Polymeric insulators were first installed in Peru in 1996 with the goal of reducing need for frequent insulator washing on transmission lines in coastal areas with heavy salt pollution, high humidity and scarce rainfall. However, after only a few years in service 17 failures occurred due to breakage of the insulator core. This forced a rethink of the strategy for insulator selection and maintenance by the country’s TSO, Red de Energia del Peru (REP).
Starting in 2009, RTV coated glass insulators began to be installed to replace polymeric types on lines in problematic coastal areas. But while research on coatings suggested good results in increasing pollution withstand, reports from the field described cases where performance fell below expectations. This was due to factors such as rapid loss of hydrophobicity, weakened ability to suppress partial discharge activity and coating pulverization.
This edited 2019 contribution to INMR by Samuel Arturo Asto Soto of REP and D.A. Da Silva of Brazil’s Military Engineering Institute described experience with RTV coated glass insulators installed on transmission lines on the Peruvian coast. Performance was reviewed as was the path taken to ensure optimal insulator maintenance and replacement under the severe service conditions.
Note: INMR visited one of these problematic lines in February 2024. Next week’s INMR WEEKLY TECHNICAL REVIEW reports on the recent installation of new RTV-coated glass insulators on one of REP’s important 500 kV coastal lines.
The first transmission lines constructed by REP in coastal areas were limited to 220 kV and utilized porcelain and glass insulators. These areas usually received special attention due to service characteristics that include high temperature and humidity, dense fog and a short rainy season that does not allow for natural insulator washing.
As shown in Fig. 1, the Peruvian coastline is affected year round by a wind component coming from south. These winds blow salt particles inland that deposit onto surfaces of electrical components. Porcelain and glass insulators installed in these areas therefore had to be frequently cleaned. However, high cost made such a maintenance strategy no longer economically feasible.
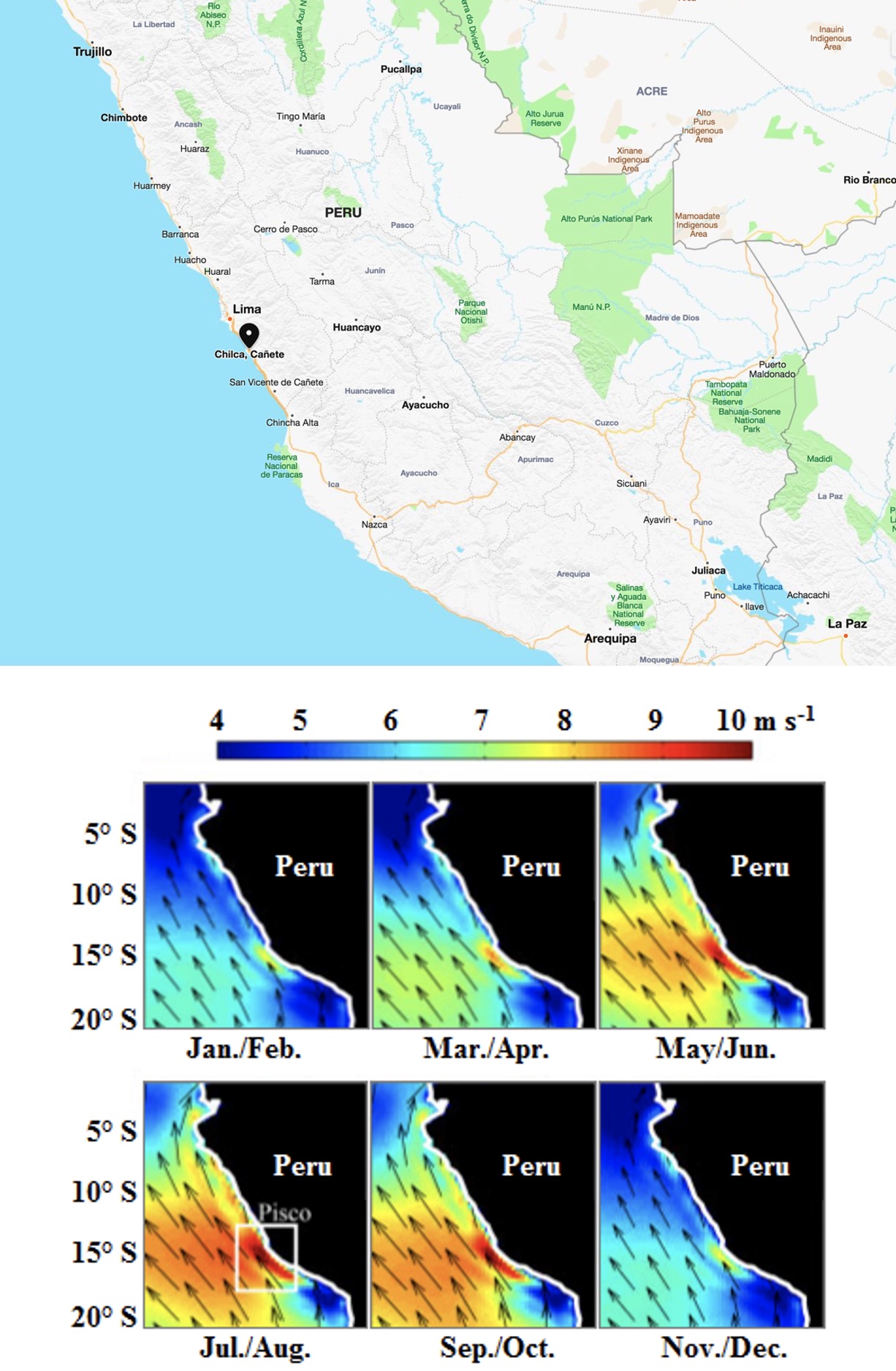
Starting in the 1990s, porcelain and glass insulators were replaced by polymeric types with the expectation, based on manufacturer claims, that these would not require maintenance for up to 15 years. Unfortunately, the polymeric insulators selected did not perform as expected and in fact experienced brittle fracture failures. Based on this, application of RTV silicone coated glass insulators was implemented as of 2009 to replace polymeric types on lines in coastal areas suffering from high rates of corrosion and pollution.

Initial Maintenance Strategy for RTV Coated Glass Insulators
Since there was no local experience covering RTV coated glass insulators installed in coastal areas with severe conditions, a succession of maintenance strategies came to be developed. One method to monitor insulators subject to saline and industrial contamination is by visual inspection using observed level of effluvia (discharge phenomena) to estimate degree of surface pollution. Such an evaluation is best carried out using a night vision camera that relies on absence of background daylight to more easily characterize effluvium (see Table 1).

The initial strategy, based on recommendations provided by coating manufacturers, contemplated replacing coated insulators in the 10th year after commissioning. No preventive maintenance was expected over the time between installation and replacement, except for periodic visual inspection and assessment of effluvium. However, the service conditions along South America’s Pacific coast forced this strategy to be re-evaluated.
RTV silicone coated glass insulation was indeed found to offer excellent performance along coastal areas and some areas saw these insulators in service for up to 10 years with no events or failures due to marine pollution. However, starting in the 5th year after commissioning, between 2015 and 2017, 220 kV and 500 kV lines located less than 5 km from the sea but nonetheless exposed to high pollution began to experience failures or discharges due to contamination.
Fig. 3, for example, shows an affected insulator string installed on the 220 kV line in a central coastal area between Huanza and Caraballo. Fig. 4 shows an insulator that experienced pollution flashover on the 500 kV transmission line from Chilca to Carapongo.
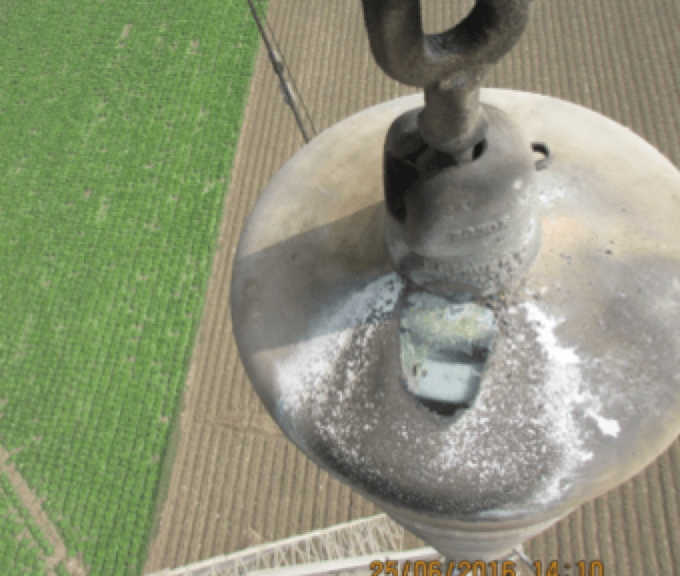
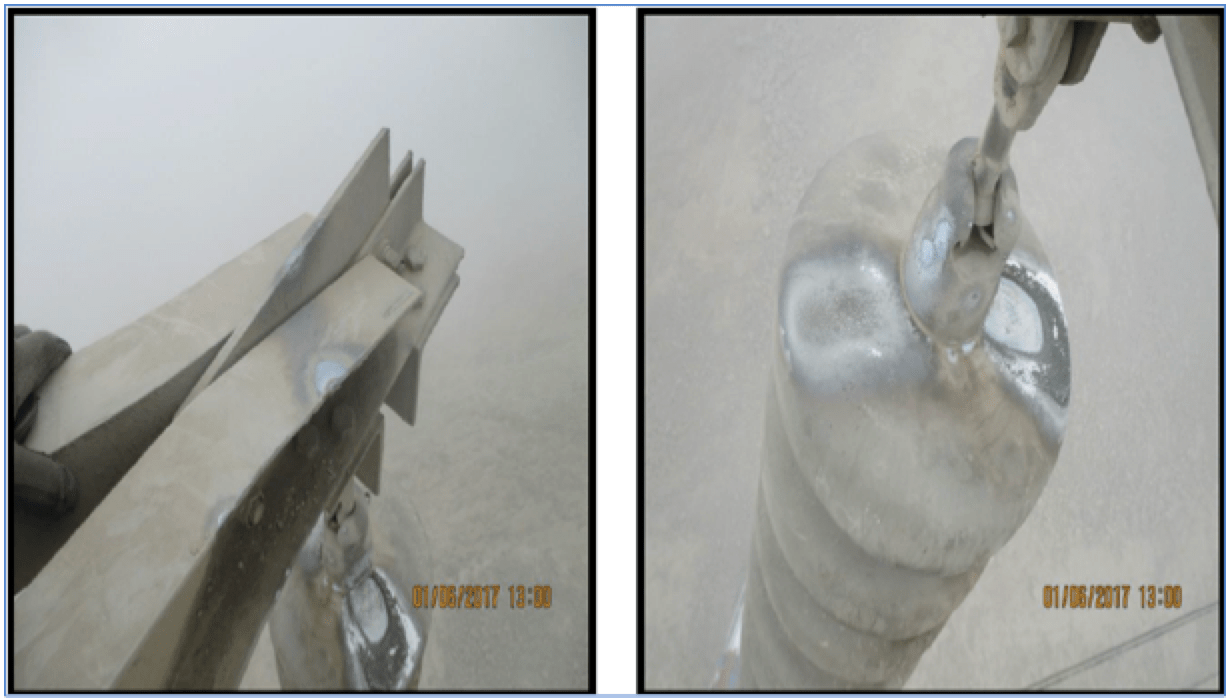
The 500 kV line from Chilca to Carapongo, which runs through the highly polluted central coastal area of Peru, recorded 7 faults due to contamination of its coated glass insulators between the 4th and 6th year after installation. Analysis revealed:
• Presence of a high salt pollution layer with signs of electrical discharges;
• Fault zones were mostly in areas with high humidity, high contamination and almost no rain
• While international standards consider extreme contamination as an NSDD of 0.3 mg/cm2, analysis conducted by one glass insulator manufacturer found NSDD of 1.2 mg/cm2 in this region;
• Increased humidity during winter and autumn
Root cause analysis of these faults pointed to the need to revise the initial maintenance strategy applied to coated glass insulators operating in highly polluted areas. This revision in strategy proposed a new activity which consisted of manually cleaning RTV silicone coated insulators with a wet cloth. For example, in 2017, conclusions from analyzing cost, risk and performance for manual cleaning of the 500 kV Chilca – Carapongo Line using wet cloth were:
1. Clean RTV silicone coated glass insulators with a wet cloth, to be carried out with the following frequencies based on local service conditions:
• Areas of high contamination and humidity (i.e. line section between towers T-111 to T-173): every 4 years.
• Areas of medium pollution and high humidity (i.e. line section between towers T-1 to T-110): every 6 years.
2. Review concession contracts with the Peruvian Government to consider the scope and obligations to be fulfilled and thereby avoid payment of compensations, penalties and fines.
Similarly, it was decided that these same criteria should also be applied to other 220 kV and 500 kV lines equipped with coated glass insulators. Fig. 5 shows manual cleaning of coated insulators.
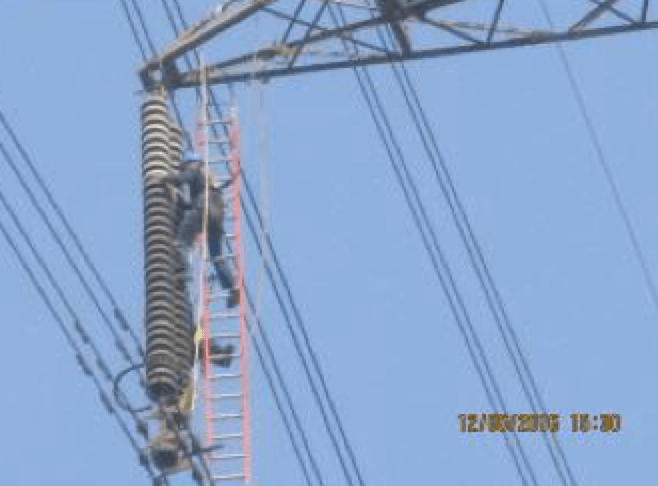
Maintenance Strategy for Critical Lines
The maintenance strategy described above was initially proposed to be applied to all lines equipped with coated glass insulators and operating in areas of very high pollution. However, due to budgetary limitations as well as lingering uncertainty, a decision was made in 2018 to apply this policy only to the 500 kV line connecting Chilca and Carapongo. Insulator maintenance on other lines would then be carried only based on necessity.
At the same time, in the case of the 500 kV Fenix-Chilca and Olleros-Chilca lines it was observed that only 12 months after insulator cleaning there were already critical levels of effluvia (see Fig. 6). These two lines operate in areas considered to suffer from very high marine pollution. Such a situation should not have occurred since, based on manufacturer claims, the RTV silicone coating was expected to recover some of its initial hydrophobicity after cleaning. It should therefore not be necessary to clean it again in the short term.
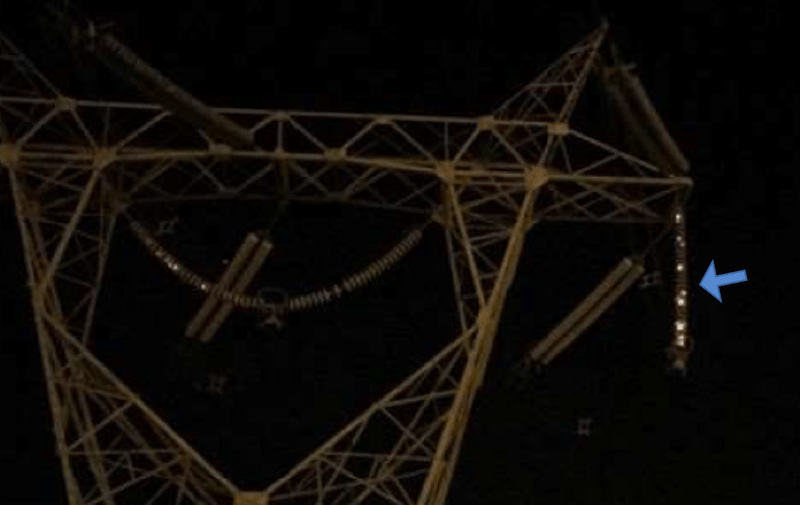
Based on this latest experience, it was felt necessary to revise the maintenance strategy for manually cleaning insulators. In this regard, a cost, risk and performance evaluation was made to adjust cleaning frequency on critical 500 kV lines (i.e. Fenix – Chilca and Olleros – Chilca) as well as on the 220 kV line connecting Zapallal and Huacho, all of which pass through areas of high pollution
500 kV Fénix-Chilca Line (L5011)
This transmission line connects the 580 MW Fenix Generating Substation to the Chilca Substation. Despite being only 7.5 km long, it is a critical line because the area in which it operates is characterized by heavy marine pollution with high humidity, especially in winter. Moreover, any failures on this line that could result in service unavailability with high compensation payment imposed as per Peru’s quality standard. For example, only 28 months after its commissioning, presence of effluvia was detected leading to the decision to clean the insulators due to failure risk. Yet only 18 months later, high levels of effluvia were again observed.
An investigation was conducted to define the optimal frequency to clean coated insulators on this line based on cost, risk and performance analysis. Four different scenarios were investigated and Table 2 indicates the savings involved with each.

Maintenance frequencies of 6 or 18 months would mean that these tasks had to be carried out during different months, which would present a planning challenge given that the generation plant interrupts service only once a year during its annual maintenance shutdown. This is why a 12-month interval was selected and which also proved to be the best choice. For example, a nighttime inspection was carried out in March 2019 to diagnose level of effluvium on insulators. This inspection revealed that 50% of insulator strings cleaned only 12 months earlier already showed presence of effluvia that ranged between Grades 2 and 3 (see Fig. 7). This indicated that these must be cleaned. Had this same inspection been done during a season with only medium humidity levels, once winter came with its higher humidity, effluvia would likely have reached greater levels, possibly leading to insulator failures.
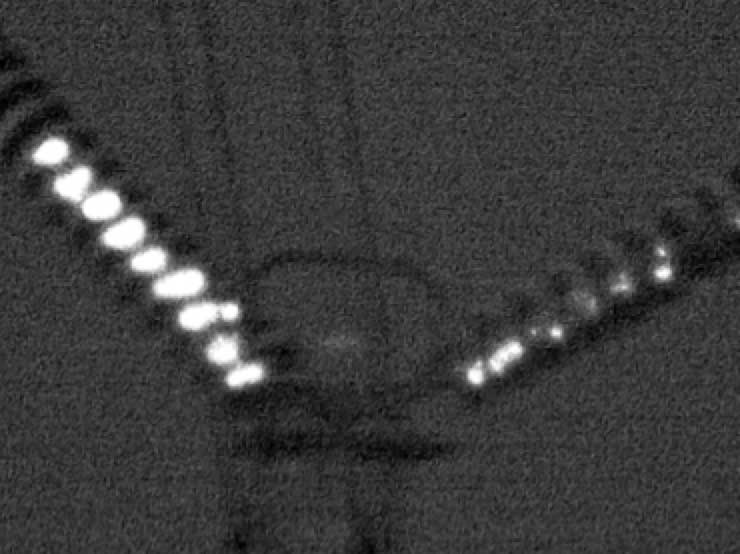
500 kV Olleros-Chilca Line (L5013)
Line 5013 connects Santo Domingo de Olleros Substation to SE Chilca Substation with approximate length of 1.76 km at 500 kV and 700 MVA capability. Considering the same maintenance costs, penalties for unavailability and repair costs for failures as in the case of L-5011, seven different scenarios were analyzed with a 6-month time interval between each. Table 3 describes findings. In this case, a cleaning frequency of 36 months was the maintenance interval finally selected because of lowest overall cost.
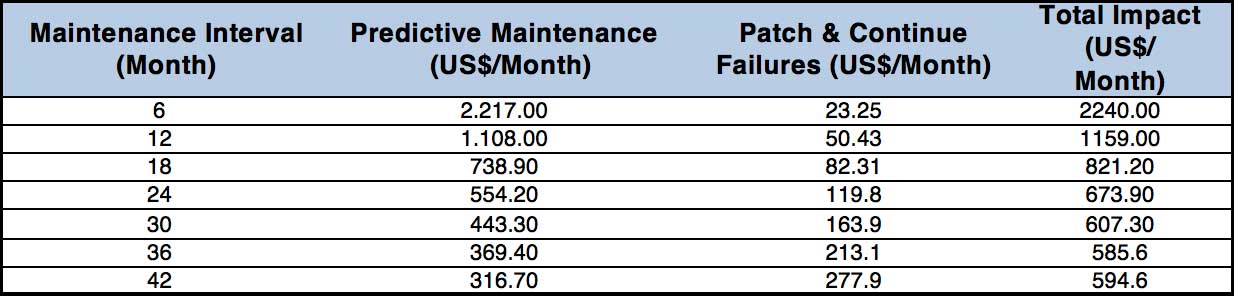
Conclusions
• 10 years after installation of RTV silicone coated glass insulators on ISA-REP transmission lines, it has been verified that these insulators offer superior performance versus uncoated glass insulators and also much better than conventional polymeric insulators, since failure rate and maintenance costs are reduced.
• Service experience during this period has allowed understanding actual performance of this type of insulator on transmission lines operating in coastal areas of South America, with their unique climatic characteristics.
• It is recommended to re-examine current standards so as to include levels of contamination occurring in South America when it comes to pollution level classifications as well as suitable insulator design for these areas.
• Design and testing of polymeric insulators for coastal areas should be reviewed to provide alternatives that equal or exceed the performance offered by coated glass insulators.
• Actual performance of coated glass insulators in coastal zones of Peru has made it possible to determine that the most suitable strategy for maintaining this type of insulation, based on technical-economic evaluation as well as cost, risk and performance analysis, is to carry out manual cleaning every 4 to 6 years for lines operating in highly polluted service areas.
References
[1] E.A. Cherney, “RTV Silicone – A high tech solution for a dirty insulator problem”, IEEE Electr. Insul. Mag., Vol. 11, No. 6, pp 8-14, November-December 1995.
[2] Lambeth PJ, Looms JST, Stalewski A, Todd WG,
Surface coatings for H.V. insulators in polluted areas, Proc. IEE, Vol. 113, No. 5, May, 1966, pp. 861-869.
[3] IEEE Committee S-32-3, Protective coatings for improving contamination performance of outdoor high voltage ceramic insulators, IEEE/PES Winter Meeting, Paper No. 94 WM 096-8 PWRD, 1994.
4 Z. Jia and S. Fang, “Development of RTV Silicone Coatings in China”, IEEE Electr. Insul. Mag., Vol. 24, No. 2, pp.28-41, 2008.
[5] E. A. Cherney and R. S. Gorur, “RTV silicone rubber coatings for outdoor insulators”, IEEE Trans. Dielectr. Electr. Insul., Vol. 6, no. 5, pp.605–611, 1999.
[6] CIGRE Taskforce 33.04.01, Polluted insulators: A review of current knowledge, CIGRE brochure No 158, 2000.
[7] IEC/TS 60815, Selection and dimensioning of high-voltage insulators intended for use in polluted conditions, 2008
[8] CIGRE WG C4.303, Outdoor insulation in polluted conditions: Guidelines for selection and dimensioning Part 1: General principles and the a.c. case, CIGRE Technical Brochure No 361, 2008.
[9] K. Siderakis, D. Pylarinos, E. Thalassinakis, E. Pyrgioti, I. Vitellas, “Pollution maintenance techniques in coastal high voltage installations”, Eng. Technol. Appl. Sci. Res, Vol. 1, No. 1, pp. 1-7, February 2011
[10] IEEE Guide for the Application, Maintenance, and Evaluation of Room Temperature Vulcanizing (RTV) Silicone Rubber Coatings for Outdoor Ceramic Insulators, IEEE Standard 1523, 2002.
[11] T. G. Gustavsson and S. M. Gubanski, “Aging of Silicone Rubber under ac or dc Voltages in a Coastal Environment”, IEEE Trans. Dielectr. Electr. Insul.,Vol. 8, pp. 1029-1039, 2001.
[12] R.E. Carberry and H. M. Schneider, “Evaluation of RTV Coating for Insulators Subjected to Coastal Contaminant”, IEEE Trans. Power Delivery, Vol. 4, pp, 577-585, 1989.
[13] R. G. Houigateand and D. A. Swiit, “Composite Rod lnsulators for ac Transmission lines: Electrical Performance of Various Designs at a Coastal Testing Station”, IEEE Trans. Power Delivery, Vol. 5, pp, 1944 -1955, 1990.
[14] S. Kumagai and N. Yoshimura, “Influence of Single and Multiple Environmental Stresses on Tracking and Erosion of RTV Silicone Rubber “, IEEE Trans. Dielectr. Electr. Insul., Vol. 6, No. 2, pp. 211-225, 1999.
[15] S. Kumagai and S. Yoshimura, “Hydrophobicity Transfer of RTV Silicone Rubber aged in Single and Multiple Environmental Stresses and the Behavior of LMW Silicone Fluid”, IEEE Trans. Power Delivery, Vol. 18, pp. 506-516, 2003.
[16] H. F. Gao, Z. D. Jia, Z. C. Guan, and K. N. Zhu, “Investigation on field-aged RTV-coated insulators used in heavily contaminated areas,” IEEE Trans. Power Delivery, Vol. 22, pp. 1117–1124, 2007.
[17] J. Chang and R. S. Gorur, “Surface recovery of silicone Rubbers used for outdoor insulation”, IEEE Trans. Dielectr. Electr. Insul., Vol. 1, pp.1039-1046,
1994.
[18] D. A. Rahna and R. D. Garreauda, “A synoptic climatology of the near-surface wind along the west coast of South America”, Int. J. Climatol., vol. 34, no. 3. Pp. 780 – 792, 2014.
[19] IEC TS 60815-1:2008 – Selection and dimensioning of high-voltage insulators intended for use in polluted conditions – Part 1: Definitions, information and general principles.
[20] Sediver technical report (PE17-00003.A). “Silicone coated glass insulators (FS160PR) returned from ISA PERU: Line 500kV Chilca – Carabayllo”, 2017.
[21] Norma Técnica de Calidad de los Servicios Eléctricos. DECRETO SUPREMO Nº 020-97-EM, Perú.