other variations in z score calculation are also possible. Calculated z score values are shown in Fig. 6.
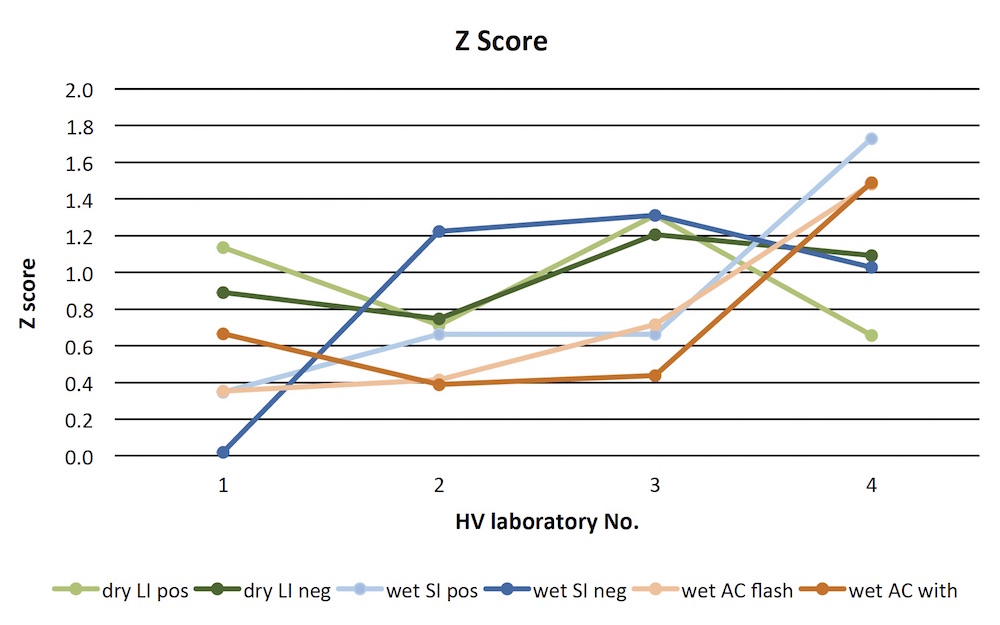
CLICK TO ENLARGE
HV laboratory No. 3 showed the highest deviations in dry LI test results. In regard to the wet SI testing, the highest deviation was indicated at HV laboratory No. 4 (positive polarity). The highest deviations in the wet AC testing are indicated in tests done at HV laboratory No. 4. All results indicate satisfactory performance. In any case, it is important to stress that considering a mean value as an assigned reference value partially eliminates influence of extreme values (as seen in case of wet AC voltages measured by HV laboratory No. 4).
Factors Affecting Measurements
The following factors could affect measured values.
Test Set-up
Participating HV laboratories were asked to arrange a test set-up of the 400 kV double suspension insulator set with polymeric insulators according to IEC 60383-2, cl. 12. The following test set-ups were used:
A) Test Set-up acc. to IEC 60383-2, cl. 12.2
A cross-arm is simulated by a horizontal member, an insulator set being at one end and a vertical member simulating the tower body at the other. In general, that set-up was followed by two of the laboratories. The test set-up shown in Fig. 3 had a vertical member simulated by means of a metallic net. A cross-arm was at more than 7 m from laboratory walls. Then, a triple bundle end terminated with a toroid was at a min 8 m distance from the impulse generator’s shielding electrode. Regarding the test set-up shown in Fig. 2, the closest earthed object to the insulator set was approx. 7 m to 8 m. Distance to the impulse generator was about 5 m to 6 m.
B) Test Set-up acc. to IEC 60383-2, cl. 12.3 and IEC 61284 (Fig. 3)
This mounting arrangement simulates service conditions of a double suspension insulator set. The crossarm is simulated by a horizontal member with the insulator set at the midpoint. A member simulating a tower body is at one end and a wall might be used to simulate an earth plane. That test arrangement simulates a critical variant found in service (see IEC 62184). Test set-ups meeting those requirements are shown in Fig. 1 and Fig. 4. The set-up in Fig. 1 used walls on both sides to simulate tower bodies. Then, a 3 m wire was used to connect an upper yoke to a cross-arm, following clause 12.1 of IEC 60383-1. In that respect, test set-up was different from those at other laboratories where a yoke was connected to a cross-arm by jointing fittings, as per a drawing provided. The set-up shown in Fig. 4 used a tower body simulation on one side. No tower body simulation was on the other but that side is closer to an earthed rain tower at a distance of about 7 m. Then, a triple bundle end terminated with a metallic sphere was 7 m from an impulse generator’s shielding electrode. Height of the bundle above the ground was of 7 m. Acc. to IEC 60383-2, no other objects nearer than 1.5 times the length of the insulator string shall be present in the test area, i.e. 6.6 m in this case. In general, presence of earthed objects in the vicinity of an insulator set can affect dielectric performance since withstand voltages might be reduced. On the other hand, large energized objects such as the shielding rings of impulse generators, dividers, etc. can increase measured voltage values.
Rain Conditions
According to experience at all participating HV laboratories, rain parameters play a key role in reproducibility and repeatability of testing. All participants used the standard method as well as a collection vessel as described in IEC 60060-1, cl. 4.4.1. According to the test reports provided by participating laboratories, rain parameters met the requirements given in IEC 60060-1. For example, measured rain intensities for the wet SI test are summarized in Table 5:
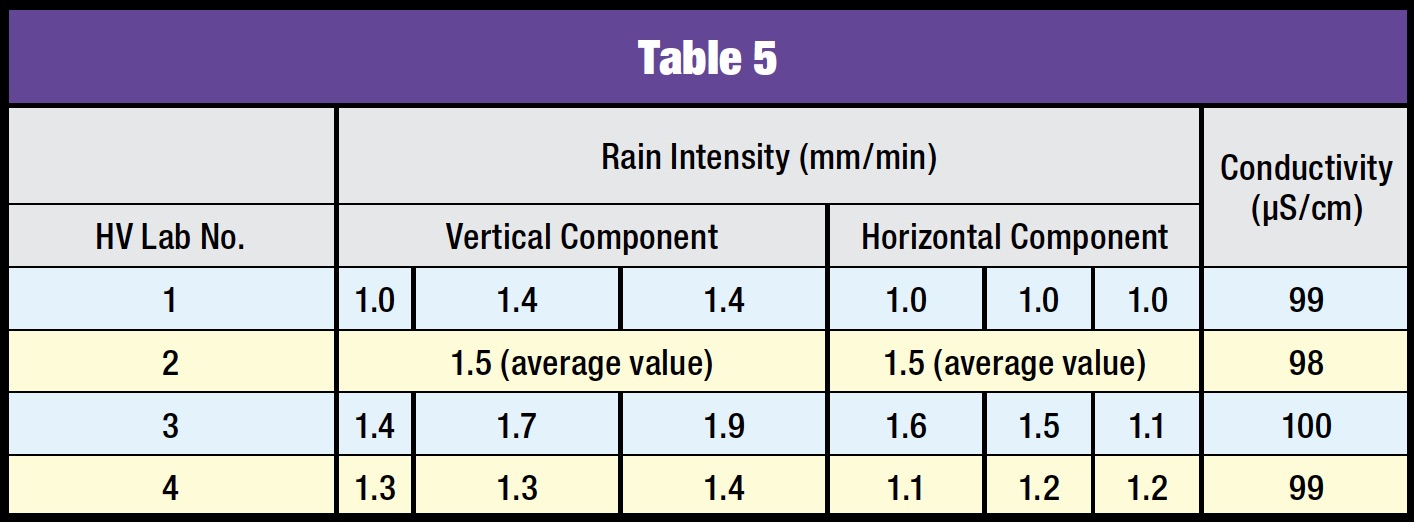
Discussion
• Range of average precipitation rate of 1.0 to 2.0 mm/min is adequate. Note: For longer objects, a vertical component of the rain intensity at a bottom part can easily reach 2.0 mm/min.
• Limits for any individual measurement and for each component of ±0.5 from an average value is quite large. Lower deviations are required to reach more uniform spraying.
• Amount of water measured at a bottom part would depend on nozzle direction and the ability of nozzles to spray horizontally over an insulator, ideally at 90º to the insulator’s vertical axis.
• Direction of water spray to the insulator’s surface is also important if a double insulator set is being tested.
• One laboratory observed that during impulse testing some accumulated droplets were shaken off the test object. When the next impulse was applied, wetting might not yet be fully re-gained and this could affect subsequent impulse performance. Rain intensity at the lower end of the allowable range could also influence this phenomenon. A defined waiting time to sufficiently re-wet the insulator might be useful.
Test Voltage Sources
Parameters of test voltage sources can significantly influence measured values, especially under wet conditions. Requirements for AC voltage sources and test transformers under wet conditions are given in IEC 60060-1, cl. 6.2.2.2, where system current rating of 1 A and system short-circuit impedance < 20 % are required for tests under wet conditions. All participating HV laboratories used voltage sources according to the requirements given in IEC 60060-1. A voltage source with non-adequate short circuit current characteristics would show higher flashover/withstand voltage values. Then, any additional resistors used in a test voltage source circuit to limit short-circuit current should be applied adequately, while respecting minimum short-circuit current requirements. It might be useful to specify minimum short-circuit current characteristic of a full set-up test voltage source. Regarding impulse testing, no requirements for minimum energy of an impulse generator are specified in IEC 60060-1. This might play a role in regard to testing under wet conditions (wet SI test). However, such an influence has not been studied properly.
Atmospheric Conditions
Corrections to standard reference atmosphere were done by each HV laboratory acc. to IEC 60060-1, cl. 4.3 and 4.4. Test results with actual atmospheric conditions and correction factors in regard to dry LI test (as example) are summarized in Table 6.
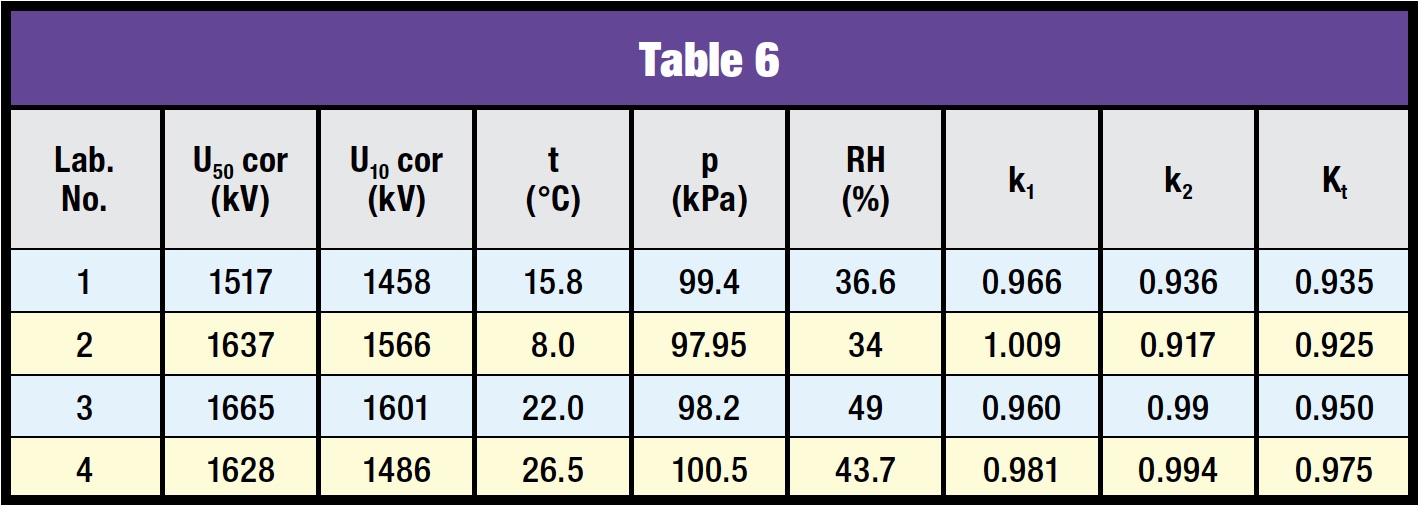
CLICK TO ENLARGE
As seen, tests were done at much different temperatures:
Lab No. 2: t = 8.0°C
Lab No. 4: t = 26.5 – 30.0°C
Humidity values measured by participants did not show such large differences and varied from 34% to 49% in dry tests. Calculated correction factors were in following ranges:
Kt = 0.925 to 0.975 (dry LI)
Kt = 0.957 to 1.008 (wet SI)
Correction factors changed uncorrected measured voltages by up to 8% in regard to dry LI testing, then by up to 4% in regard to wet SI testing and up to 3% in regard to wet AC testing. Calculated correction factors are in the range given by IEC 60060-1 and not considered extreme.
Conclusions
Round Robin Testing on a 400 kV double suspension set with polymeric insulators according to standard procedures given in IEC 60383-2 and IEC 60060-1 was performed at four international high voltage test laboratories. Results were evaluated according to ISO/IEC 17043. Maximum relative differences showed large deviations, especially in tests under wet conditions. These were up to 22% in regard to wet switching impulse tests (wet SI) and nearly 29% in regard to wet power-frequency tests (wet AC). It must be emphasized that measured differences in the wet SI testing are a matter of fact and significantly lower deviations in measured values can hardly be achieved.
Regarding wet AC testing, the highest differences were recorded in measured values at one laboratory. Eliminating those extreme values, differences would drop down to only 7% to 8%. Such a reproducibility level in wet AC testing would be realistic and acceptable. Main aspects affecting measured values were discussed. To reduce differences in reproducibility, it is important to keep variations in any given test set-up to a minimum. Moreover, distances of test object to other earthed and energized objects should be in line with requirements given in IEC 60383-2 and related recommendations. Poor repeatability and reproducibility of dielectric testing might lead to excluding the testing under wet conditions from a standard dielectric type test of insulator sets or other test objects and performing testing only under dry conditions. But that would be an incorrect direction. Estimating external insulation performance from testing under dry conditions would lead to much larger errors. These errors would be due to differences in insulation material and dimensions, profiles etc. since these parameters fundamentally affect external insulation performance under wet service conditions.