While all bushing technologies applied these days are characterized by very high operational reliability, there is now a trend toward greater awareness of their safety aspects. The result has been a greater focus within the industry on advancing dry technology to further improve its service reliability.
This edited contribution to INMR by Laura De Fina and colleagues at GE Grid Solutions in Italy describes research and testing carried out to verify dry RIP bushing reliability as well as to assess various design criteria to assure long service life.
Technologies & Trends
Bushings are devices that enable one or more conductors to pass through an earthed partition, such as a wall or tank, and insulating the conductors from this. In the most common application, the tank is that of HV power transformer. Although not among the costliest of its components, bushings nonetheless have an important influence on a transformer’s service reliability.
The characteristics required of a bushing to perform efficiently in service are:
• good thermal dissipation behavior to avoid overheating and preventing ageing phenomena during normal operation and in situations of overload. In addition, the conductor must have a proper design to also meet the thermal short time current that can be superimposed on continuous operation at rated current;
• reliable internal and external electrical insulation under rated voltage and service overvoltage, under all environmental conditions and especially under pollution;
• adequate mechanical strength, taking into proper account conductor and external connection to short circuit forces, seismic events, wind and ice.
The main bushing technologies in regard to their internal insulation include: oil-impregnated paper (OIP); resin-impregnated paper (RIP); resin-impregnated synthetic (RIS); and SF6. Each offers advantages but also comes with certain disadvantages.
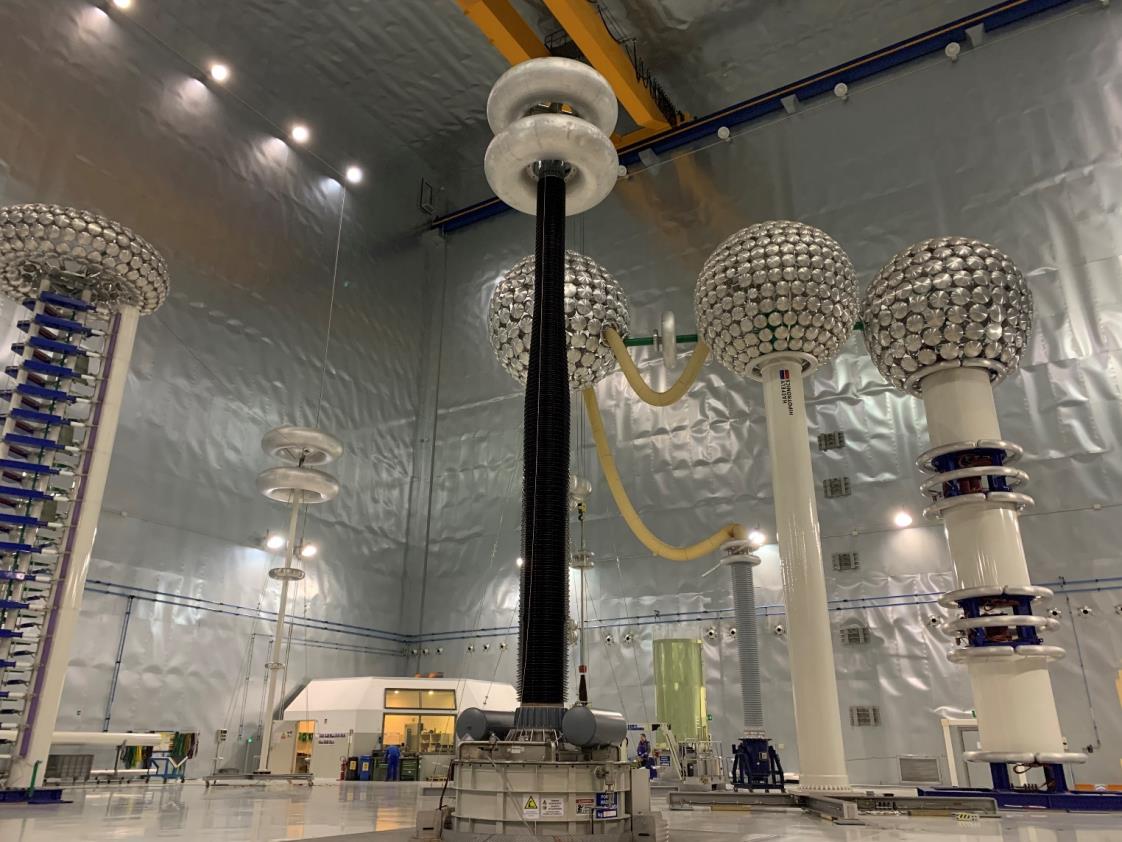
OIP technology, for example, consists of a condenser core wound using kraft paper and subsequently treated and impregnated with oil. This offers very good heat exchange due to the thermal properties of oil as well as the possibility to have oil circulation cool the conductor. Moreover, analysis of dissolved gases is an established diagnostic tool for this technology to allow any necessary preventive maintenance. On the other hand, OIP bushings have an insulation class A up to 105°C, which is lower than that of RIP and RIS bushings.
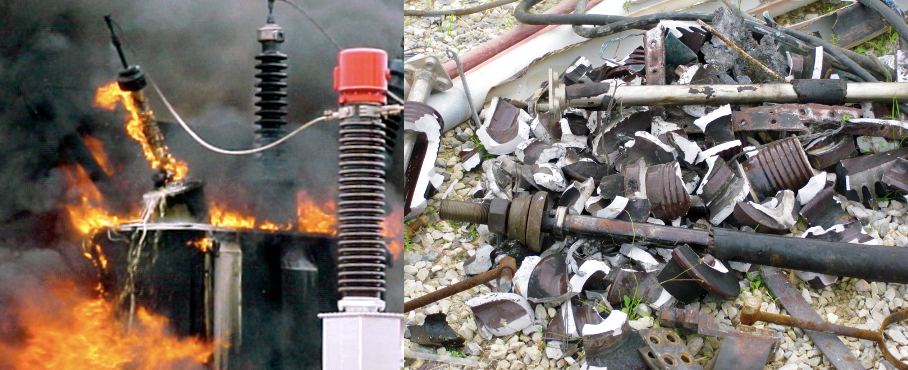
The OIP solution has the longest service experience and is still the most widely used worldwide. Still, its main disadvantage comes from the safety and environmental points of view since, even if rare, there remains a risk of possible leakage and flammability in the event of accidents. Furthermore, since porcelain is still used in most OIP applications, explosion of the housing could occur following an internal fault, with risk that dangerous shards are projected toward people and nearby equipment. This risk is prevented when composite insulators are used as the bushing housing. Indeed, the key motivations behind a transition to silicone composite housings in place of porcelain has been the reduced risk to personnel and other apparatus, better pollution performance and easier handling because of reduced weight.
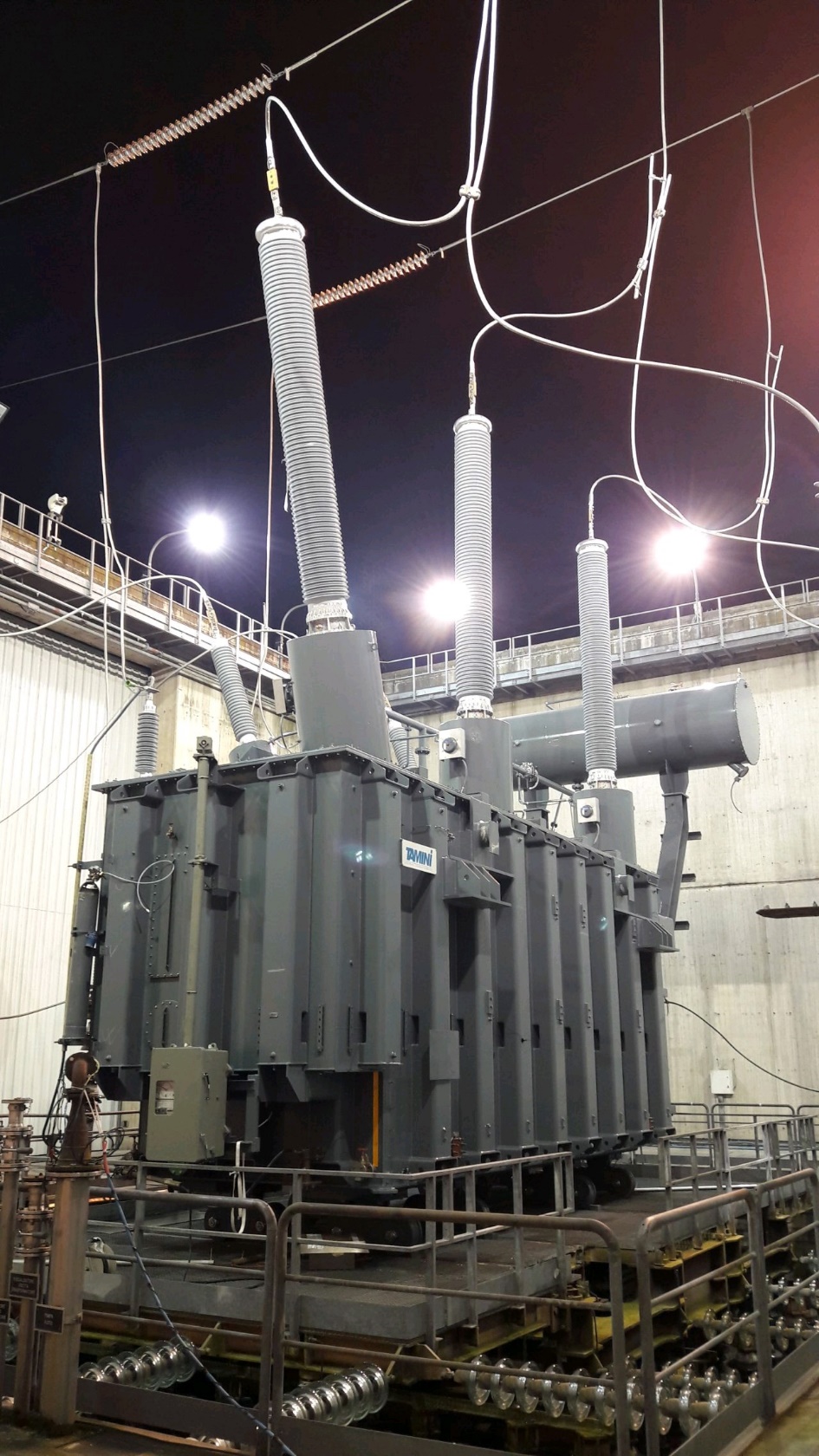
RIP and RIS bushing technologies offer higher mechanical stability compared to OIP bushings. While their heat exchange behavior is less proficient than oil-impregnated paper bushings, this is compensated for by the possibility to operate them at higher temperatures because of their different thermal insulation class E, i.e. up to 120°C. Additional advantages of RIP and RIS are non-flammable materials and lower risk from the explosion point of view, thereby allowing use of either ceramic or composite housings. However, composite housings are now more commonly used because of their hydro-repellent silicone material which allows improved pollution performance.
A disadvantage of RIP & RIS technologies is their presently higher cost. Dry technology is in general more expensive than an OIP solution with the extent of the price increase depending on voltage range.
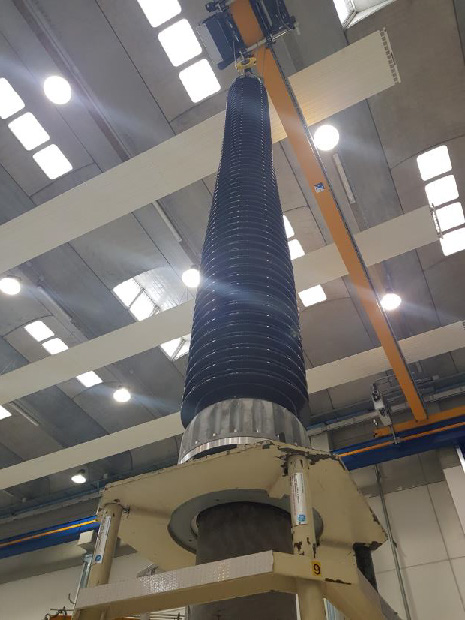
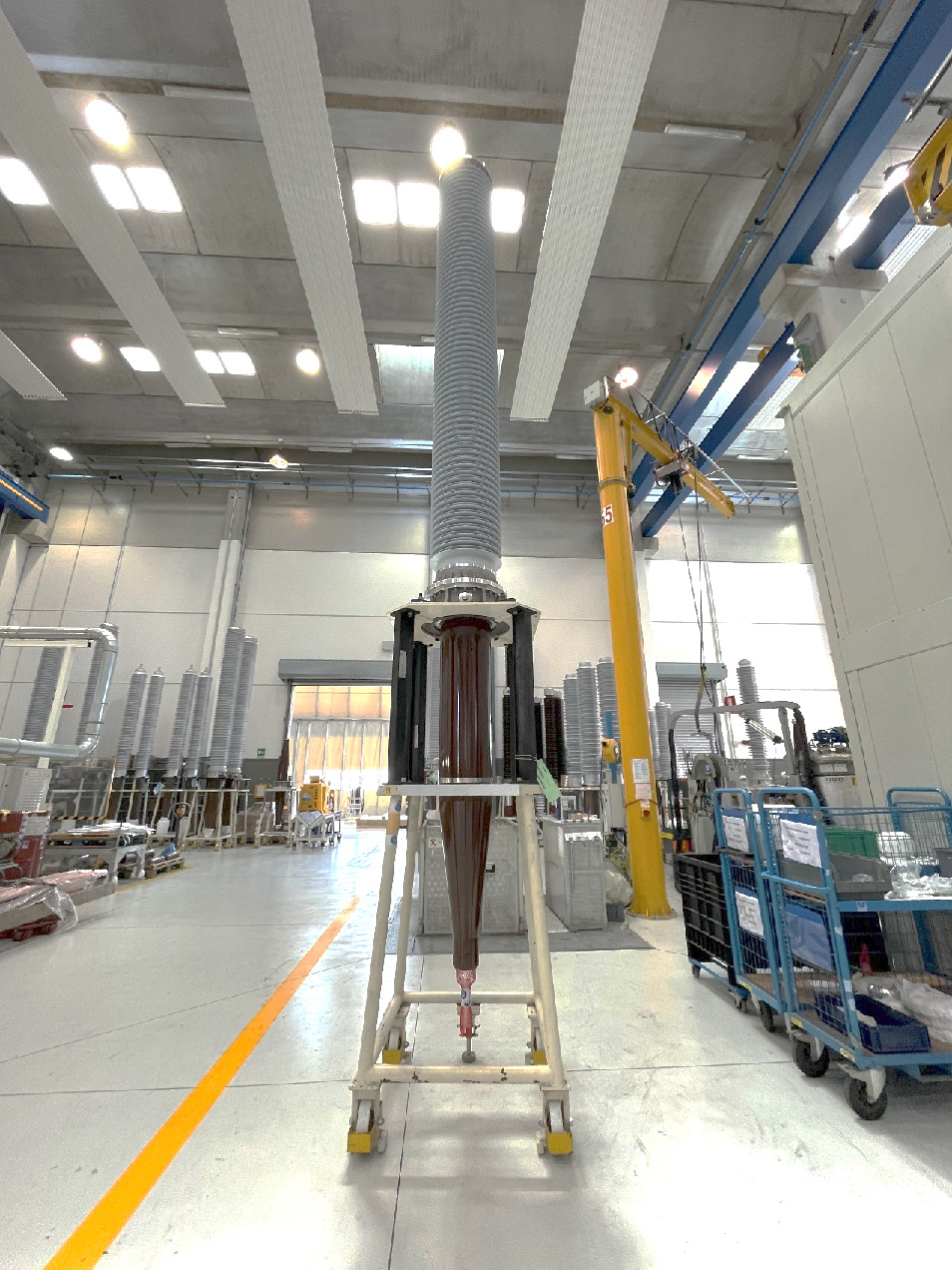
Traditional gas bushing technology uses sulfur hexafluoride as the internal insulation medium and is widely used for bushings installed in GIS, GIL, dead-tank circuit breakers as well as in DC applications for transformers and trough wall-bushings. In converter transformer bushings, the SF6 is used in combination with RIP to provide a reliable hybrid solution up to 530 kV that can also reduce the space required in a valve hall. Application of SF6 technology for wall bushings can used to the highest voltage levels.
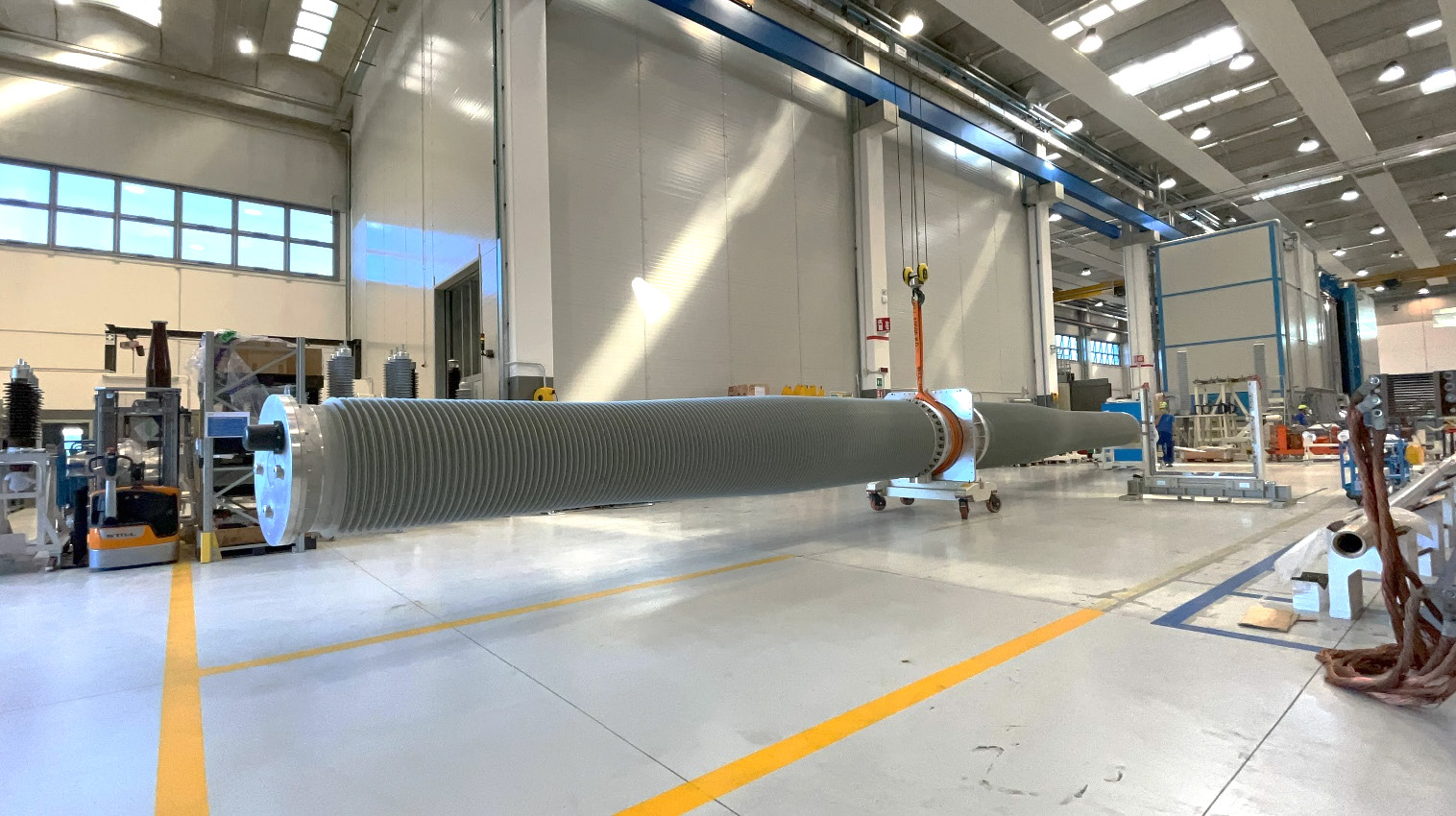
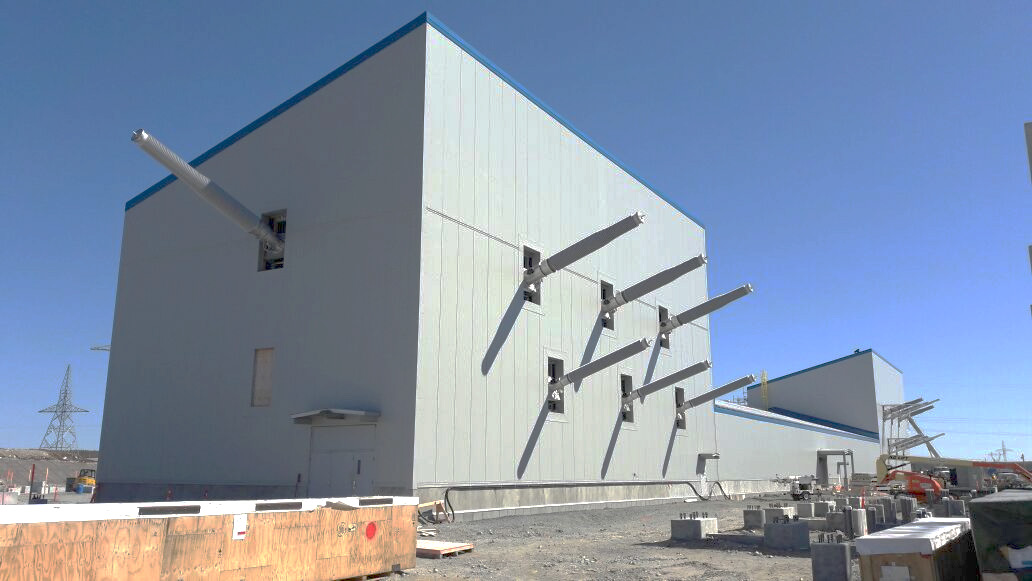
According to recently published market research, the global transformer bushings market is forecast to experience strong growth during the period between 2020 and 2030. Key drivers contributing to the growth will be:
• grid transition and interconnection with renewable energy;
• rapid urbanization activities;
• increasing industrialization in various economies.
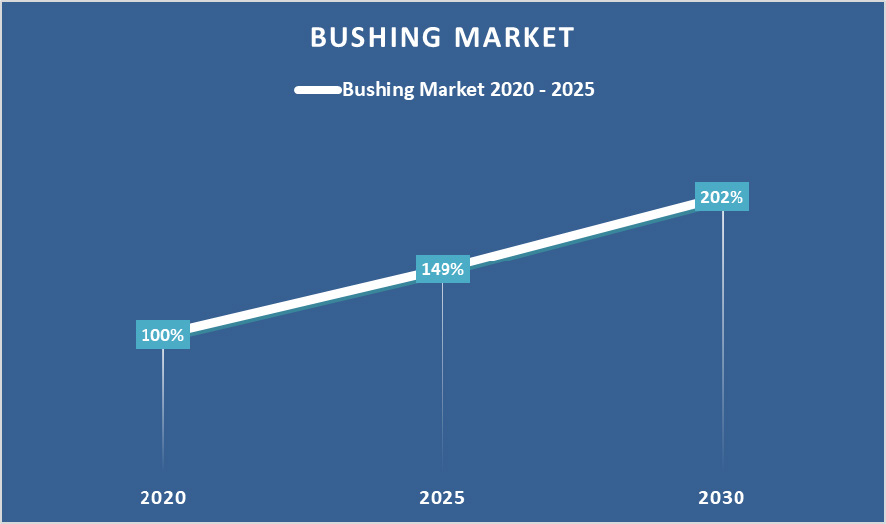
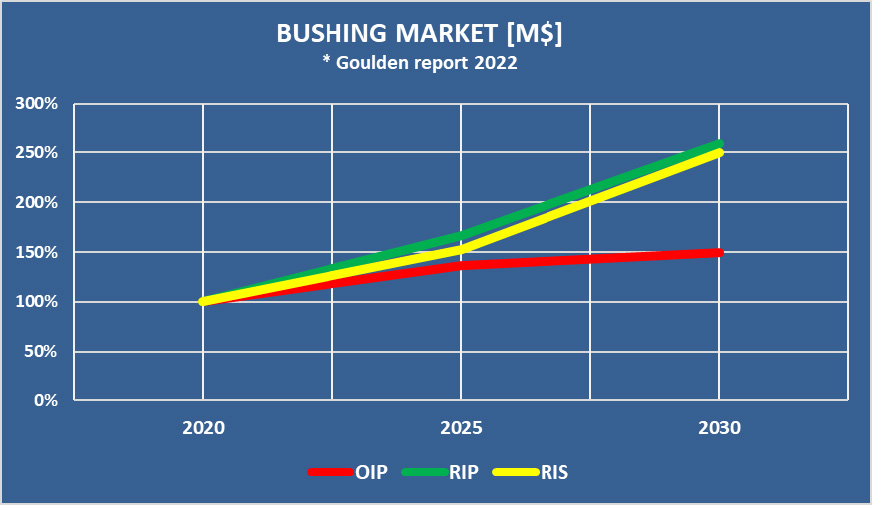
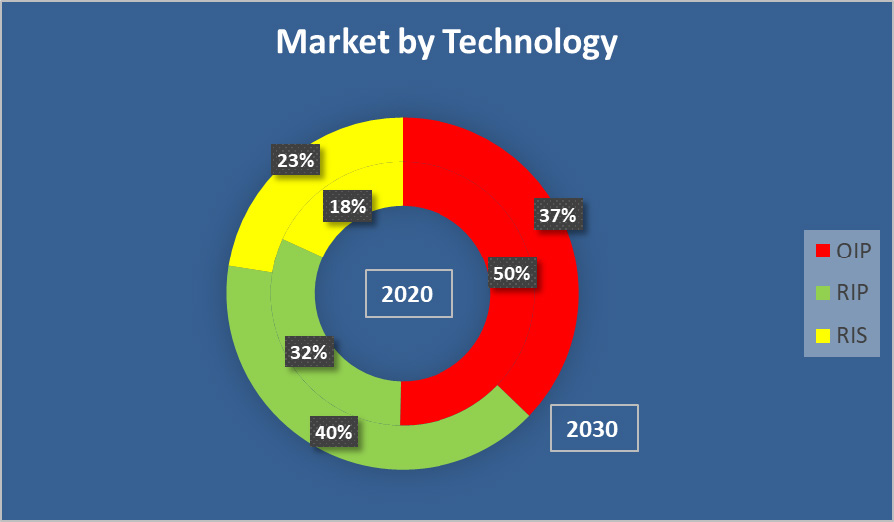
In regard to alternative bushing technologies, the general market trend is shown in Figs. 9 and 10. Estimated growth of RIP and RIS technologies will be higher than for the OIP solution and this will require increasing R&D to assure reliable dry solutions, possibly reducing cost as well.
Bushing Reliability
Bushings are a crucial component for transformers. Although their share of total transformer cost is in the range of 3 to 5%, they are among the most frequent cause of transformer failures. In fact, bushing failure during service could lead to transformer failure. For this reason, bushing test levels prescribed by most relevant standards are higher than for the transformers.
Bushings are designed to support high as well as low temperatures, mechanical static and dynamic loads or some combination of these, overvoltages and harsh service environments with adverse conditions (e.g. heavy contamination). As such, bushings design must consider the following stresses:
• Thermal
• Electrical
• Mechanical
• Chemical & various contaminants
Moreover, these stresses have to be considered non-independent since synergy among them is also a possibility. As such, R&D activities to improve dry bushing design and reliability need to cover the following aspects:
• Internal insulation design;
• External insulation design;
• Mechanical design.
Internal Insulation Design & Tests
Dry type condenser bushings are produced by wrapping paper or synthetic material on a central tube or conductor as thin metal foil electrodes of certain lengths are inserted to grade radial and axial voltage stress not to exceed design limits.
To assess the reliability of the insulation materials subjected to service voltage stress, accelerated ageing tests were performed on RIP specimens under multiple stresses, including thermal and electrical, to represent actual service conditions. One approach to accelerate the ageing process is by increasing the frequency of the applied voltage. Similarly, ageing of RIP bushings for DC applications was also evaluated through a DC voltage endurance test to assess reliability.
Accelerated ageing tests were conducted on RIP insulation materials to verify reliability by applying increased stresses for sufficient time duration to represent the stress experienced by a bushing over its typical service life. Samples were exposed to these stresses up to discharge or alternatively for a time duration comparable to required equivalent life. To evaluate behavior of these samples, the following conditions were applied:
• oven with controlled temperature at 90°C
• three different voltage/electrical gradient levels (kV) increased compared with design criteria
a) |E1_test|=140 % |Eradial|max design
b) |E2_test|=175 % |Eradial|max design
c) |E3_test|=230 % |Eradial|max design
The temperature that the insulation could experience in service (as a maximum average) was selected as 90°C. To reduce test time and accelerate the ageing process, frequency of the applied voltage was increased from 50 Hz to 5 kHz. The following relationship was assumed between life at power frequency f, i.e. Lf and the life Lh, at the test frequency, fh:
For the RIP specimens being tested, given a service frequency 50 Hz and test frequency 5000 Hz, time to failure was estimated at 100 times the test time. Aged samples that had not failed were then tested at lightning voltages (1.2/50 s) to determine if there was any decrease in performance following ageing.
In terms of test methodology, the RIP specimens had been manufactured from the same material used in standard production but machined in a shape to have a central uniform stress area. RIP thickness in this uniform stress area was the average thickness between two conductive layers in the bushing’s condenser core. Several finite element analyses were carried out to fine tune both electrode and sample profiles (see Fig. 11).
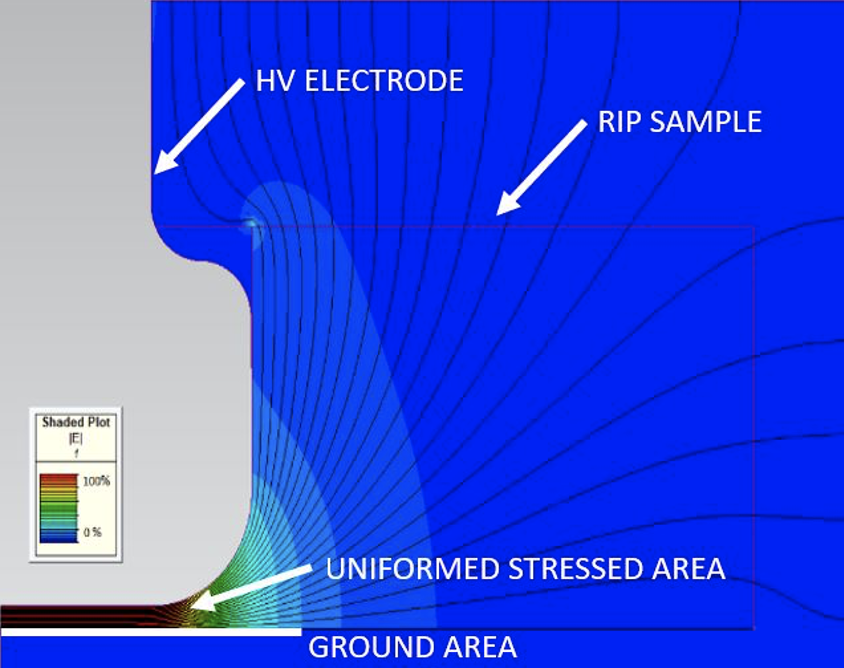
The external surfaces of the uniform stress area were metallized with graphite paint to allow good electrical contact with the HV and ground electrodes with minimum risk of surface discharges. To avoid any other partial discharge activity inside the oven, the HV electrodes were rounded on the air side facing the test specimens (see Figs. 12 & 13).
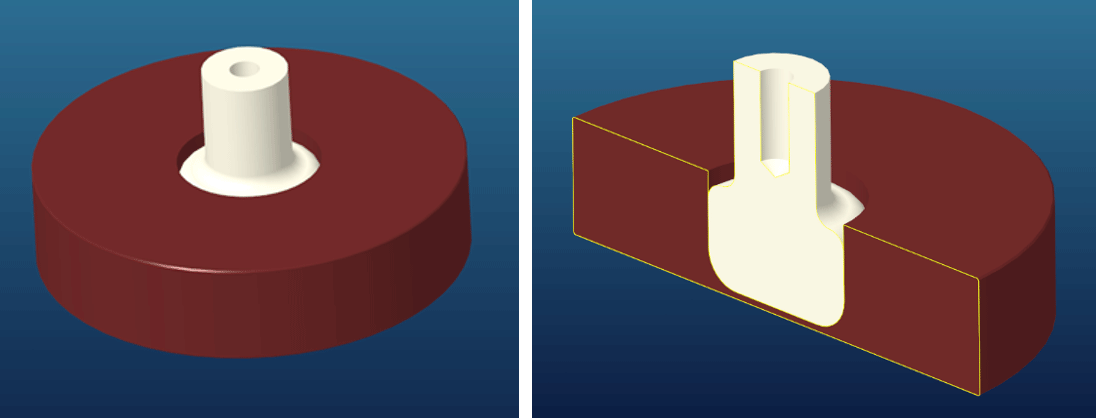
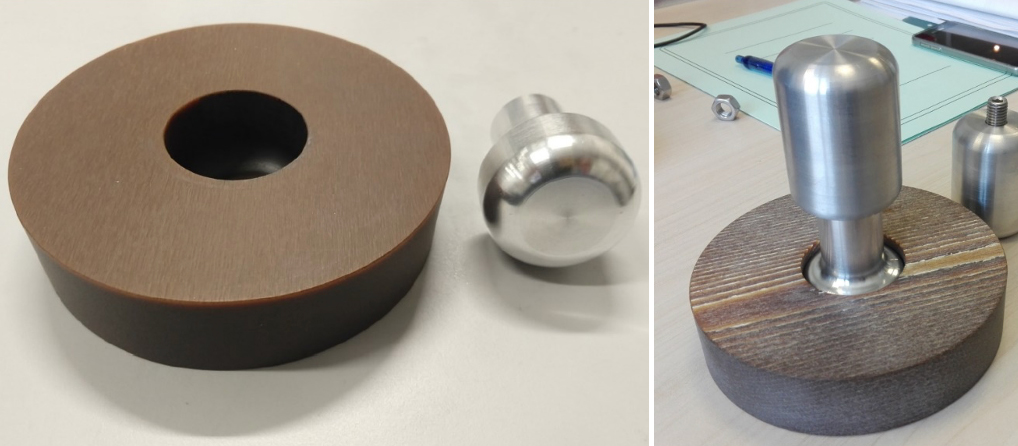
Before performing these tests, the RIP samples were pre-conditioned in an oven under vacuum for 48 hours and then placed inside PET cells and filled with de-gassed silicon oil to prevent external flashover in the surrounding medium.
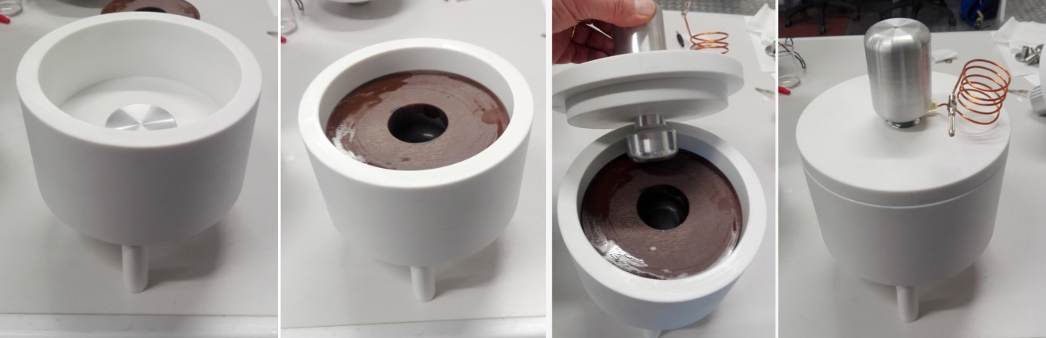
A distribution line was built to supply test voltage for up to 5 specimens in parallel inside the oven through a PET ‘bushing’ with air shields on both sides – inside the oven and outside (see Fig. 5). A set of wires had been put in place to connect the bushing terminals to the specimens’ air side electrodes. Oven temperature was set at 90°C during the entire test while voltage and frequency on the test specimens was constantly monitored. Moreover, a system for measuring partial discharge was used to record, in advance, any signs of insulation ageing. The measuring system was connected to the ground electrodes of the specimens and continuously measured and recorded discharges while, at same time, a circuit board recorded voltage measurements.
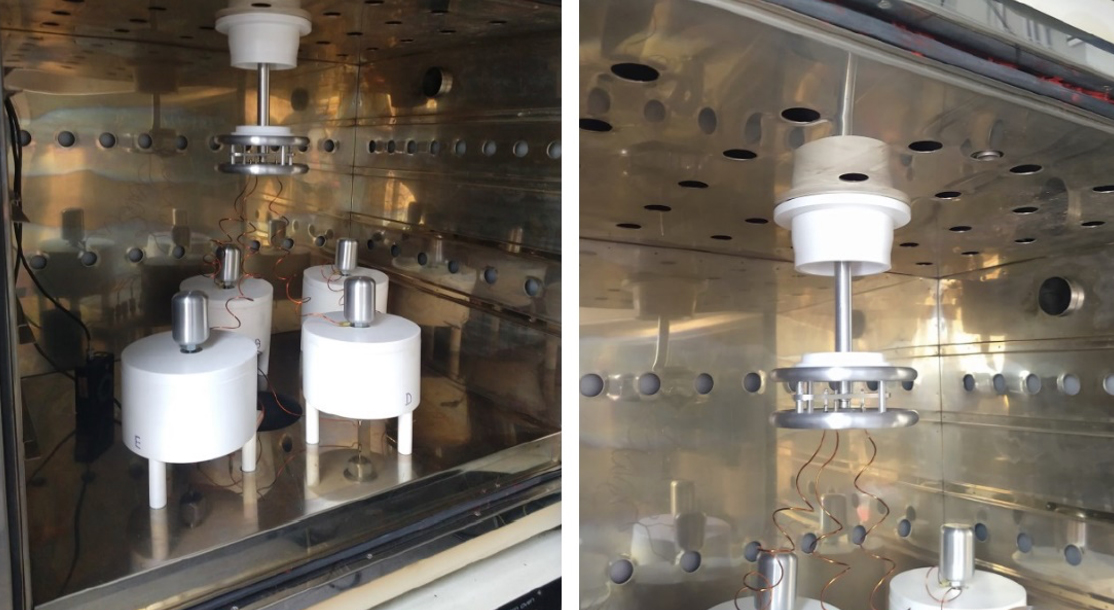
The tests were stopped for all voltage levels at 5000 hours, which corresponded to roughly 57 years of service, according to the above assumptions. No partial discharge activities were measured on specimens without defects.
In regard to the three-voltage levels and samples:
• At |E1_test|=140 % |Eradial|max, two out of the 5 samples failed due to metallization process issues at the initial stage of the test and were therefore not considered.
• At |E2_test|=175 % |Eradial|max, one out of the 5 failed just after energization due to a material defect.
• At |E3_test|=230 % |Eradial|max one out of the 5 failed due to material ageing after an equivalent of more than 36 years’ service.
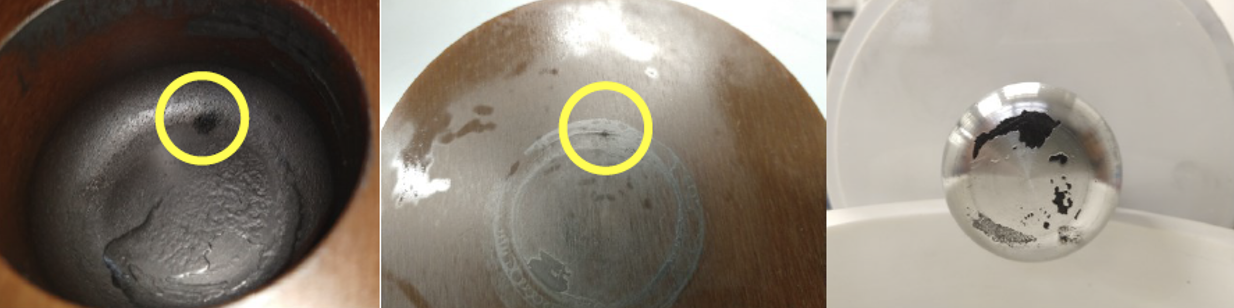
No failures were observed on samples without defects, even with voltage stress up to 175% of normal service stress over an equivalent service life of 57 years. This was much greater than the average required for bushing life expectancy (i.e. 30 to 40 years) and served to confirm the conservativeness of the design criteria.
Lightning breakdown tests were also performed on aged specimens after the accelerated testing. A series of sets of three waves of equal peak voltages were applied, starting from 110 kVpk and increasing by steps of 5 kVpk. The breakdown voltages (BD) show that there was no significant difference among the specimens aged at different stress values (see Fig. 7).
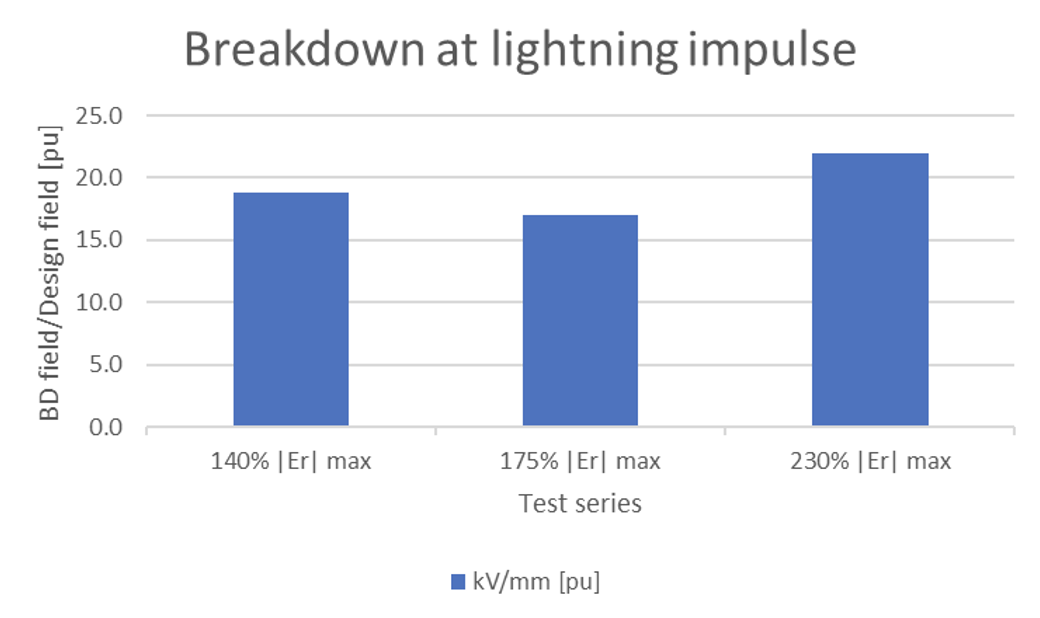
DC Voltage Endurance Testing on RIP Samples
To obtain proper material characterization for DC applications, DC voltage endurance tests were performed on epoxy impregnated paper material at 90°C to represent both electrical and thermal stresses. As used in the AC ageing tests, 90°C was selected as the maximum average temperature that insulation will experience in service. Also, as in the earlier tests described above, test specimens were machined from RIP material in such a shape to have a uniform stress area and to minimize possibility of surface discharges. Sample surfaces in contact with electrodes were metallized to allow good electrical contact between electrodes and sample surfaces.
Test specimens and electrodes were of Bruce profile type, to minimize field increase at their borders. The Bruce profile electrode is composed of three sections: a linear section of radius R0 followed by a sinusoidal section extending over a radial distance of A and terminated by a circular section. This allows for a negligible border effect and nearly constant uniform field region. Effective area of uniform fields can be greater with a Bruce profile compared to other uniform field profiles.
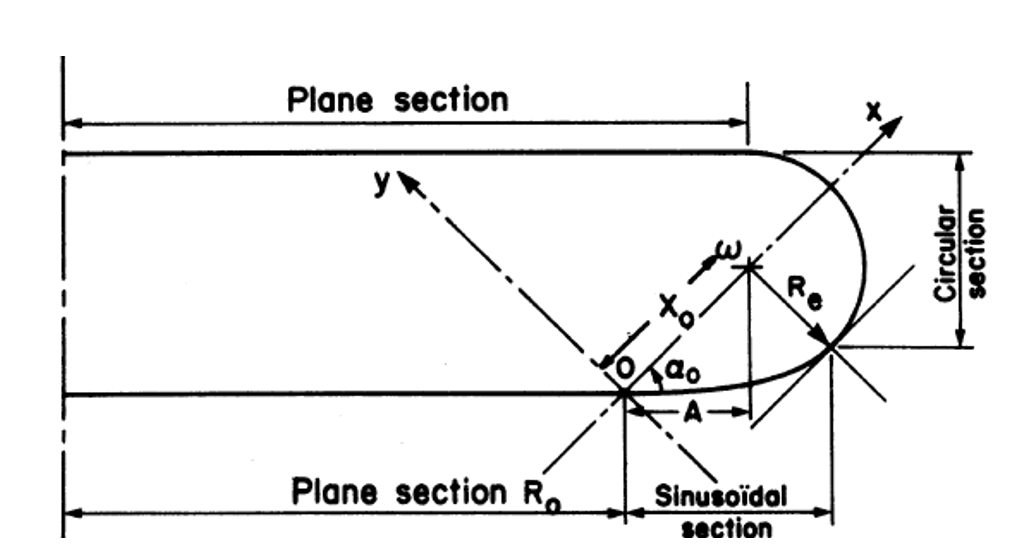
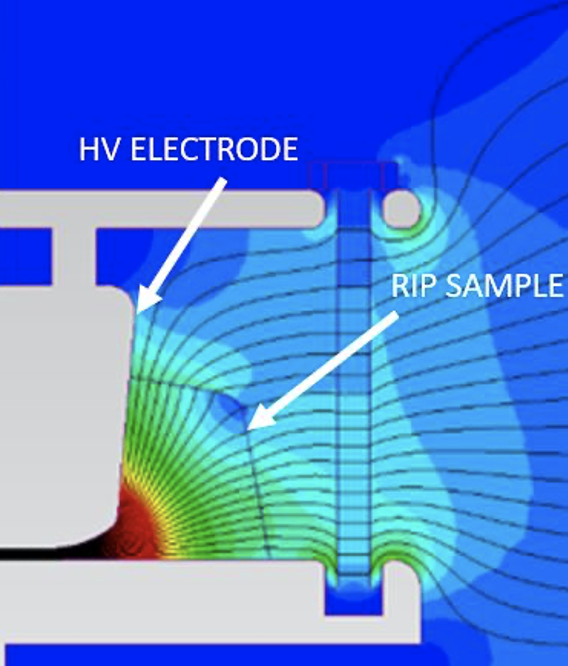
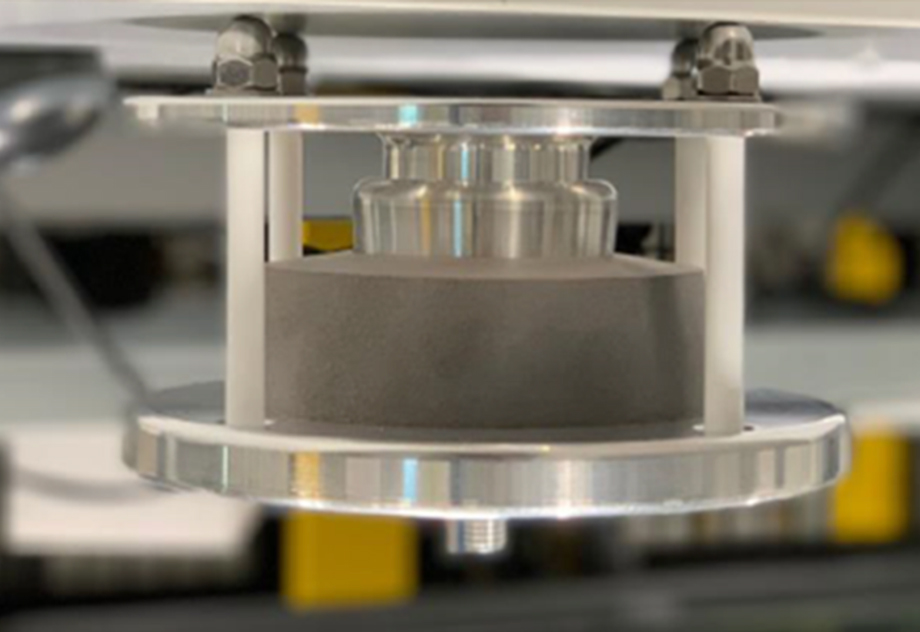
These tests consisted of two parts. In the first, DC breakdown tests were conducted at three different uniform temperatures: 90°C, 70°C and 50°C. As a second step, a set of ageing tests were performed at 90°C and at voltage levels defined as percentages of DC breakdown voltage (as per the first test). During all tests, specimens were kept at constant temperature in a dedicated test vessel, using heating resistors placed on the outer surface that had been calibrated to achieve the desired temperature inside.
Standard IEC 60243-2 was followed for the first test to determine DC breakdown voltage of the samples, using the 60 s step-by-step method. This states that the test shall be applied starting from 40% of probable breakdown voltage and increased by steps, that, for the voltage of the test, have a value of 5 kV. If the test specimen withstands this voltage for 60 s without failure, the voltage shall be increased in incremental steps. Each increased voltage shall be kept for 60 s until failure occurs. The output of the first test is average DC breakdown voltage at 90°C, 70°C and 50°C.
The second part consisted of ageing tests performed at 90°C. Specimens were kept at constant temperature and constant voltage level until breakdown. Voltage levels were defined as 90%, 75% and 65% of the short time DC BD average voltage. The output of these tests was a DC voltage-time (V-t) curve at 90°C (shown in Fig. 21).
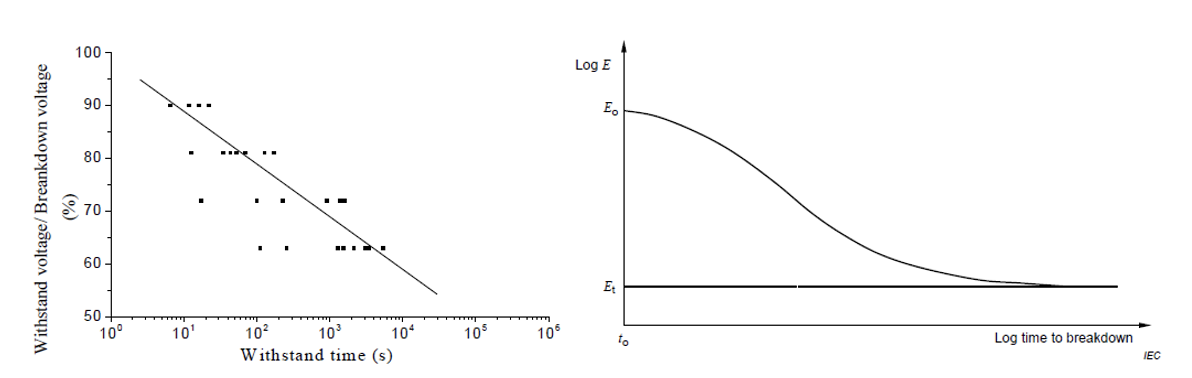
In regard to set-up, dedicated mock-ups for solid material ageing were used to simultaneously test 5 samples in a gas-insulated environment that allows having pressurized gas (SF6, dry air, etc.) with humidity control and constant temperature. The vessel system allowed disconnecting any punctured specimen and continuing testing the remaining specimens.
Concerning methodology, the following procedure was established for these ageing tests:
1. Conditioning the samples at 75°C for 2 days using N2 at 4 bar abs to reduce humidity content within the bulk material and ‘de-sorb’ any moisture;
2. Installing samples in the insulated test vessel;
3. Applying ageing voltage (90% of the short time DC breakdown voltage) up to breakdown;
4. After each breakdown, recording the time and re-applying the voltage to the remaining specimens.
Leakage current on each sample was also measured over the test’s duration to monitor evolution in material conductivity with time and to obtain additional information on possible deterioration.
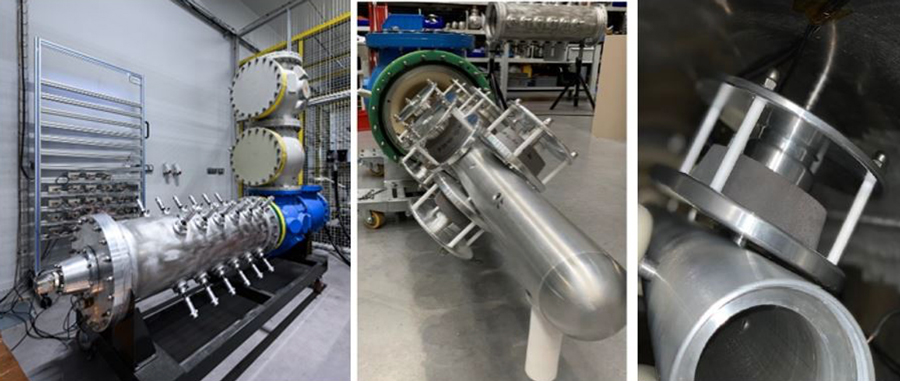
The short time DC breakdown voltage tests were completed and, as expected, voltages at breakdown were lower at higher temperatures. Considering average breakdown stress at 50°C as reference, Fig. 23 shows a plot of average BD fields per unit. Increased temperature almost halved breakdown field.
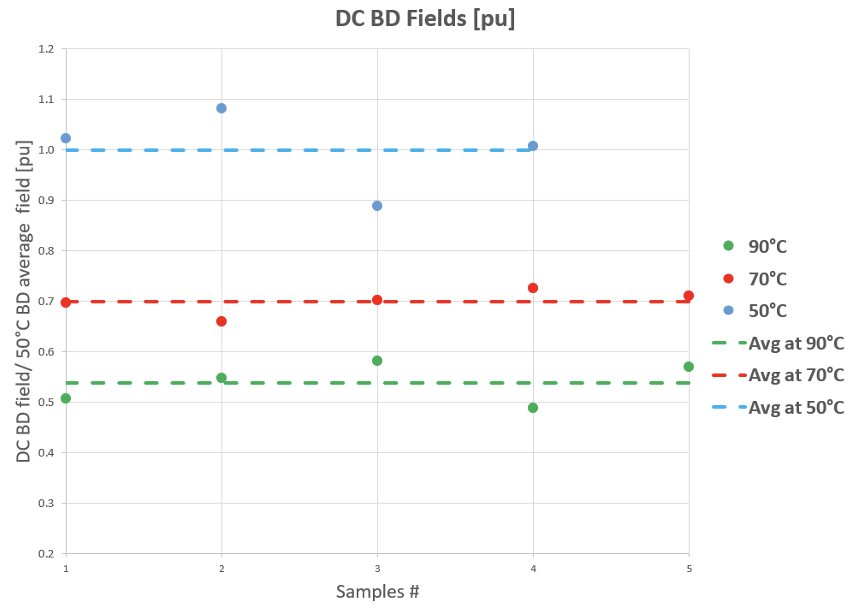
Comparing these results with average design criteria, a safety margin was estimated for each temperature.
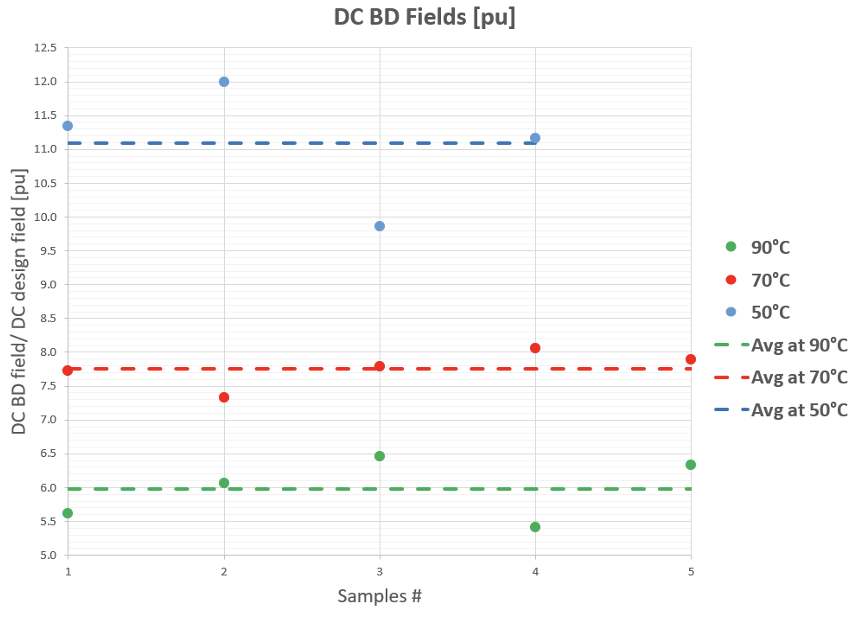
In regard to the ageing tests, Fig. 25 plots time to breakdown of each sample versus the ratio between testing voltage and average breakdown voltage. When comparing the V-t endurance curve at 90°C (based on preliminary results of these tests) with design voltage, it is evident that present criteria guarantee highly reliable service life.
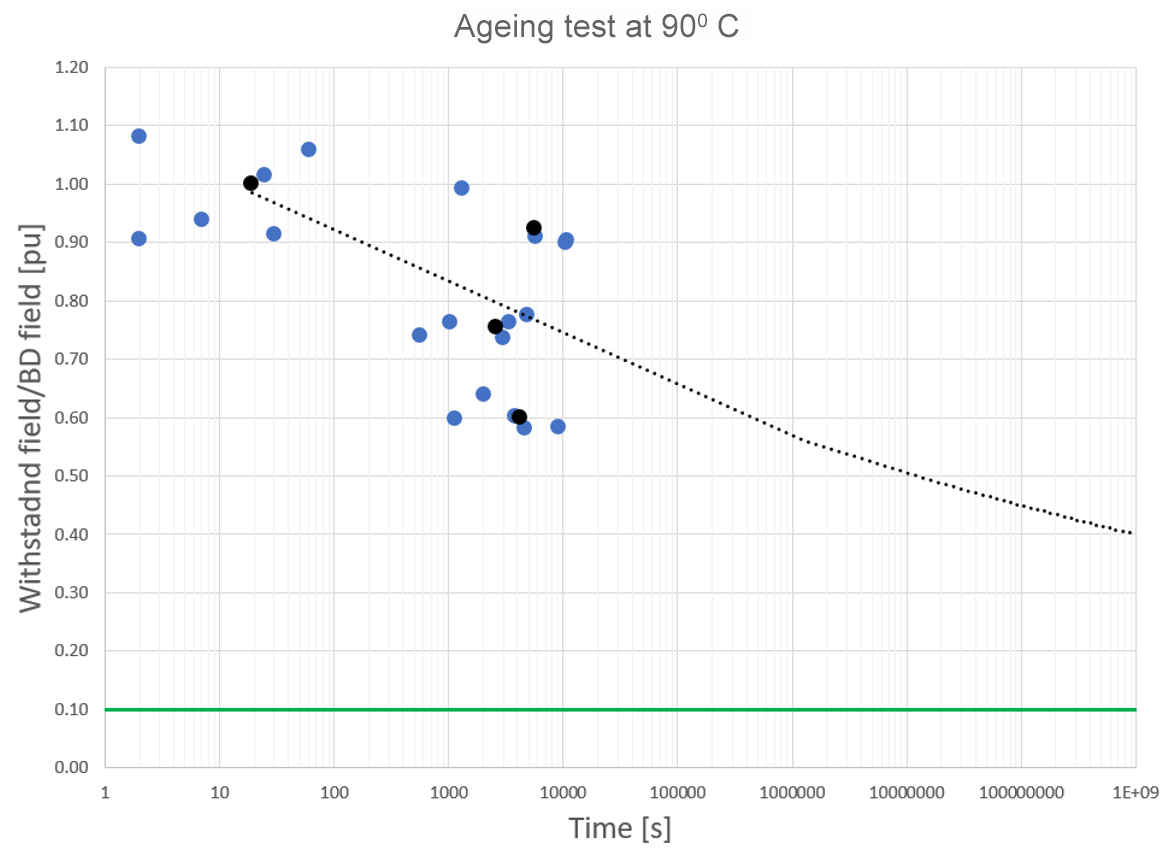
Partial Discharge Performance of RIP Bushings
To advance knowledge on RIP insulation, continuous effort has been devoted to collecting and analysing data and experience with faults by partial discharge measurements done with the conventional method (as per IEC 60270). These records on PD patterns permitted identifying different types of faults that can occur. The literature describes much work devoted to recognizing partial discharge activity but this is mostly general in nature and not really applicable to specific equipment such as a bushing.
Phase resolved partial discharge (PRPD) patterns, which visualize occurrence of PD activity in reference to the phase of AC voltage allows classifying defects. Based on this classification, it becomes easier to recognize them. In a PRPD pattern, important parameters include discharge location in reference to phase angles and also variation in discharge magnitude with voltage and time.
Delamination is a typical defect that can appear in solid insulation. A void, for example, can generate partial discharge activity at the interface between the foils and the RIP materials. Delamination PD patterns are symmetrical with discharge pulses on the positive half-cycle larger than on the negative half-cycle. Other PD patterns based on experience are listed in Table 1 and refer to contamination on insulator surfaces and discharges in air from a sharp point at ground potential. Such continuous research has offered useful support to analyze bushing defects and has also provided valuable feedback about process reliability and recognizing systematic process deviation.
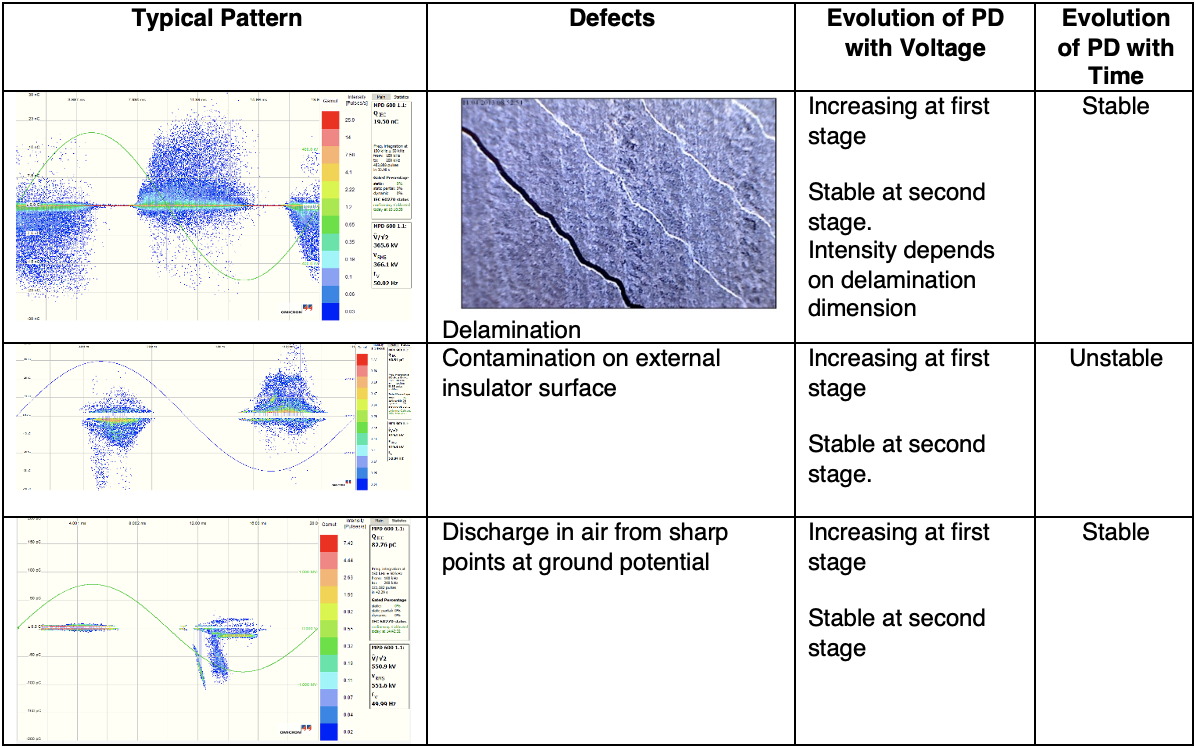
Special Tests on Dry Type Bushings
Beyond the above tests on materials, extended DC special tests were also performed on dry type bushings to assess service reliability, considering the polarization effect. The example shown in Fig. 16 involved a DC RIP bushing, rated Um at 530 kV and foreseen to be applied for a service voltage of 400 kV. It was successfully subjected to a 12-hour test at 690 kV, which corresponded to 30% more than rated voltage. The bushing was placed inside a turret that houses a barriers system to represent its actual service condition in an HVDC converter transformer. The bushing was tested with continuous PD measurements to detect any abnormal behaviour. After completing the DC extended test, success was confirmed based on the type tests as well as with AC partial discharge tests performed both before and after the long duration test and which showed no change in main parameters.
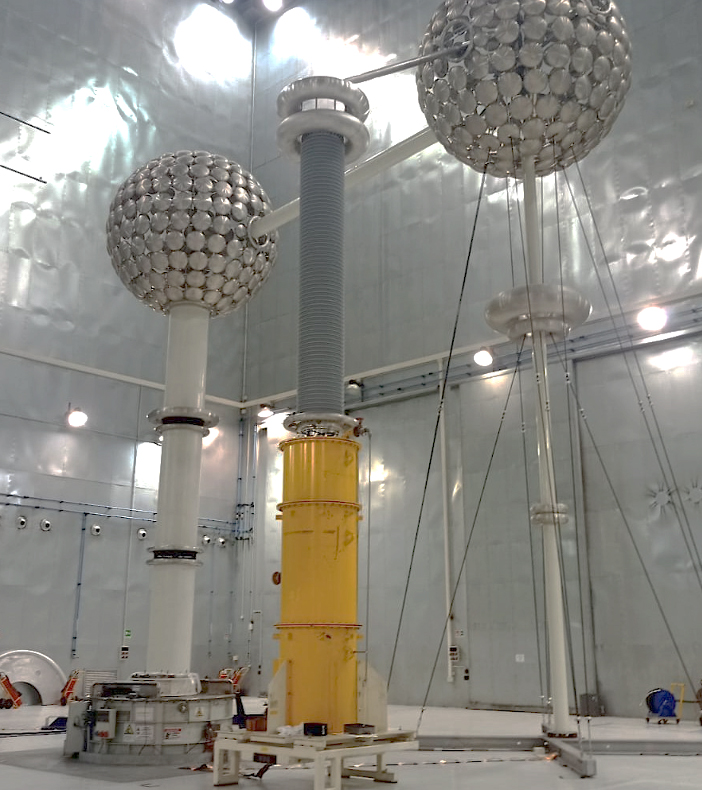
Mechanical Design & Testing
The main aim of mechanical design for a bushing is to ensure the best service conditions for materials by predicting stress and strain during its life cycle. Proper design must therefore evaluate stress under both test and service conditions. In this regard, the main loads generally come from the external connections that are subject to bending, gravity (due to mounting angle), earthquakes and short circuit forces. As a first step, advanced numerical analysis is useful to schematize the physical model using different failure criteria and mechanical properties as input for the different materials. The main components of a bushing can then be verified for different loads, acting simultaneously, to simulate test and service conditions. This helps designers to ensure the correct criteria are adopted. Fig. 17, for example, shows the ratio between predicted stress of a 550 kV RIP design subjected to seismic test on a shake table and maximum allowable stress according to design rules and material tests.
To achieve final product qualification, mechanical type tests are necessary to evaluate bushing performance. The tests recommended in most relevant standards are seismic (for bushings installed in areas where earthquakes occur) and cantilever (to simulate stress on the connection and on a bushing’s structure during service). Since utilities often require type test certificates not older than 5 to 7 years, continuous upgrade in product qualification is necessary to sustain any manufacturer’s product portfolio.
Focusing on the seismic aspects of dry bushing technology, laboratory tests were carried out using a shake table to validate RIP bushing classes 245 kV, 362 kV and 550 kV equipped with hollow core composite insulators. In general, seismic stress has a specific spectrum of frequencies from 1 to 30 Hz. Maximum peak in frequencies is from 2 to 10 Hz while for other frequencies stress is lower. The critical point in seismic bushing design is the resonance frequencies that can occur within this spectrum, usually in the lower range for HV bushings and at the higher range for LV bushings. To mitigate seismic impact during the design stage, numerical analyses are useful to evaluate any reinforcement that might be needed to a bushing’s structure or any change in material thickness that can modify its natural frequencies. While it is relatively easy to modify the vibration mode for a low voltage bushing, this can be complex and costly for a high voltage bushing. A test using a shake table is therefore useful to assess the response of different materials subjected at the same time to mechanical stress relative to their design limits.
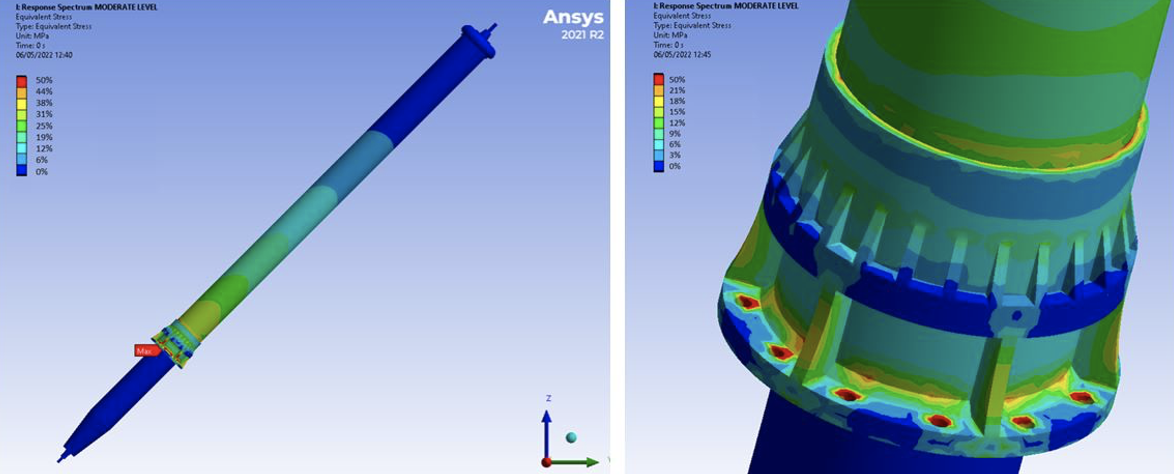
Insofar as test set-up, bushings were positioned on a structure that simulates a transformer turret. Using a specially designed plate, the bushings being tested were installed with a mounting angle of 45°, which is generally the maximum required in service for Um ≥ 245kV. Referring to the reference system according to the IEEE standard, the spectrum in Fig 31 was applied for 245 kV and 362 kV class bushings and the spectrum in Fig. 32 was applied for the high voltage class, i.e. 550 kV. The spectrums were applied along X and Y axes with a damping factor of 2% while along the vertical Z axis the spectrum was applied at 80%.
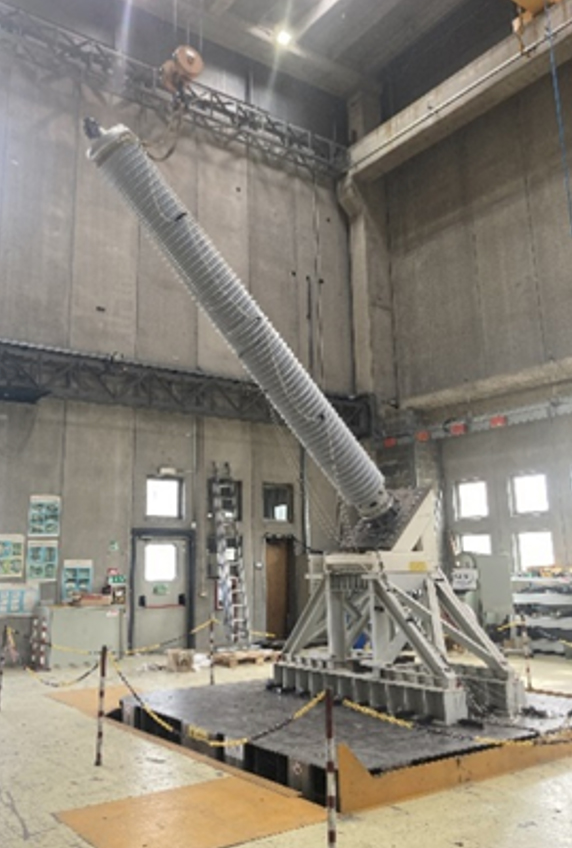
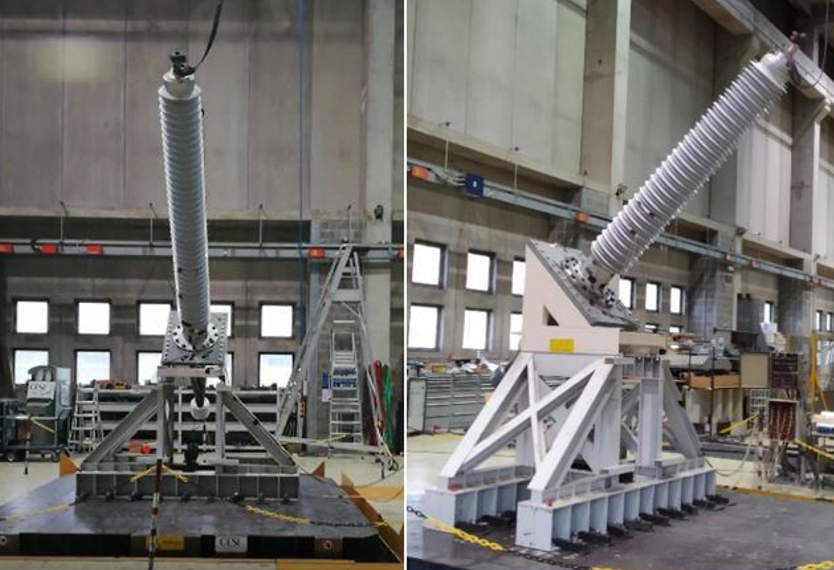
An additional mass of either 7 kg or 11 kg was positioned on the top terminal, depending on bushing size in terms of rated voltage. According to IEEE’s standard, 7 kg is required to be added for bushing in the range 145 kV ≤ Um ≤ 500 kV and 11 kg is added for Um > 500 kV. By contrast, the IEC standard requires 7 kg for Um < 420 kV and 11 kg for Um ≥ 420 kV. With the aim of testing under the more restrictive conditions, the IEC standard was considered as the reference when it came to additional mass. Before performing this test, each bushing was subjected to a routine test in a UHV test hall. The test objects were also equipped with strain gauges placed near the bottom of their hollow core composite insulators, where highest stress and strain are normally expected. To apply the transducers, four 20 x 30 mm openings were made by cutting the silicone sheds all the way to the surface of the fiberglass inner tube (see Fig. 30).
In addition, four accelerometers were placed as follows:
• A0 on the base, at ground level – reference position placed on shake table;
• A1 on the terminal at the top of the bushing;
• A2 near the center of gravity;
• A3 on the shield at the bottom of the bushing;
• A4 on the main flange, on top of the rigid adaptor near the mounting location.
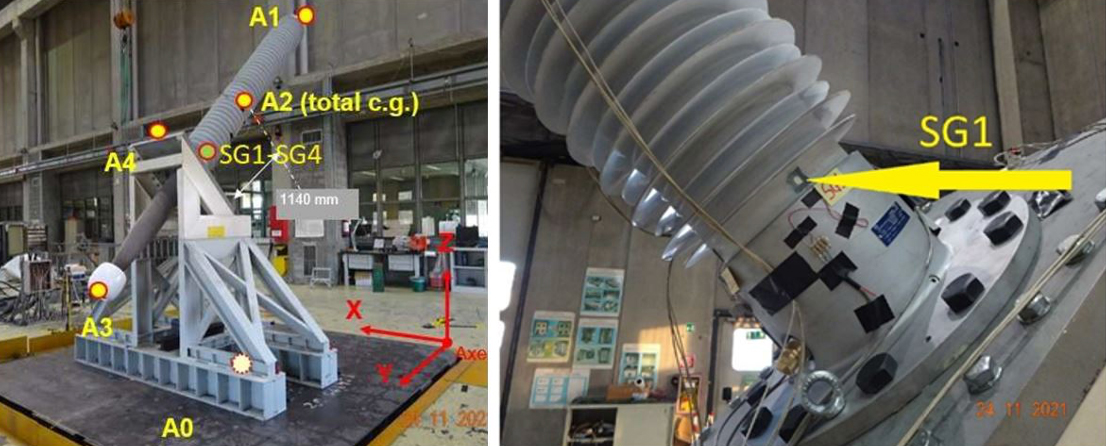
While the bushings were mounted on the shake table according to their class, (as shown in Table 2), pre-seismic static pull tests were carried out by applying a 600N or 1200 N force to the top terminal. This procedure was necessary to calibrate the strain gauges for the test limit based on results of a bending type test previously performed on the hollow composite insulator.
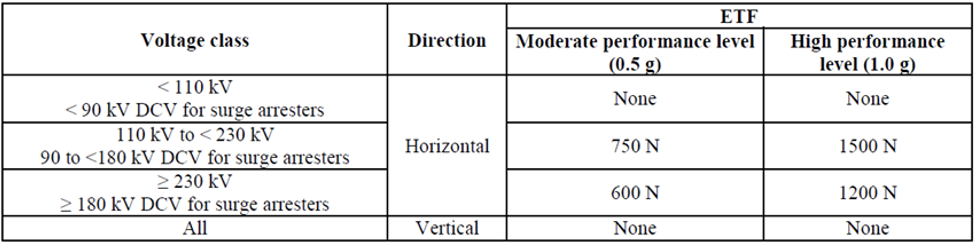
To measure vibration modes, a pre-test was then conducted by imposing an input sine sweep at 0.07g in the main three directions (X, Y, Z) with frequency scanning for resonance research. Such values are useful to validate the input used during any preliminary finite element analysis.
Before starting the final test at 2.00 g for 245 kV and 362 kV bushings, several steps were completed. Triaxial time history shake table tests for calibration and instrumentation checks were performed at 0.08g, 0.12g, 0.18g, 0.24g, 0.36g, 0.50g, 0.70g, 1.00g and 1.42g ZPA. Deformations at each step, measured by the strain gauges, were monitored and these values did not exceed defined limits. Finally, the 2×1.00g =2.00g ZPA time history test was performed according to the demanding requirements of IEEE 693-2018.
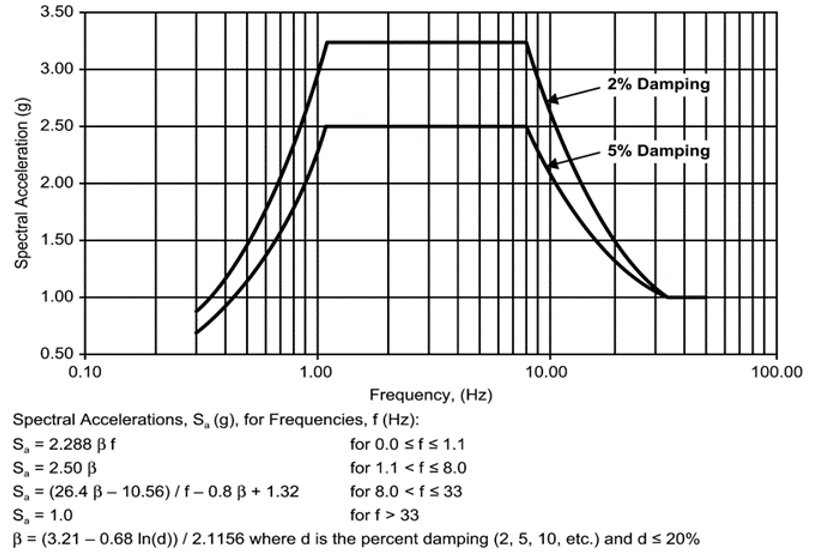
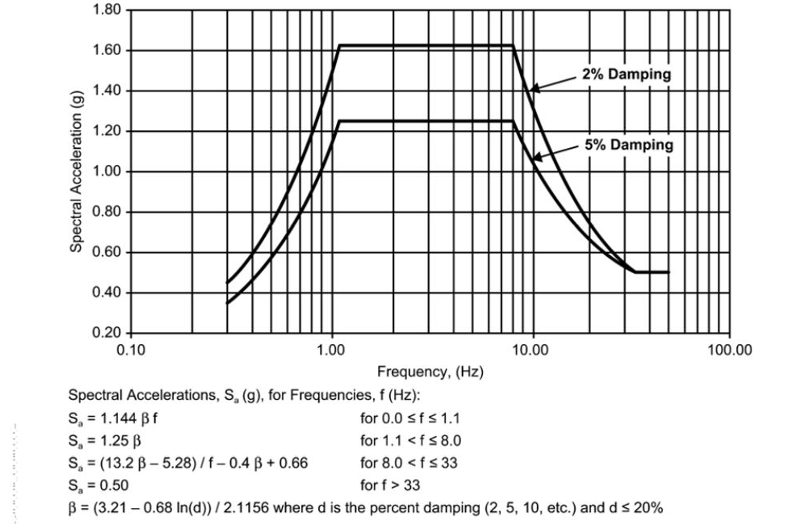
The same procedure for calibration and instrumentation checks was performed at 0.08g, 0.12g, 0.18g, 0.24g, 0.36g, 0.50g and 0.70g for the 550 kV class bushing. After the final test, post-seismic inspection was carried out consisting of the following:
1. Visual inspection for any signs of damage;
2. Comparison of bolt torque values before and after the test;
3. Evaluation of the test response spectra of the shake table motion about its capability to envelop the required response spectra from the technical specification.
Moreover, a post-test resonance search was performed for all bushings by imposing an input sine sweep at 0.07g in the three main directions (X, Y, Z). According to the IEEE standard, a change of more than 20% in the resonant frequencies can be used as the parameter to determine whether there are structural changes because of damage to materials. Resonance tests were successfully carried out for each test object, i.e. with no change in the values before and after testing. After this mechanical test, the bushings passed routine electrical checks with no change in partial discharge behavior. As a point of interest, these tests were witnessed by an independent external group to validate the product with an official qualification report, as mandatory for access to certain end user markets.
Conclusions
Special electrical and mechanical tests were carried out at GE Grid Solutions – RPV Unit in Italy to verify reliability of RIP dry bushings up to 550 kV. Since the market is moving rapidly toward a dry solution to replace traditional OIP technology, their reliability aspects in service are key points that must be included in each product development program from the start. Moreover, dry bushing technology is also growing because of the large demand for HVDC and AC oil-free and SF6-free bushings.
Due to interconnection requirements and network structure, HV substations are sometimes being sited in areas of high seismic activity or with heavy pollution. It has therefore become necessary to offer a fully proven technical solution for such environments and applications. Bushings are an essential component of transformers and their failure for any reason can result in system failure with serious financial consequences for utilities. In this regard, most relevant standards require higher test levels for bushings than for transformers, aiming to obtain reliable products with long service life. In addition to the requirements prescribed by standards, certain special tests performed by bushing OEMs can confirm the service behavior of optimized solutions focused on performance as well as cost reduction.