The 750 kV/±400 kV Qinghai-Tibet Intertie ranked among China’s most ambitious network projects since 2000. Commissioned in late 2011, it connects with 750 kV AC lines running 1500 km between the cities of Xining and Geermu, in central Qinghai Province. From the converter substation in Geermu, it then continues as a ±400 kV DC line to Tibet’s capital, Lhasa, over 1000 km away. Apart from these lines, the project included two 750 kV substations, a 750 kV switching station and the two ±400 kV converter stations. A 220 kV AC circle grid in Tibet was also part of the same scheme, which reportedly involved an investment equivalent to some US$ 2.5 billion.
What made the ±400 kV line portion of the project especially noteworthy was that it was one of the world’s highest overhead transmission lines and also the longest HVDC line ever built at such altitudes. For example, it traverses terrain that averages 4500m, with the highest point reached at the 5300m mountain pass at Tanggula – gateway to Tibet. Apart from the construction challenges across the vast, rugged Qinghai-Tibet plateau under extreme cold, permafrost, high UV and fragile local ecosystems, altitude impacted factors such as corona as well as electromagnetic field. Designing the most suitable line insulators for this environment and meeting performance requirements of external insulation on HV station equipment also proved demanding.
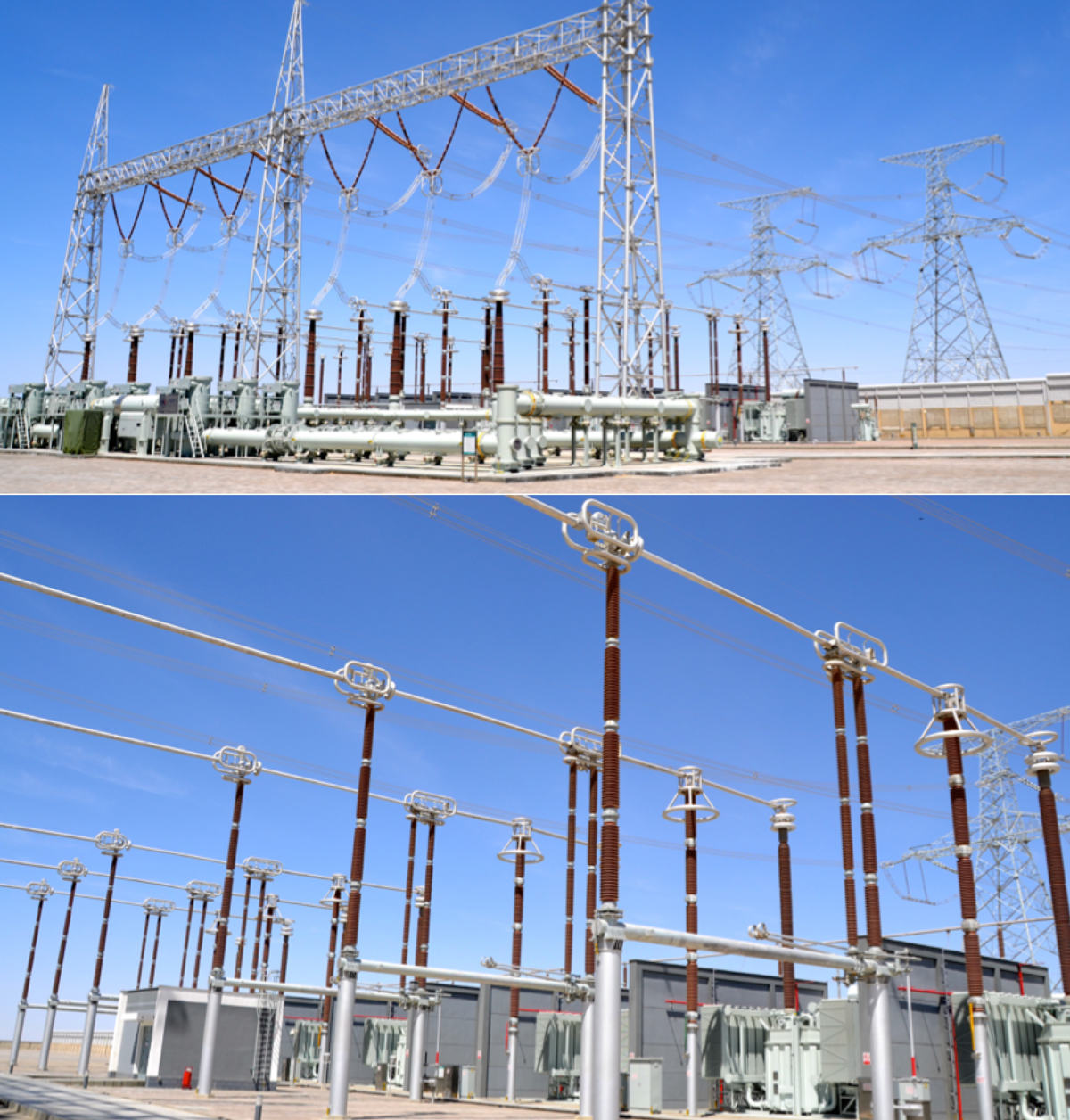
Investments made in expanding China’s power grid over the past quarter century have been extraordinary and best put into context by the fact that between 2005 and 2010, as example, the country added on average the equivalent capacity of the entire power system of the United Kingdom every single year. Notable among these investments were groundbreaking UHV projects – both AC and DC – such as the 640 km 1000 kV AC line between the provinces of Shaanxi and Hubei or the expanded 750 kV AC supergrid in Western China. When it comes to DC, China also completed an array of other major projects such as the 1400 km ±800 kV line between Chuxiong to Suidong Converter Stations in south China.
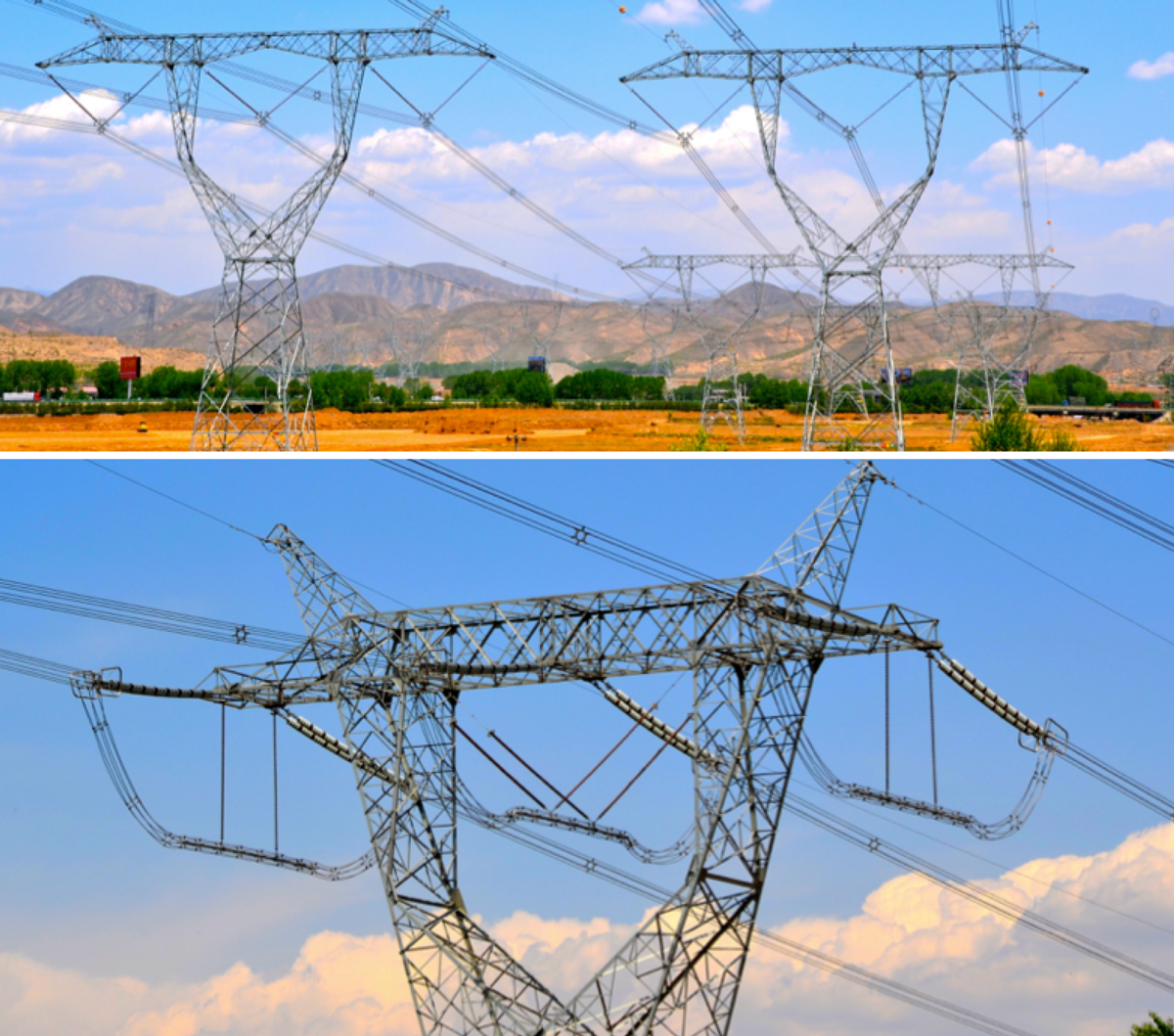
Driving these investments was a commitment by the State Grid Corp. of China (SGCC) to increase electricity transmission as a proportion of total energy delivered. A decade ago, energy sources in China were still transmitted mainly by road and rail with as much as half railway capacity used just to move coal. The SGCC has aimed to increase the share for electrical transmission such that the ratio of coal to energy transmission would drop significantly. Achieving this required construction of numerous new lines and substations. For example, the State Grid Corp and the China Southern Power Grid together planned and realized a dozen UHV DC projects, most at ±800 kV but with one at ±1100 kV, including the Hami–Zhengzhou and Xiluodu–Zhejiang ±800 kV DC projects.
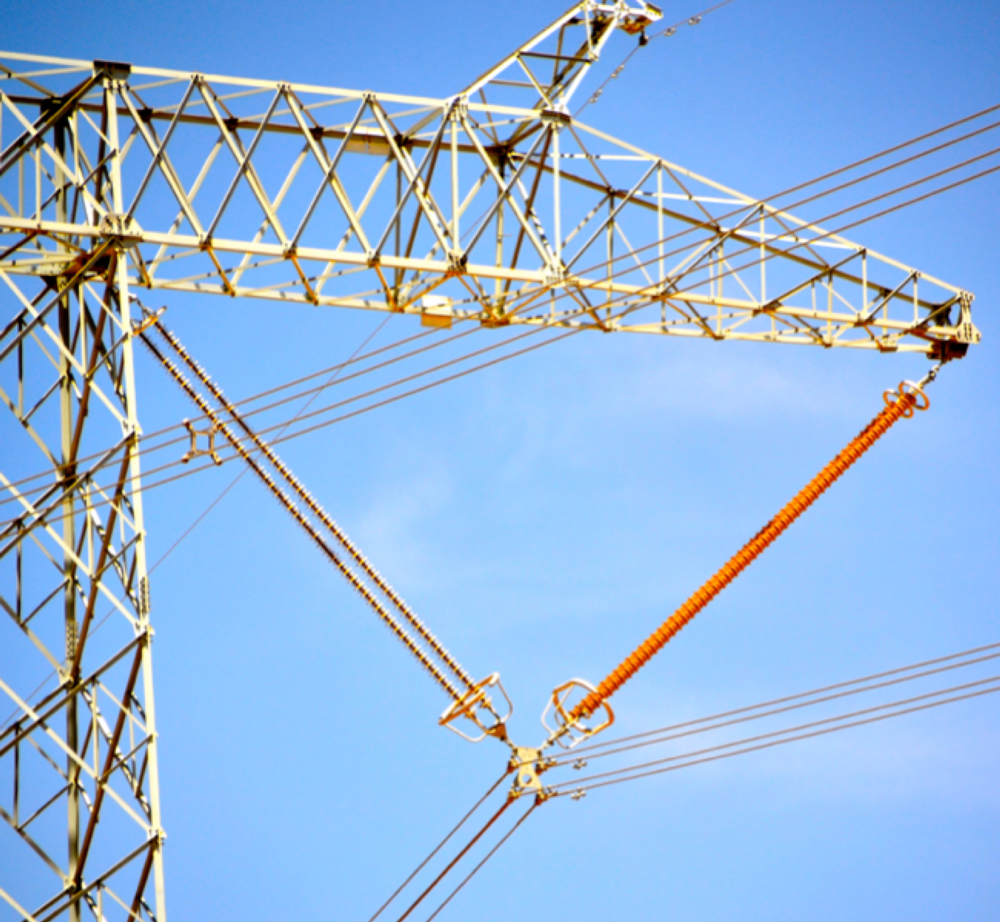
One of the goals of the new Intertie was to increase reliability of the Tibetan power grid given major outages whenever a local hydropower plant that supplies a high proportion of the total power had to interrupt operation. The new ±400 kV line also permitted power flow between Qinghai and Tibet to be adjusted to meet the needs of better exploiting the region’s natural resources.
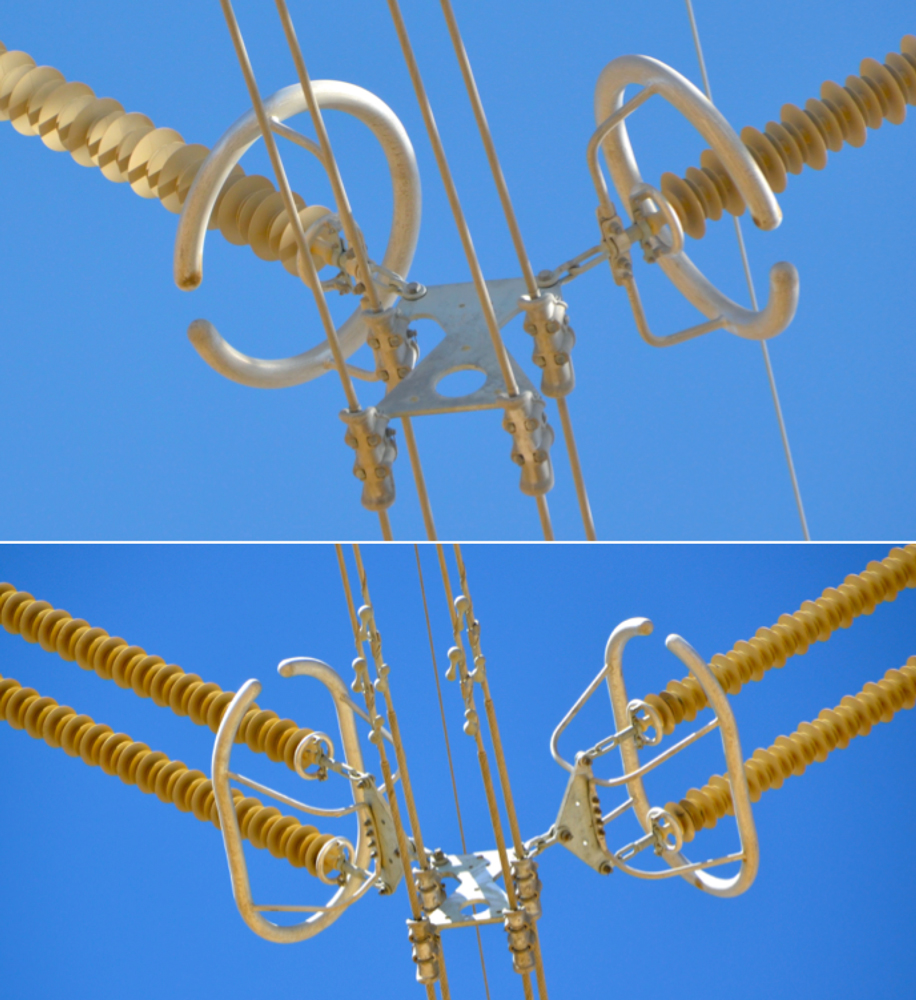
The original intent was for the HVDC line to be designed for ±500 kV. But constraints in external insulation at these altitudes combined with the realization that power demand in Tibet did not require such a system voltage resulted in the project being scaled down to ±400 kV. One of the key considerations when it came to specification of insulators and hardware such as fittings and corona rings involved the extreme altitude. Other factors included perpetually high UV and frequent cold in the area through which the line runs.
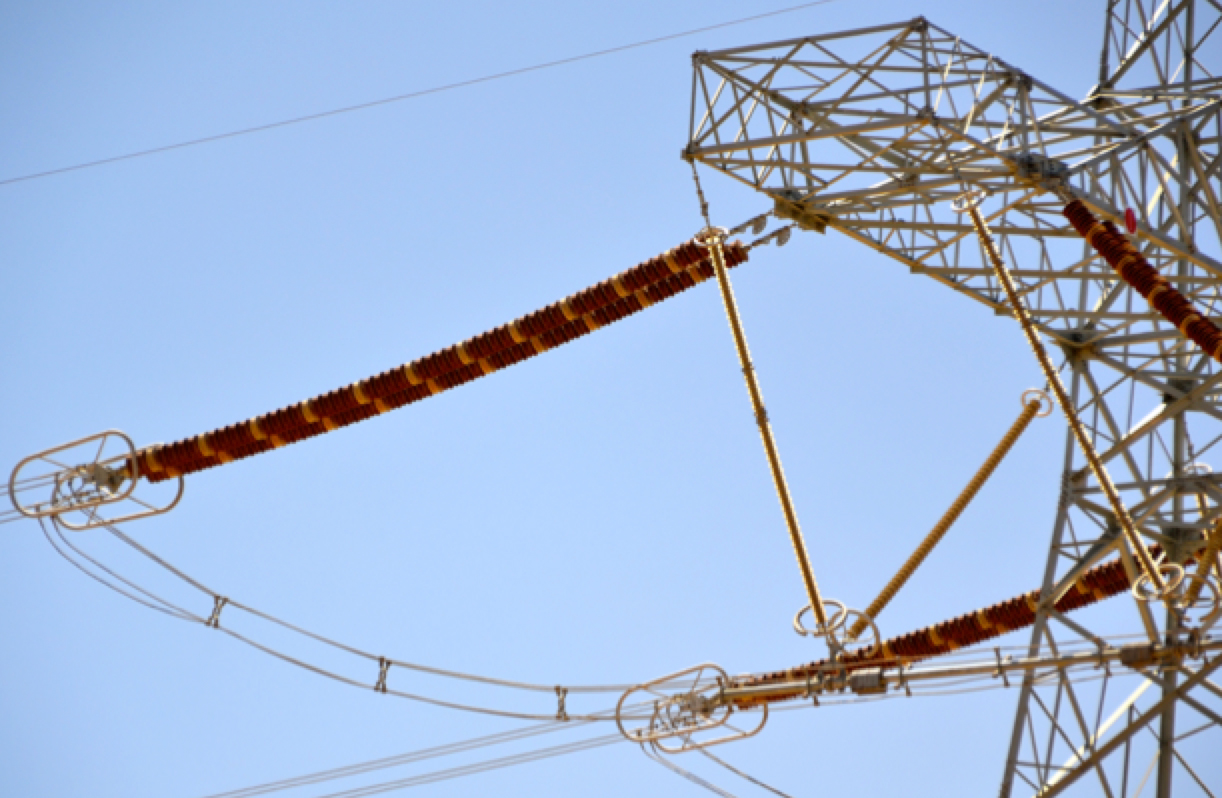
The decision to select silicone composite insulators for all suspension applications on the HVDC line was based on an assessment of their relative advantages and disadvantages in relation to porcelain and glass strings. Both ceramic technologies have a history of successful application on Chinese power systems and a variety of possible shed designs might have been able to satisfy the line’s pollution performance criteria. However, regulations in China require that porcelain discs be checked regularly for loss of dielectric. Conducting such inspections annually on every tower across remote regions of Qinghai would create a maintenance challenge. Moreover, should the number of zero value insulators in any string become critical due to insufficient inspection, this could quickly lead of flashover.
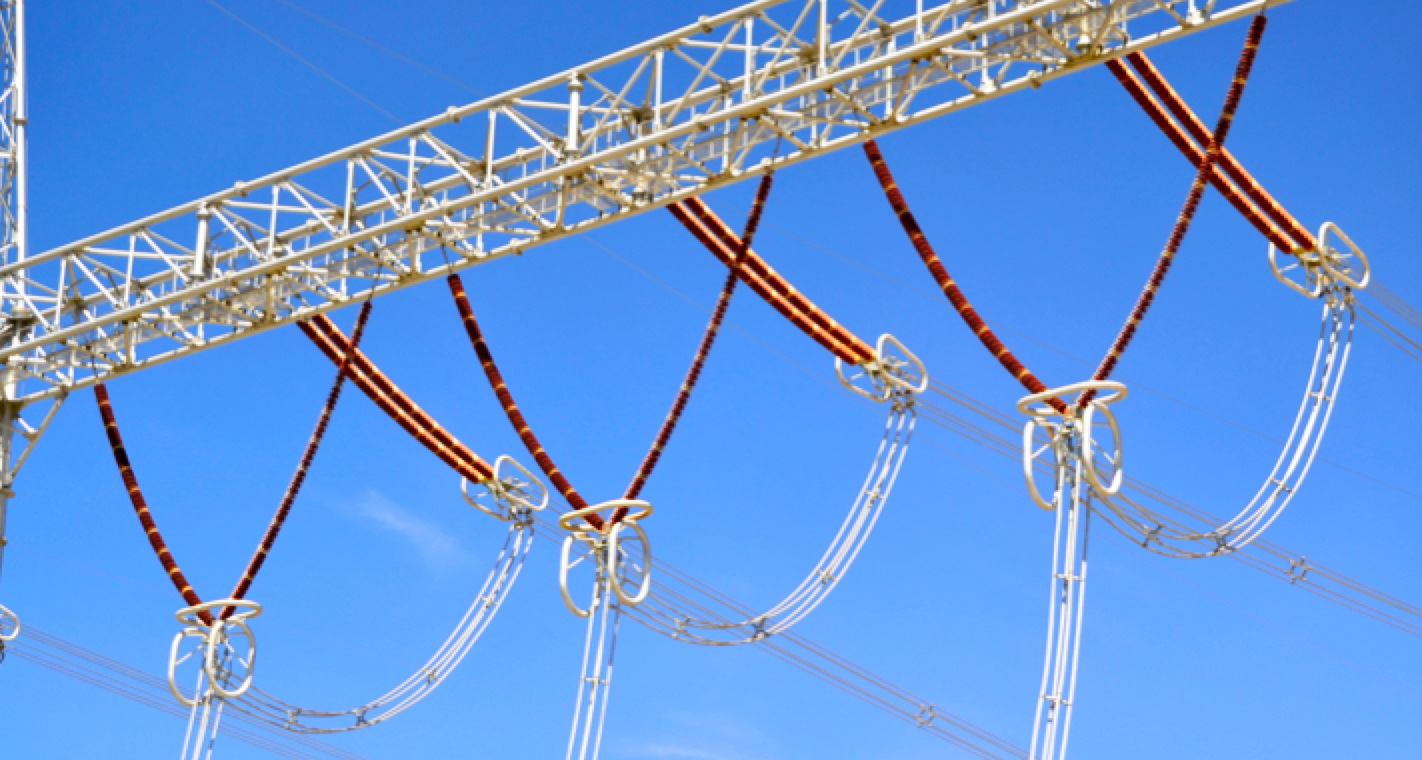
As for glass insulators, higher thunderstorm activity south of the Yangtze River (the traditional demarcation line between China’s north and south) has made toughened glass a more popular choice there than porcelain. By contrast, experience with glass in the northern region between Qinghai and Tibet has been less and replacing discs that self-shatter across the rugged terrain would pose a maintenance challenge. In addition, while double shed discs are preferred for insulator strings in northern China due to greater local dust and pollution problems there was still little operating experience with such designs in glass at the time the line was being designed.
Given the decision to specify composite insulators for all suspension applications on the new ±400 kV line, there were still two key issues to resolve given the service environment: possible premature ageing under the constant high UV and risk of reduced performance under the frequent cold. The issue of UV resistance was addressed by the insulator manufacturer through incorporation of fillers to ensure that chemical bonds in the silicone rubber polymer are not broken by high-energy UV rays. Moreover, the material used for insulators on this line was a unique formulation in respect to higher than normal tear strength, i.e. over 20 kN/m versus the typical 7 kN/m. This was another issue to address given that experience with high winds along 750 kV AC lines in desert regions of China’s northwest had demonstrated that wide sheds are susceptible to tearing under constant wind shear.
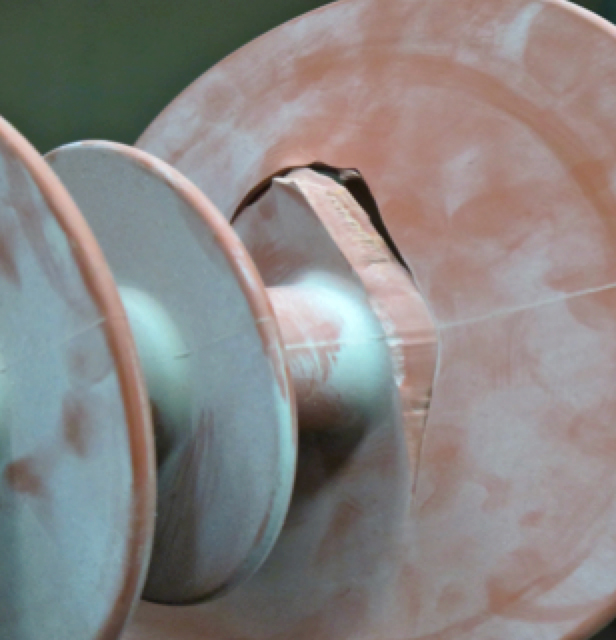
In regard to impact of sustained cold on insulator performance, operating experience in China suggested that hydrophobicity of silicone is reduced at ambient temperatures of between -2 and -10°C. For example, flashover of such insulators at 220 kV had already been identified, typically on rainy mornings when temperature falls into this critical zone. Research confirmed that this was due to a relative loss of hydrophobicity. A related finding was that water on composite insulators turns to ice not a 0°C but rather at -3°C.
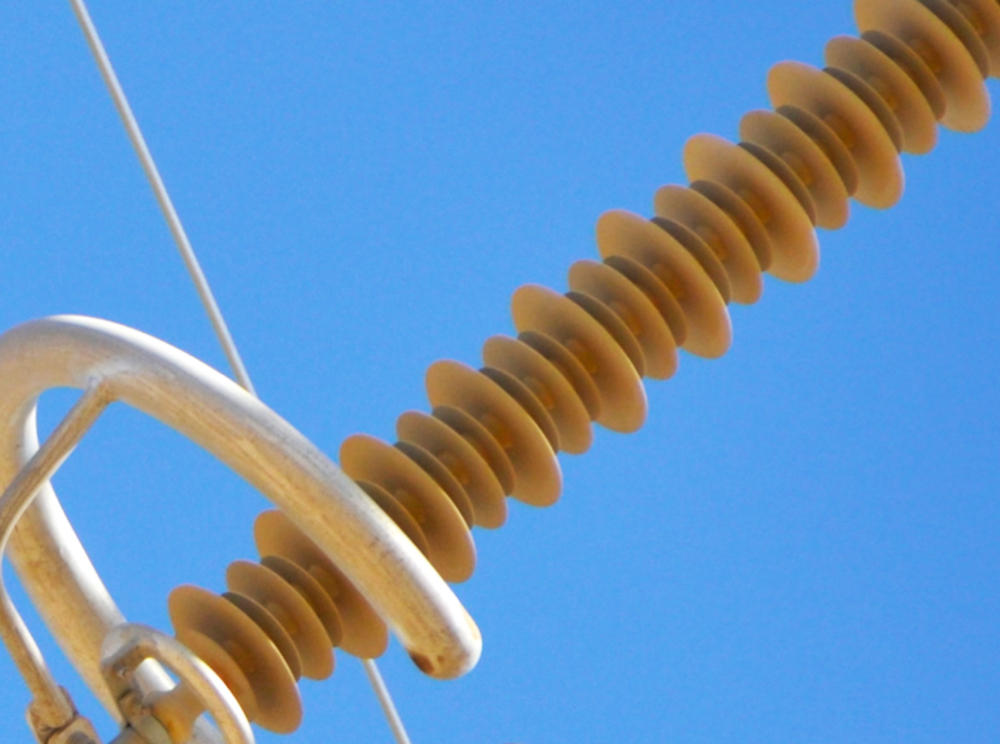
Overcoming the potential for reduced hydrophobicity of silicone rubber under persistent cold temperatures involved developing the most suitable shed geometry for the pollution environment. In the case of insulators for the ±400 kV Qinzang Project, this turned out to be three different shed diameters: small, mid-size and large, each separated by a distance of 40 mm along the shank and in a configuration where there is a small shed on either side of both the mid-size and the large sheds. As such, the distance between any two consecutive large sheds amounts to 160 mm, less than the 180 mm normally required in China for UHV applications.
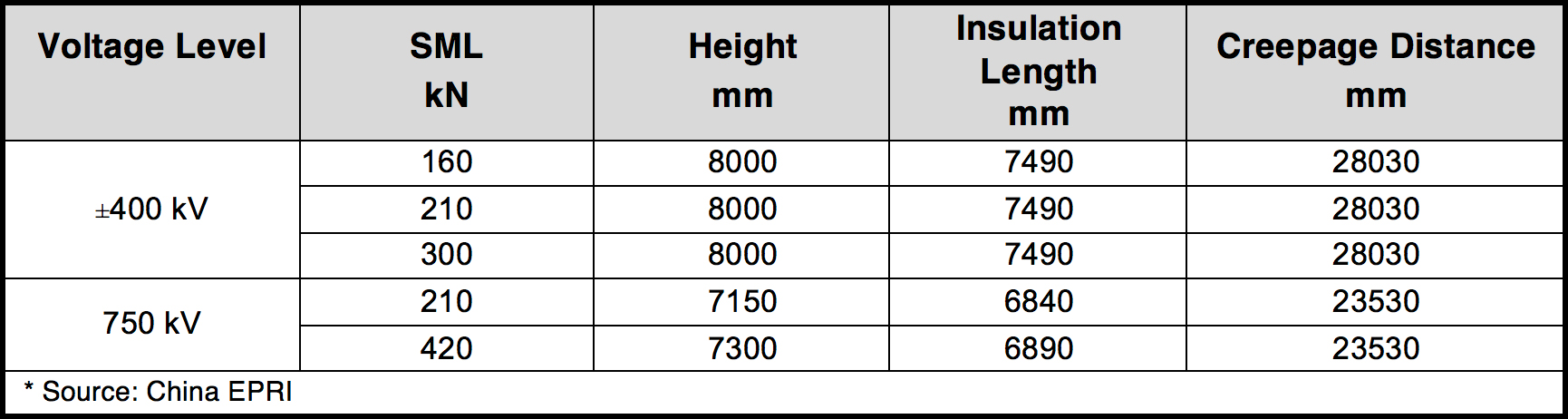
There are five main pollution classes in China – ‘A’ being the lowest and ‘E’ the highest. Unified specific creepage distance (USCD) then varies from a low of 22.0 mm/kV to as much as 53.7 mm/kV for ‘E’ type environments. This line was classified as passing through a type ‘C’ environment and the normally prescribed USCD requirement in this case would have been 34.7 mm/kV. Allowing for the fact that the line is DC and that about 88% of its length traverses areas with altitude exceeding 4000m, a correction factor of 1.28 was applied, resulting in a final USCD of somewhat more than 44mm/kV.
While suspension insulators on the new ±400 kV Geermu–Lhasa Line are silicone composite type, porcelain cap & pin strings dominate most tension applications. A small number of porcelain long rods were also initially selected for a handful of towers to obtain operating experience with how these perform in terms of self-cleaning in such a service environment. Application of ceramic strings for tension is typical on most UHV AC and DC lines in China even though composite insulator technology has been dominant in suspension. This is due mainly to concern about risk of damage to insulators from lines workers walking across strings for the purpose of conductor maintenance. Indeed, the issue of whether tension insulators should ever be composite type has remained a matter of controversy.
As part of the final process to confirm design parameters of the ±400 kV line in terms of tower clearances, on site testing was carried out in summer 2011. The findings allowed researchers to compare lightning and impulse switching data obtained from simulations performed before construction at the UHV test laboratory in Beijing (at 54m) as well as at the 4300m test station in Tibet. This work was carried out by the China Electric Power Research Institute (CEPRI) on a simulated tower structure located near Tanggula Mountain, the highest point along the line (some 5000m). According to CEPRI, minimum insulator length here would have to be 12m (with 14m the longest) versus the more typical 9.75m for an insulator used in UHV AC. These findings applied only to silicone insulators and would be longer in the case of porcelain.
One of the problems encountered during construction of several UHV projects in China involved bird attack on the sheds of silicone insulators before the line was energized. This same problem had also been reported in other countries where species with powerful beaks sometimes chewed away entire sheds. CEPRI researchers reported, for example, that about 2000 composite insulators on the 640 km 1000 kV line from Shanxi to Hubei were damaged by birds during the period after installation but before energization. While in most cases damage was minor and affected only a few sheds, in some cases the sheath itself became punctured and the insulators had to be replaced. This same problem of bird pecking reportedly also occurred during completion of the ±400 kV line to Lhasa, although it was never a major problem. Rather, a more serious incident involving birds was the line’s first flashover, recorded in January 2012 and attributed to short circuit from a bird streamer.
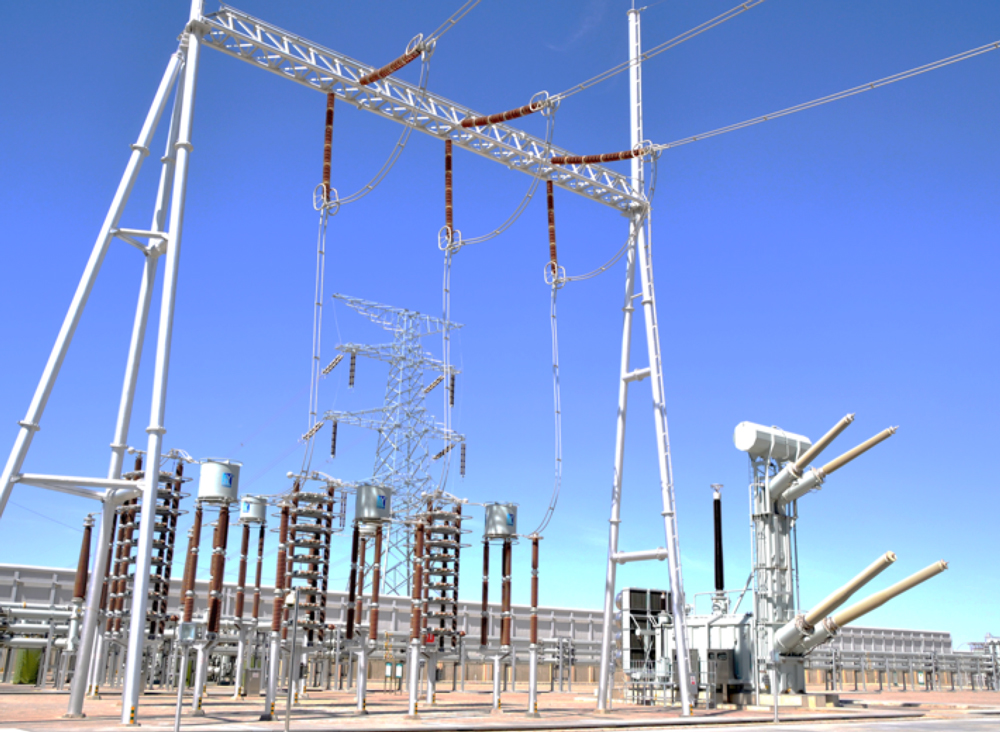
The origin of the ±400 kV line to Tibet is the Geermu 750/330/±400 kV Converter Station, a facility surrounded by vast stretches of open desert. The area has little industrial activity but the site has nonetheless been classified as type ‘C’, meaning moderate to high pollution. Contamination comes mainly from a nearby salt lake with a large extraction facility for alkalis. The impact of this salt lake is such that the windswept ground surrounding the substation is tinged by a coating of salt that mixes with dust and is kicked up by trucks driving along nearby dirt roads.
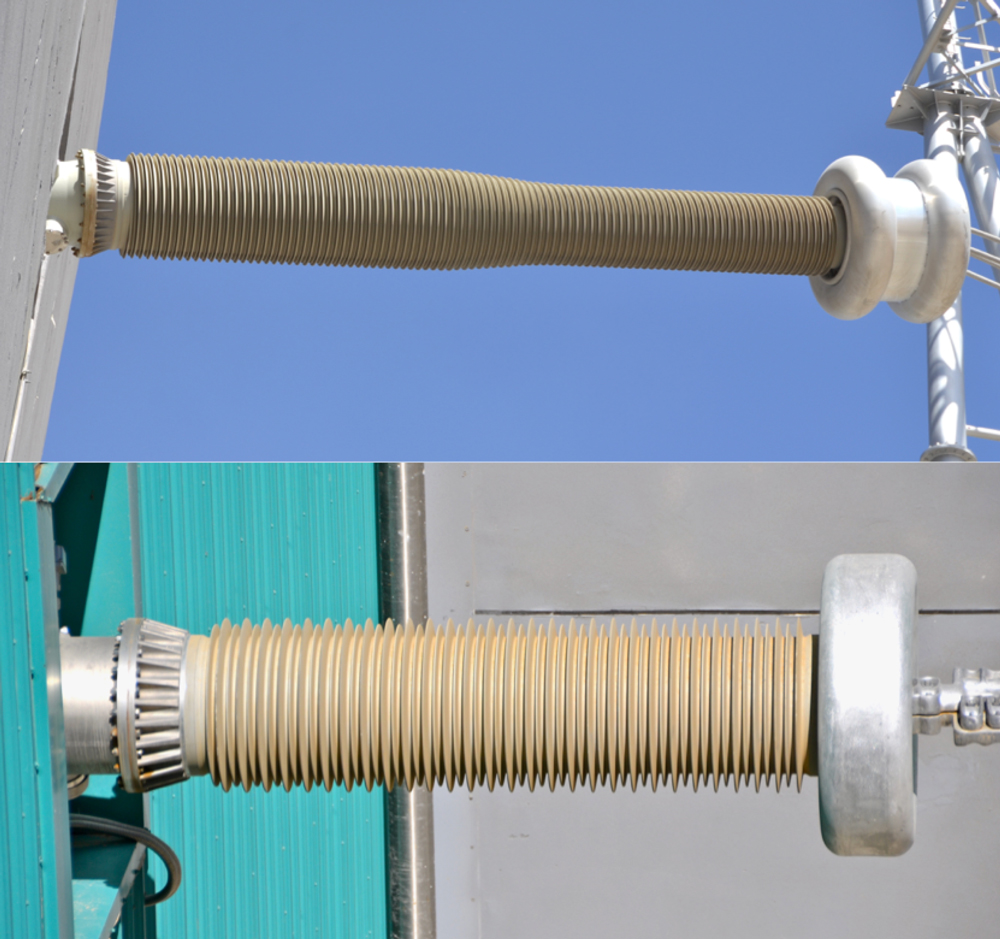
In fact, the pollution environment at Geermu is so challenging that all porcelain equipment housings and support insulators were coated with RTV silicone before the station was energized. Moreover, because of the high specific creepage distance and relatively narrow shed spacing required for porcelain, booster sheds were installed for sensitive applications such as the 750 kV GIS bushings to protect against bridging during heavy rain or from ice formations during winter.
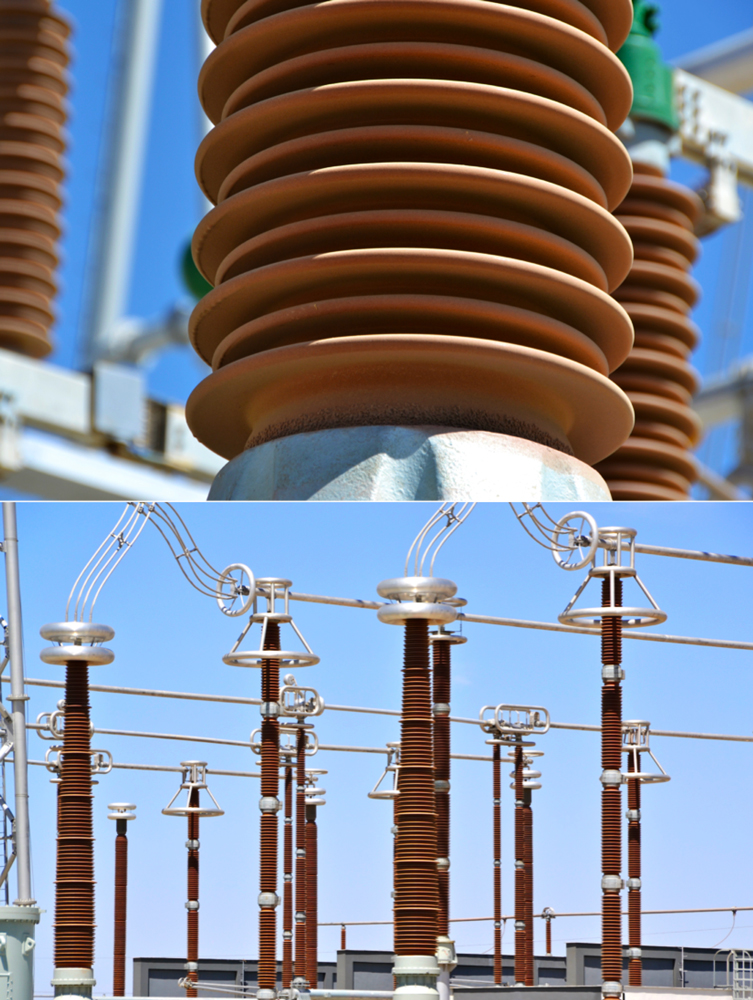
Another remedial measure against pollution was construction of buildings to house the DC fields, making this one of only three fully enclosed facilities in China at the time. The added cost of the enclosures was seen as justified because power arcs in DC are more difficult to extinguish and, considering the substation’s altitude of 2800m, the problem would be even greater.
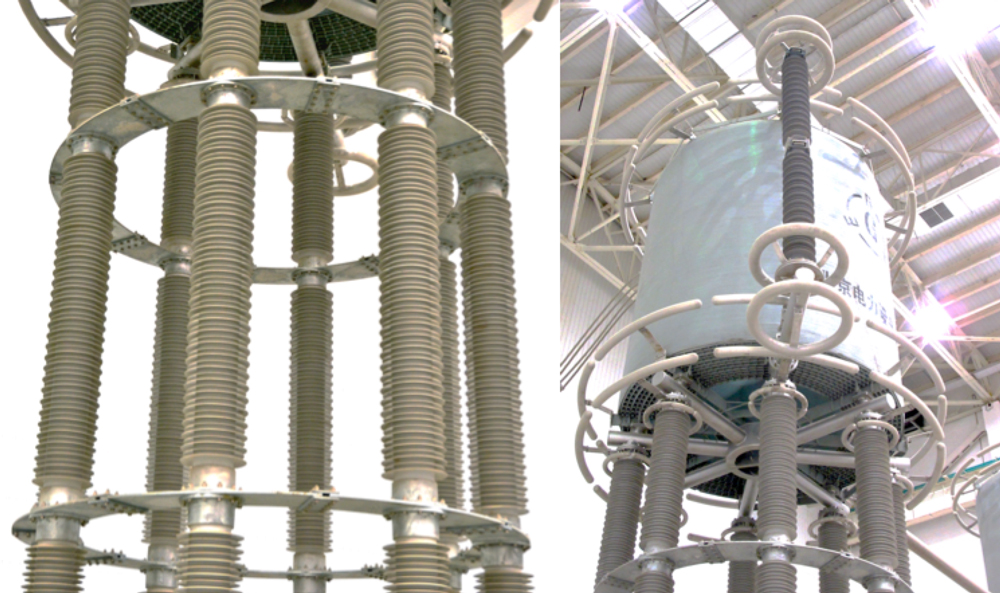
Given these risks and the high level of pollution, solid core reactor supports as well as arresters and CTs specified for the indoor DC fields were all equipped with silicone housings for added security. This applied as well to the converter transformer bushings outside the valve hall as well as to all wall bushings. A further safety feature was metal walls around the converter transformers, intended to shield substation staff from high noise levels when equipment was operating at or near capacity.
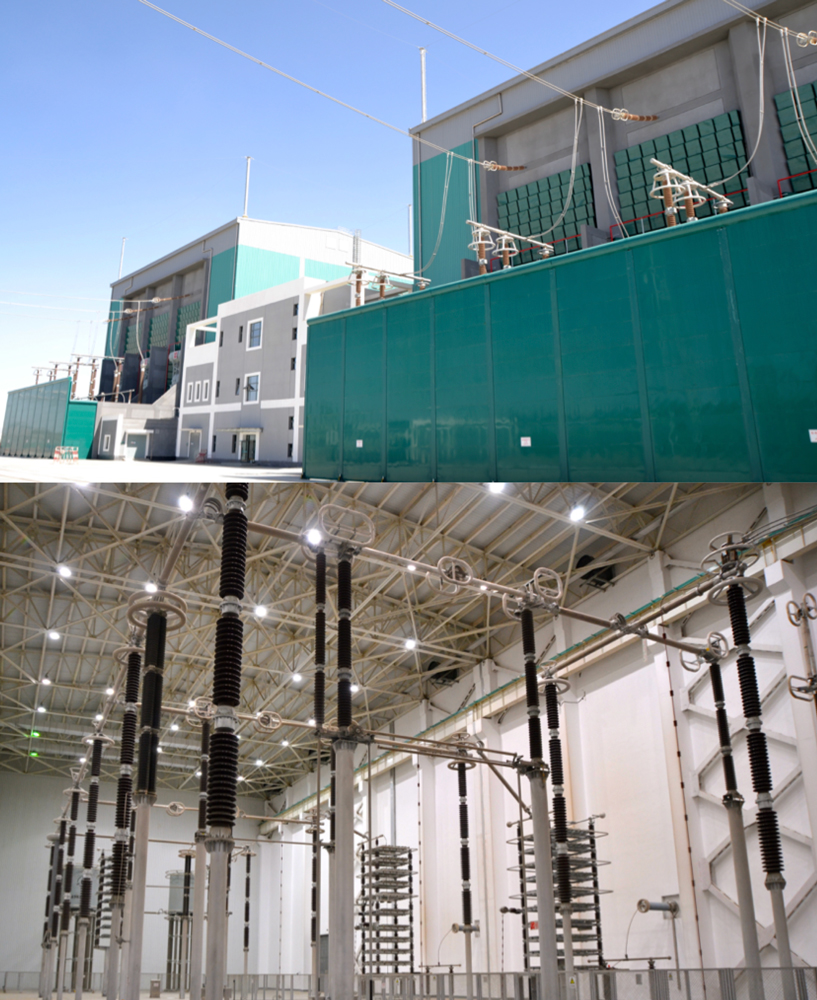
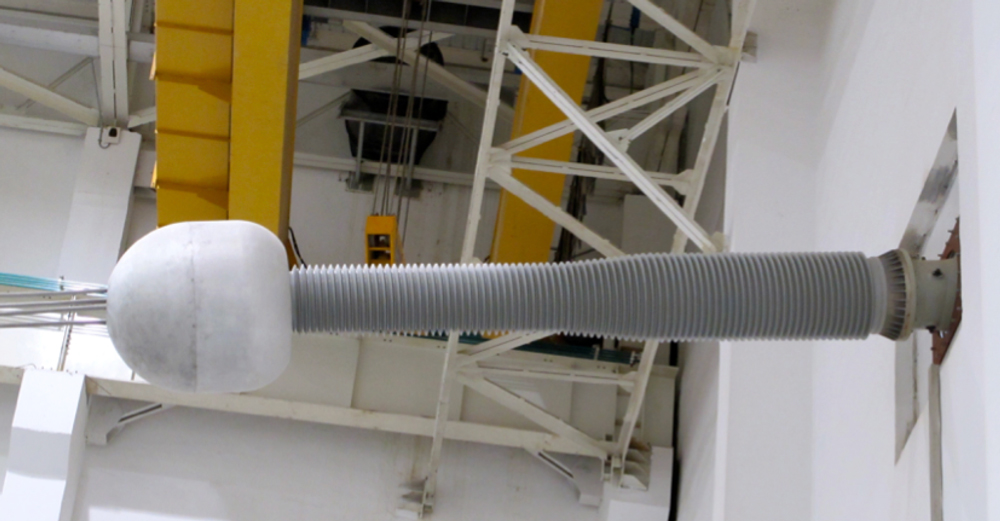
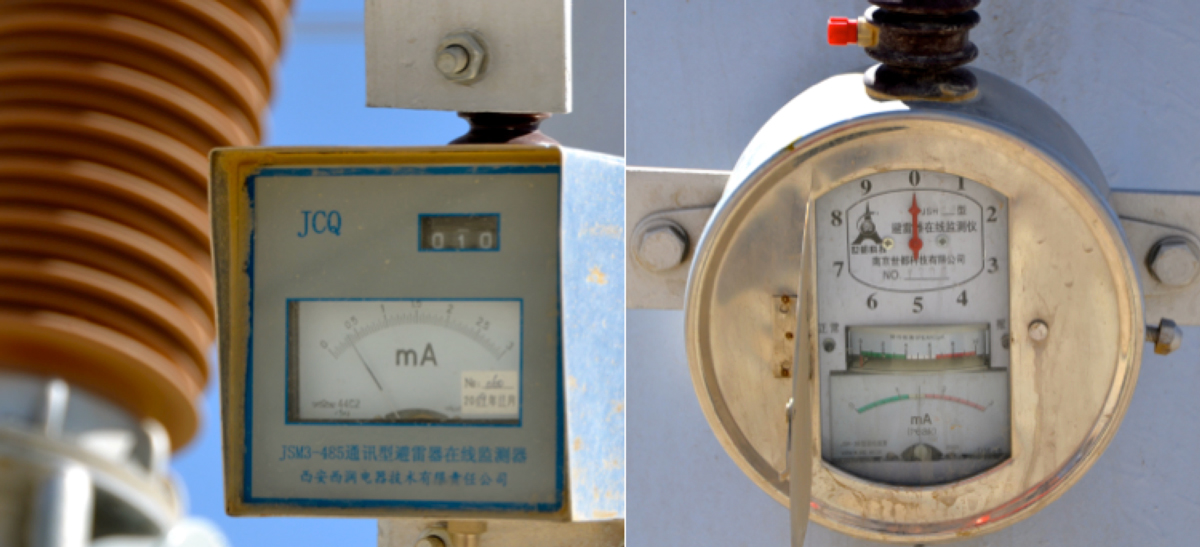
In spite of all the pollution countermeasures at the converter substation, night-time inspection several months after commissioning revealed surface discharges near the flange of 330 kV arresters. This occurred during a period of heavy precipitation, reportedly the first sustained rainfall after the substation was put into operation. Staff responded by verifying ESDD measurements to re-assess the level of pollution affecting the substation and, depending on findings, decided whether to implement remedial measures such as washing.
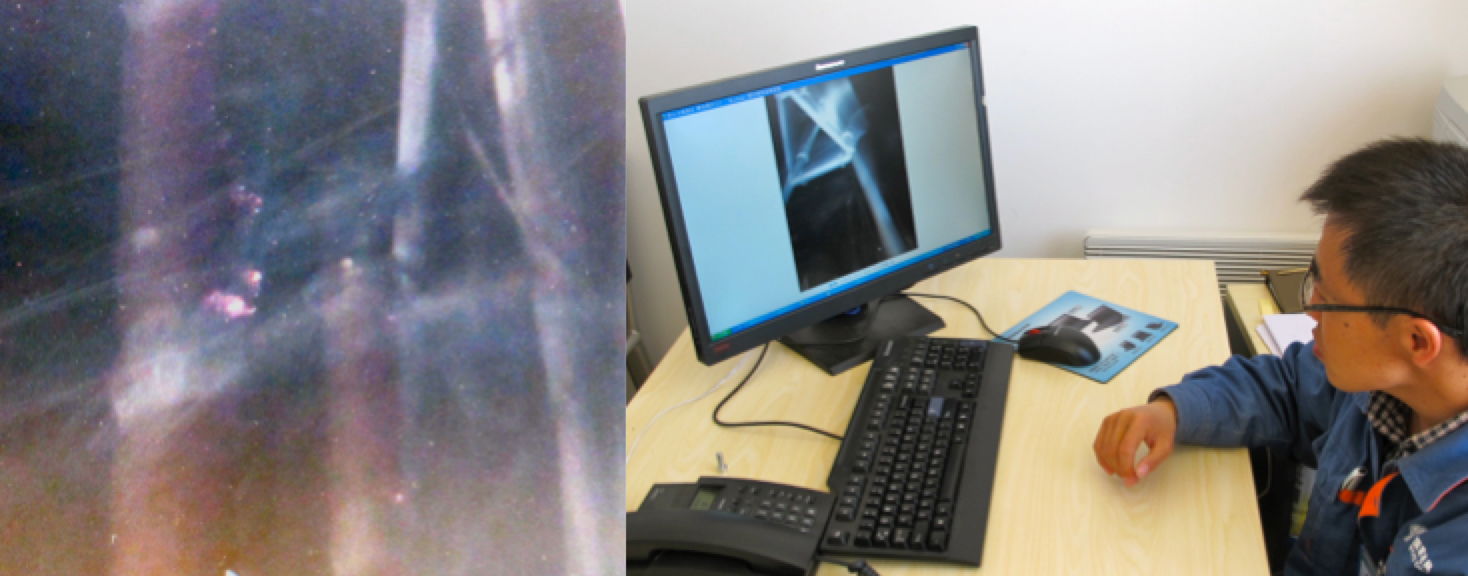
Over the years, China’s expanding HVDC and UHV DC networks have provided a growing body of service experience on which to base insulation decisions. For example, the country’s first HVDC line was built in the late 1980s using porcelain string insulators but, while designed for ±500 kV, operated in areas of extreme conditions at a lower voltage until 1997. The flashover rate on the line to that time was 0.07/100km/yr but this increased to 0.27/100km/year once the line was brought to its full design voltage. Research was carried out into why flashover rate increased and the insulation was subsequently changed to silicone rubber composite type, at which point the rate dropped back to 0.07/100km/yr. Also of note was that post insulators at the line’s converter stations had originally been designed with 40 mm/kV specific creepage but that this was eventually considered too low for ±500 kV application. Over subsequent months, RTV silicone and booster sheds were applied while some porcelain posts were exchanged for ones made with silicone rubber housings.
Experience on UHV DC lines in China since 2010 also revealed problems of corrosion affecting metal fittings of porcelain ‘V’ strings – a situation that for example affected some 20,000 disc insulators on the 1400 km line running from Yunnan to Guangdong. No ‘I’ strings were involved since the phenomenon seems to be initiated by rain coming from the side of a string in the ‘V’ configuration. Apparently, the problem involved the lines negative pole and affected only insulator caps that, unlike pins, were not outfitted with zinc anti-corrosion rings. Ferrous oxide and zinc oxide residues migrated down onto the porcelain surface turning it yellowish.
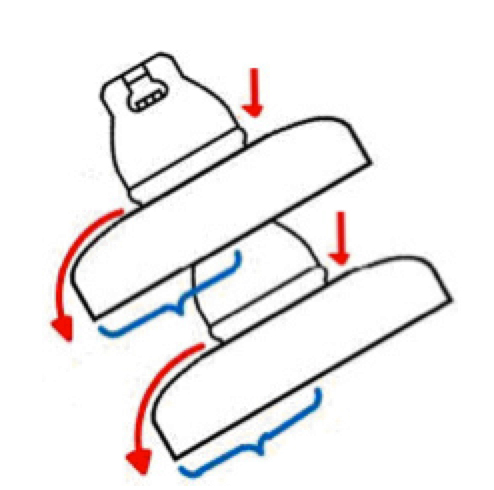
Research into this phenomenon revealed that the conductor was at negative polarity and the cap at relatively positive polarity. During periods of heavy rain, some electrolytic activity took place, which resulted in corrosion. While not necessarily a serious operating problem, Chinese standards still required that all affected porcelain discs had to be replaced. A similar problem was reported on the Xiangjiaba to Shanghai ±800 kV line as it passes through Hubei Province but involved a much smaller number of discs – only about 2100.
Much of the problem of corrosion of caps was geographically focused due to local weather conditions and no program of replacing affected discs was initially undertaken. Since other ±800 kV DC lines that traverse the same type of service conditions, such as the Jinping to Jiangsu line, could be expected to encounter a similar problem, remedial measures were undertaken in the form of zinc rings fixed to the bottom of the caps of porcelain discs. Research confirmed that such a solution prevents risk of corrosion.
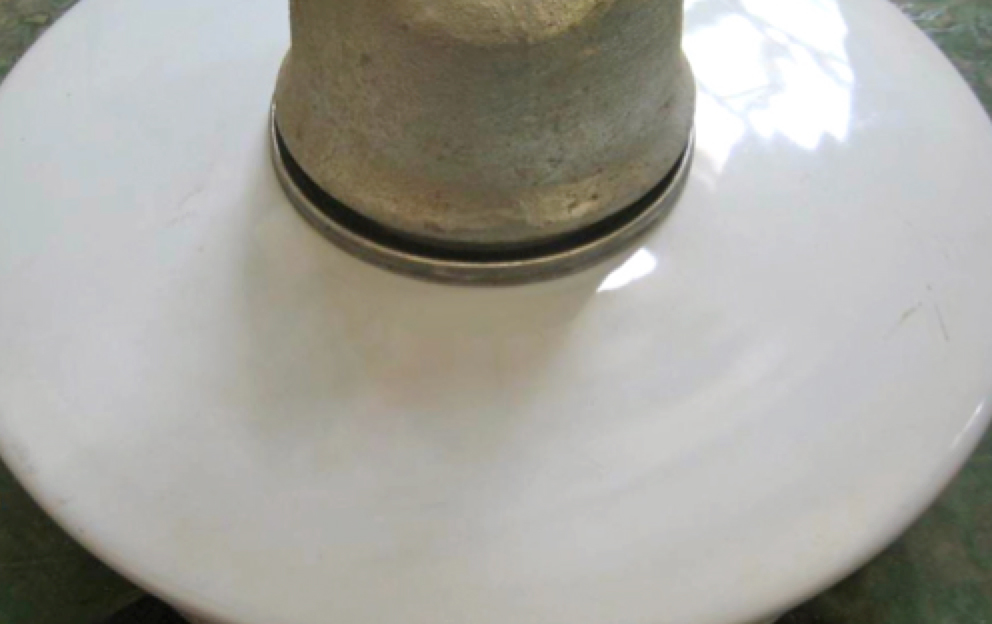
This type of problem affecting other DC lines in China is thought never likely to be a concern in the case of the Geermu-Lhasa line. To begin with, leakage current on the silicone rubber insulators here is much lower than on porcelain V-strings used elsewhere. Also, there is much less chance of heavy rain along the line’s route. Finally, a zinc ring was fixed on all the fittings of these silicone insulators.
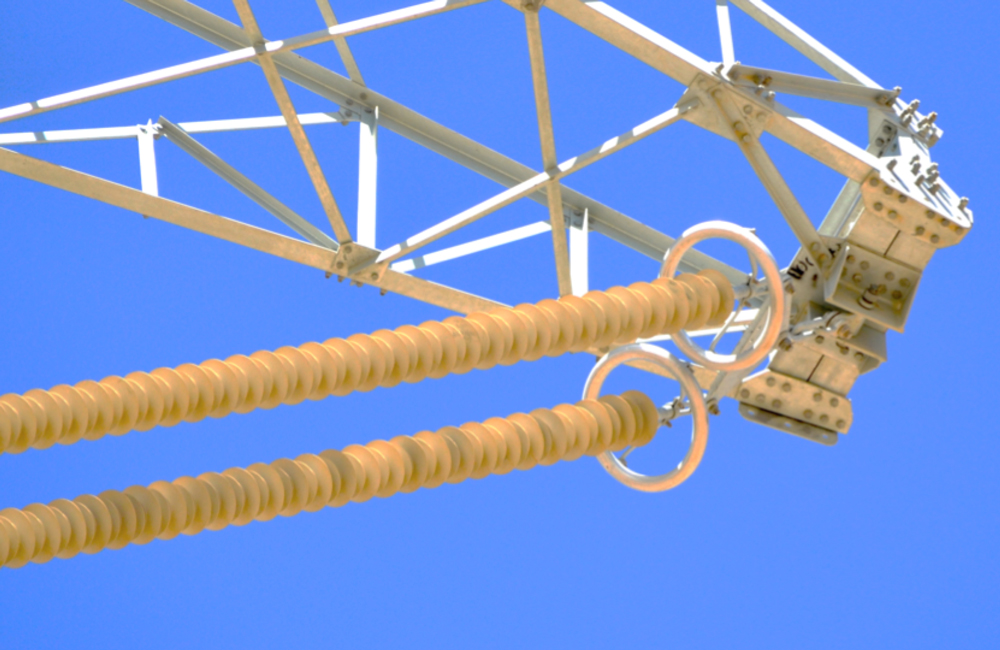
The Geermu Substation, while in a difficult service environment of dust and salt, has relied mainly on RTV silicone coatings to ensure pollution performance. However, other substations in China’s expanded northwest UHV grid have since made much greater use of composite insulators. For example, the entire 750 kV AC Shazhou Substation in Gansu Province, commissioned in 2013, relies on composite insulation – from busbar supports to bushings to disconnectors to live tank breakers to CTs, and so.
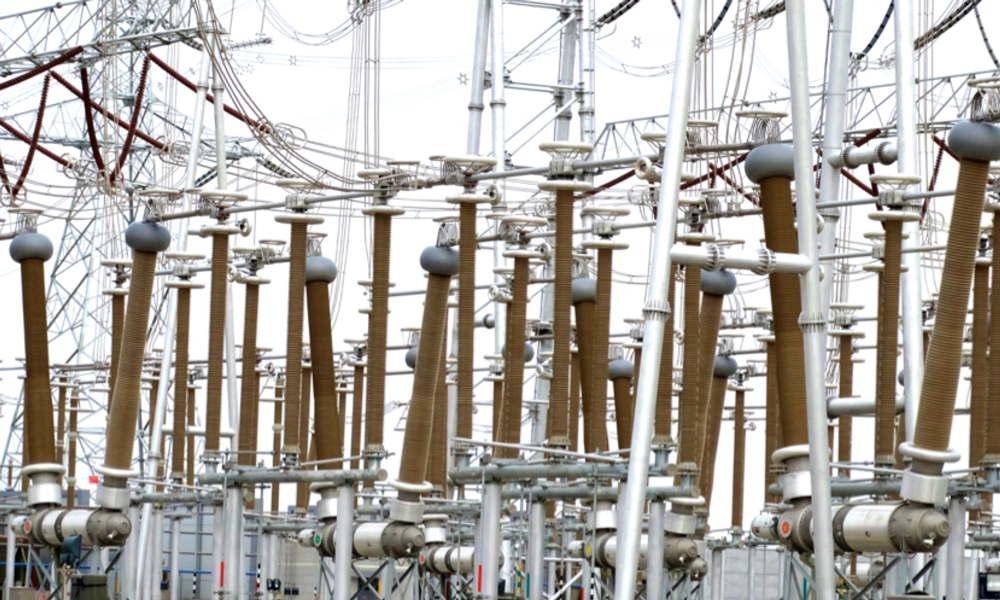
[inline_ad_block]