While external design is essential to how reliably a surge arrester performs in service, its electrical characteristics depend largely on the properties of the internal metal oxide resistors. These ceramic disks are sophisticated electronic devices manufactured using complex technologies and, despite the important role they play, their key properties are not always well understood by those who specify arresters. Yet, much of the performance of an arrester is dictated by the disks. If they fail, so too will the arrester.
The following article from a past contribution by industry expert, Roger Perkins, while dated, offered a valuable review of some of the main elements when it comes to the design and production of MOV disks.
Introduction
MOV disks (the common terminology for zinc oxide varistors) were invented during the late 1960s by engineers in Japan. One can say that their development was mostly fortuitous since they were the unintended by-product of an attempt to create semiconductor metal surface barriers using polycrystalline zinc oxide and silver electrodes. The disks were later adapted for use in HV surge arresters by several companies, notably General Electric, which conducted some of the landmark research to understand their behaviour.
The ’varistor effect’ is actually not a bulk effect but rather a grain boundary phenomenon associated with polycrystalline, semi-conducting ceramic materials. While many models have been developed to explain it, perhaps the most successful has been the Double Schottky Barrier (DSB) model. The huge influence on current flow of very small changes in voltage – the inverse of which represents the primary characteristic of an arrester – is due to a process called impact ionization.
Optimization of Composition
The modern varistor block contains predominantly ZnO but also between a few percent and a few parts per million of at least 10 additional elements, each of which has been determined through experience to contribute to performance. Some of these dopants, which include elements such as bismuth and manganese, affect discharge voltage while others play a role in power loss, ageing behavior, energy absorption and so on.
For the development engineer in this field, the key challenge is to determine the optimal number, type and composition of these various elements. The task is not easy since the effect of one is not independent of the others and significant, often non-linear, interactions have to be considered. Moreover, there is not only a single varistor property to optimize but typically several, each of which will influence arrester performance.
Statistical techniques to cope with this problem have been developed and these enable production engineers to come up with an optimal formulation for their particular material system as well as the ideal related manufacturing process. Nonetheless, it is important to note that not all MOV discs offered in the marketplace and used in the production of surge arresters have the same optimal properties as well as varistor characteristics. Some of the reasons for this are discussed below.
Role of Microstructure
Optimal formulation does not in itself guarantee a good MOV disk. While formulation might assure intrinsically good electrical properties, there are other performance characteristics that depend more on production process than on material composition. This is because manufacturing involves ceramic technology and the essence of a ceramic material lies in its microstructure. The key properties of all ceramics – and this also applies to MOV blocks – are determined by their microstructure.
Fig. 1 illustrates a typical varistor microstructure. To the untrained eye, it may not appear homogeneous, especially if one considers that: 1) grain boundaries are so important, 2) that the content of critical elements is measured in parts per million and 3) that current densities can exceed 90A/mm2 in arrester applications. Nevertheless, this device offers exceptional performance in spite of these constraints.
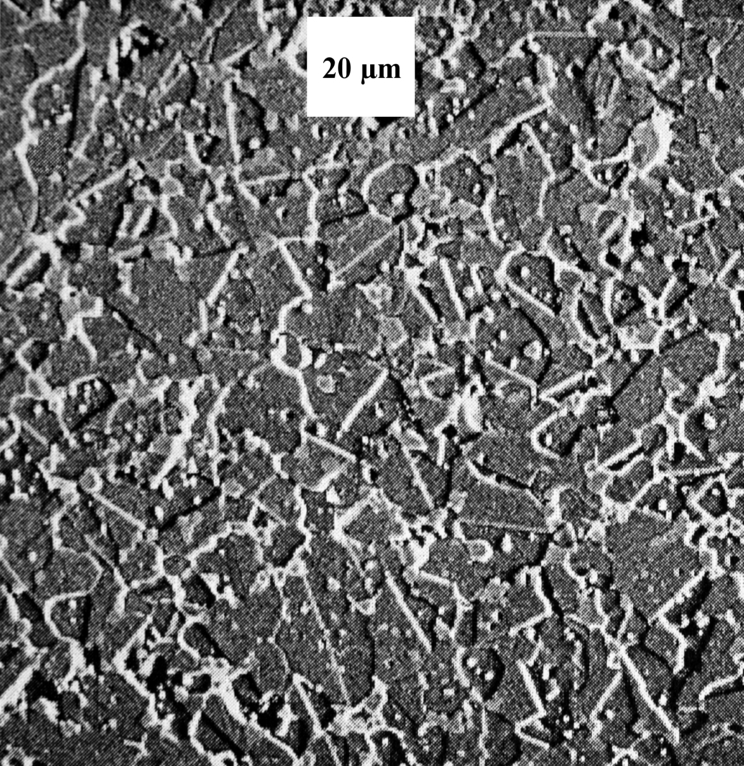
The area of the microstructure shown in Fig. 1 is only 0.02 mm2 and contains only 50 grains of ZnO. A key concern is that this same uniformity must persist over a volume of perhaps 105 mm3 as well as the huge quantity (300×106) of grains one finds in a typical MOV disk.
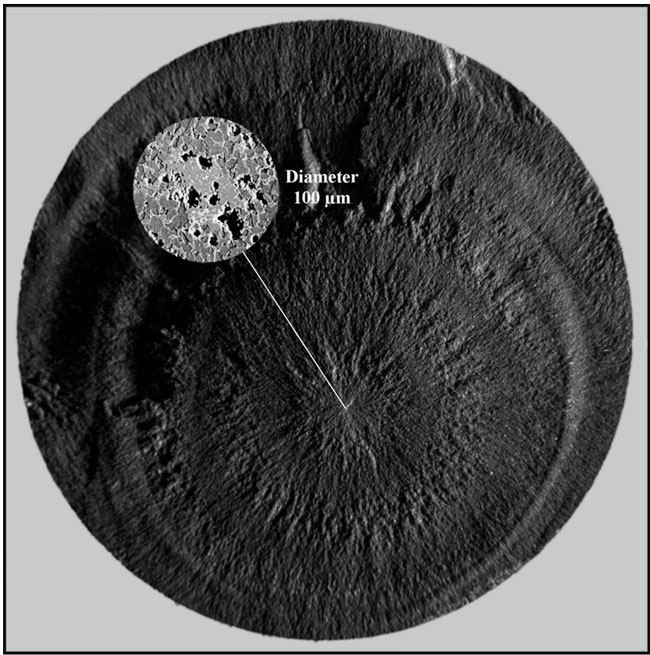
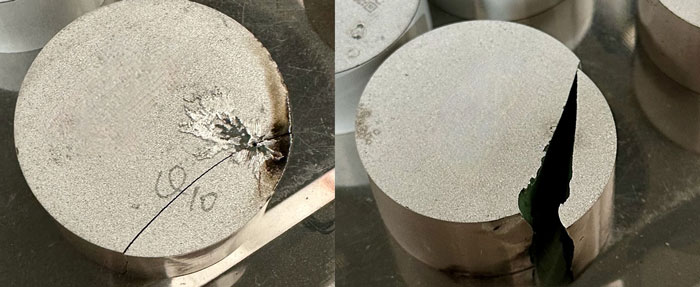
Fig. 2a shows a problem that can occur if the microstructure of a disc is not well-designed and controlled and in this case the defect resulted in failure under severe operating conditions. Ceramics tend to exhibit brittle fracture so that, if localized stress exceeds tensile strength, a crack will be initiated and expand catastrophically. Localized stress is influenced by defects, which, depending on their size and geometry, can magnify the impact of an externally applied stress.
For example, a high current discharge through an arrester (such as from a 100 kA lightning impulse) subjects the MOV disk to heating rates of as high as 2.5×107 °C per second. Resulting thermal expansion generates inertial stress waves within the material whose magntiude depends on the MOV’s physical dimensions as well as the rate of heating. Longer disks generate higher internal tensile stresses than shorter discs and, should the material contain any microstructural defects (e.g. of the type in Fig. 2), these stresses will lead to fracture. For a symmetrically constrained disk, reflections of the stress wave will maximize tensile stress at the center and a characteristic mid-plane crack will form. Clearly, the manufacturing process must avoid such defects if an MOV disk is to successfully withstand current impulses of this magnitude.
In addition to the above mechanical effects, a non-uniform current distribution through the MOV disk can lead to electrical failure. The current path is usually not uniform due to statistical variations in grain boundary properties coupled with the strongly non-linear conduction mechanism. Should the microstructure not be highly homogeneous, this effect is magnified and current paths can be formed which, due to the positive temperature coefficient of semiconducting materials, can lead to thermal instability and failure. Microstructural homogeneity is therefore essential and the manufacturing process must aim to always achieve it.
Role of External Coatings
Although material formulation and microstructure are clearly significant, these characteristics are not the only ones which must be carefully controlled when manufacturing MOV disks. The externally visible electrodes and circumferential coating (or collar) also play important roles in ensuring good performance.
A. Metallized Electrodes
1. Mechanical Preparation
Prior to metallization of an MOV disk, it is essential that precise geometrical conditions are fulfilled, namely that the surfaces are completely flat, plane-parallel and perpendicular to the rotational axis of the disk. If this is not the case, a range of subtle problems can result. For example, adjoining electrode surfaces may not make uniform contact meaning that current injection into the metallization will also not be uniform. Potential differences will result which, under high current impulses, can lead to electrical breakdown of the tiny air gaps and to unnecessary erosion in the contact surface.
The mechanical construction of the arrester itself, whether polymer or porcelain-housed, will also be sensitive to any deformities in shape of disks. Undesirable pressure points can generate fractures, while air gaps can lead to partial discharges and dielectric breakdown of the housing. The most effective way to avoid such deficiencies is through carefully controlling the grinding operation which precedes metallization.
2. Metallization
The function of electrodes is to uniformly distribute the high currents that can flow through an arrester’s MOV disks during a nearby lightning strike and ensure a uniform current density across the varistor surface. Inability to achieve this will result in non-uniform heating, current channeling and hot-spot formation – all potentially resulting in failure.
The most important property of the electrode is the degree to which it covers the surface of the disk. Traditionally, metallization has been of aluminum and applied using an arc or flame-spraying manufacturing process. A circular mask with diameter a few millimeters smaller than the disk is placed in contact with its surface using a methodology called border-metallization. However, there can be serious deficiencies in this technique. For example, the tolerance between mask and disk sizes and in the accuracy of positioning can lead to an electrode border having a non-uniform width. Moreover, the difficulty in cleaning the mask can lead to uneven edges. In addition, the high spray-pressure and inevitable gaps between mask and disk surface allow some metal to leak through and to coat surfaces which should not be coated, such as the border and collar. Each of these problems could lead to non-uniform current or electric field distribution and the typical resulting failure mode will be puncture (see Fig. 3).
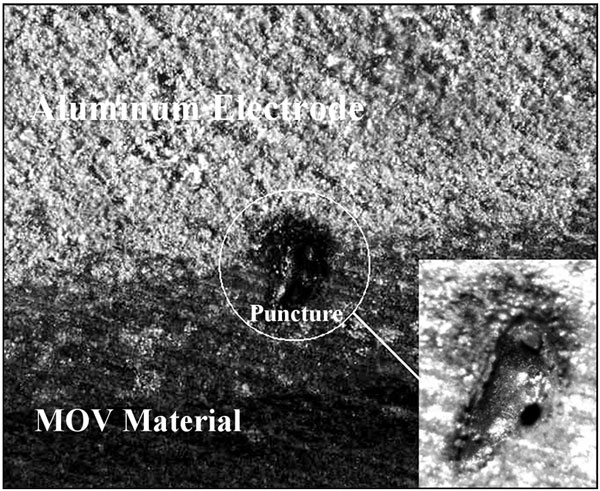
In contrast to the above failure modes, which occur only within a single MOV disk, a further potential failure is linked with inter-disk contact in the presence of border-metallization. In this case, the air gap generated at the edge of and between disks leads to high electric fields in the region, which in turn can lead to dielectric breakdown. An arc initiated here will generally strike the bare disk surface and inevitably generate a hot-spot that also leads to current channeling and puncture.
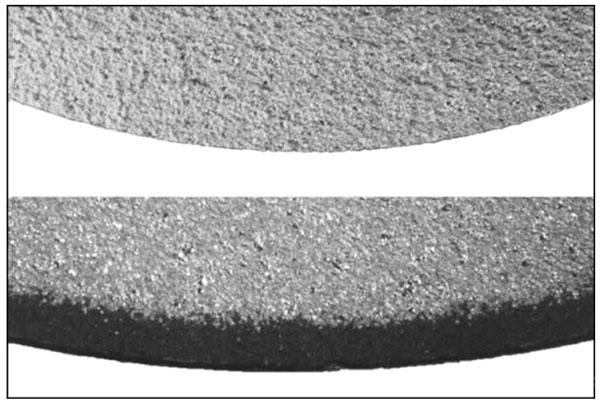
An effective way to avoid these types of metallization defects is to use full-face metallization (as in Fig. 4). With this technique, the edge of the disk forms one part of the mask while the other part is semi-circular and does not make contact with the disk. This arrangement is less sensitive to the problems described above. In addition, the complete volume of the disk is utilized and the current distribution is uniform all the way out to its edges. Other methods such as high-resistive coatings and flexible masks have also been devised to circumvent the potential problems described but each also has some deficiencies.
B. Collaring
As with metallization, the simplicity of the circumferential disk coating (or collar) can be deceptive. Traditionally, polymeric coatings have been used because they are easy to apply. However, their performance is not always optimal since thermal degradation and poor adhesion to the disk surface can concern the arrester manufacturer. As the performance of arresters continues to improve, the maximum temperature excursions they experience in service also increase. A polymeric coating can soon become the weakest link.
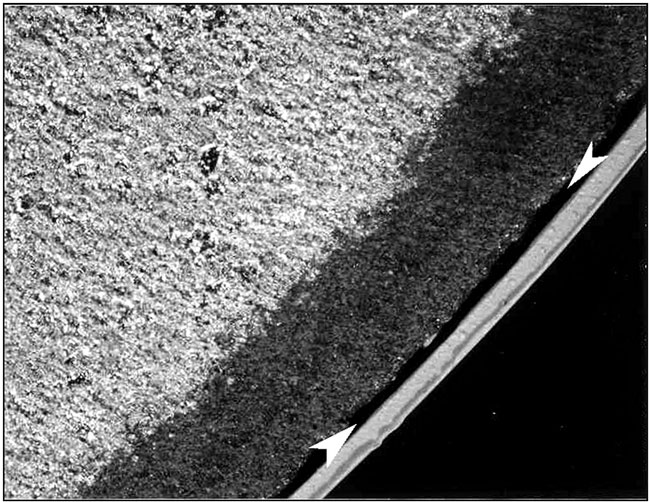
For example, under poorly-controlled manufacturing conditions, adhesion between the coating and the disk can be inadequate (as in Fig. 5). The disk surface will then be exposed and start to degrade. Moreover, in the case of porcelain-housed arresters, transverse fields caused by severe external pollution could lead to internal partial discharges which can degrade some polymeric coatings (see Fig. 6) and cause formation of corrosive gases. Polymeric coatings have proven themselves less effective than glass coatings in preventing attack on the disk surface from such effects. The ZnO varistor effect is strongly influenced by oxygen concentration at the grain boundaries of the DSB. Consequently, it is sensitive to localized changes in the partial pressure of oxygen, which can lead to rapid ageing of a disk and eventual arrester failure.
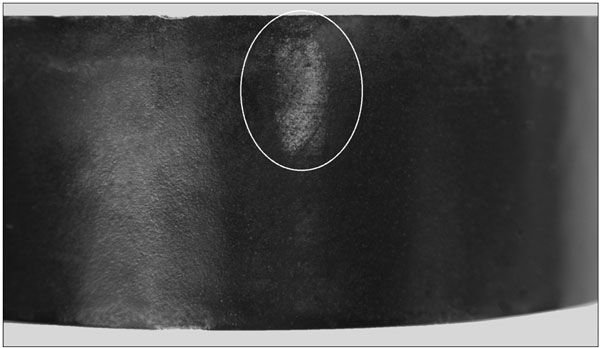
It is important to remember that a varistor is a semiconductor whose electronic junctions at naked surfaces require correct electronic grading in order to prevent degradation or elevated surface leakage currents. The use of glass instead of polymeric coatings achieves this more effectively and prevents deficiencies. Glass will not degrade thermally and exhibits such low diffusion coefficients as to hermetically seal the varistor surface from all external chemical influences.
However, glass coatings must be chosen carefully in order to fulfill this requirement as well as to be chemically compatible with the disk material i.e. not react with it at elevated application temperatures. Additionally, the glass should not contain hazardous components, such as lead, which will cause concern both in manufacture and in future disposal.
Quality Control & Test Procedures
It is evident that each step in the manufacturing process for MOV disks exhibits its own potential challenges if all required performance criteria are to be fulfilled. An integrated testing philosophy is therefore important.
Statistical Process Control
It is very the nature of an MOV disk that its properties cannot be adequately checked until the manufacturing process is complete. An alternative approach is to apply statistical process control to each step in the production process.
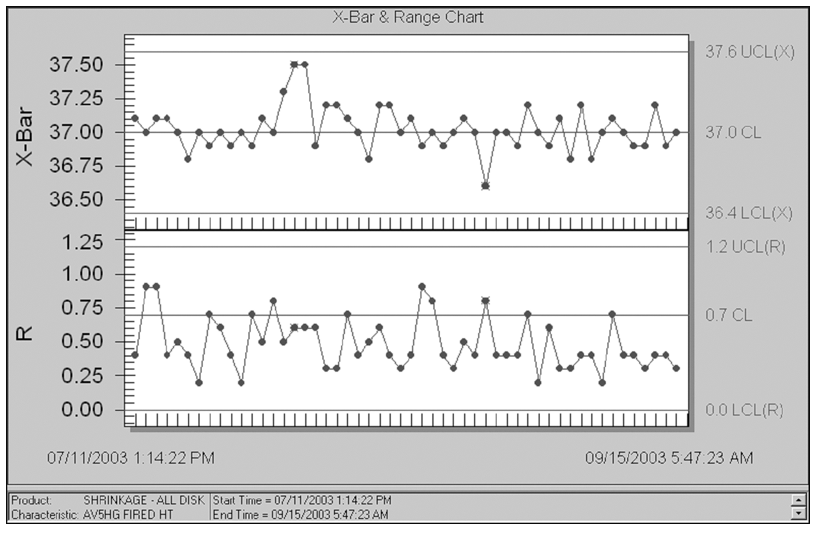
In some cases the control parameter is obvious e.g. flatness, weight. In other cases, the intent is to identify and control those production parameters (Fig. 7) that are known to influence disk performance, e.g. temperature, cooling rate, atmosphere, pressure.
Final Testing
In spite of effective process control, it is still necessary to conduct extensive testing of MOV disks at the conclusion of the manufacturing process. The goal is to:
1. control those material parameters that impact performance in service;
2. confirm the protective characteristic;
3. ensure that design parameters are not exceeded, and
4. confirm long term behaviour.
The following Table offers an overview of tests that are normally carried out on MOV disks and explains how they relate to subsequent arrester performance. Type tests are not included in this overview but are specified in detail within the relevant IEC and IEEE standards. While these documents specify minimal routine tests, it is still necessary that the disk manufacturer extend this list significantly so as to be certain of satisfactory performance.
At the same time, it is important to stress that arrester performance is determined not only by the MOV disk but also by its basic construction. For this reason, routine disk testing is by nature generic since it focuses only on basic performance characteristics. Arresters are designed around the disk and not the reverse. Therefore, safe arrester performance cannot be guaranteed by successful routine disk testing alone.
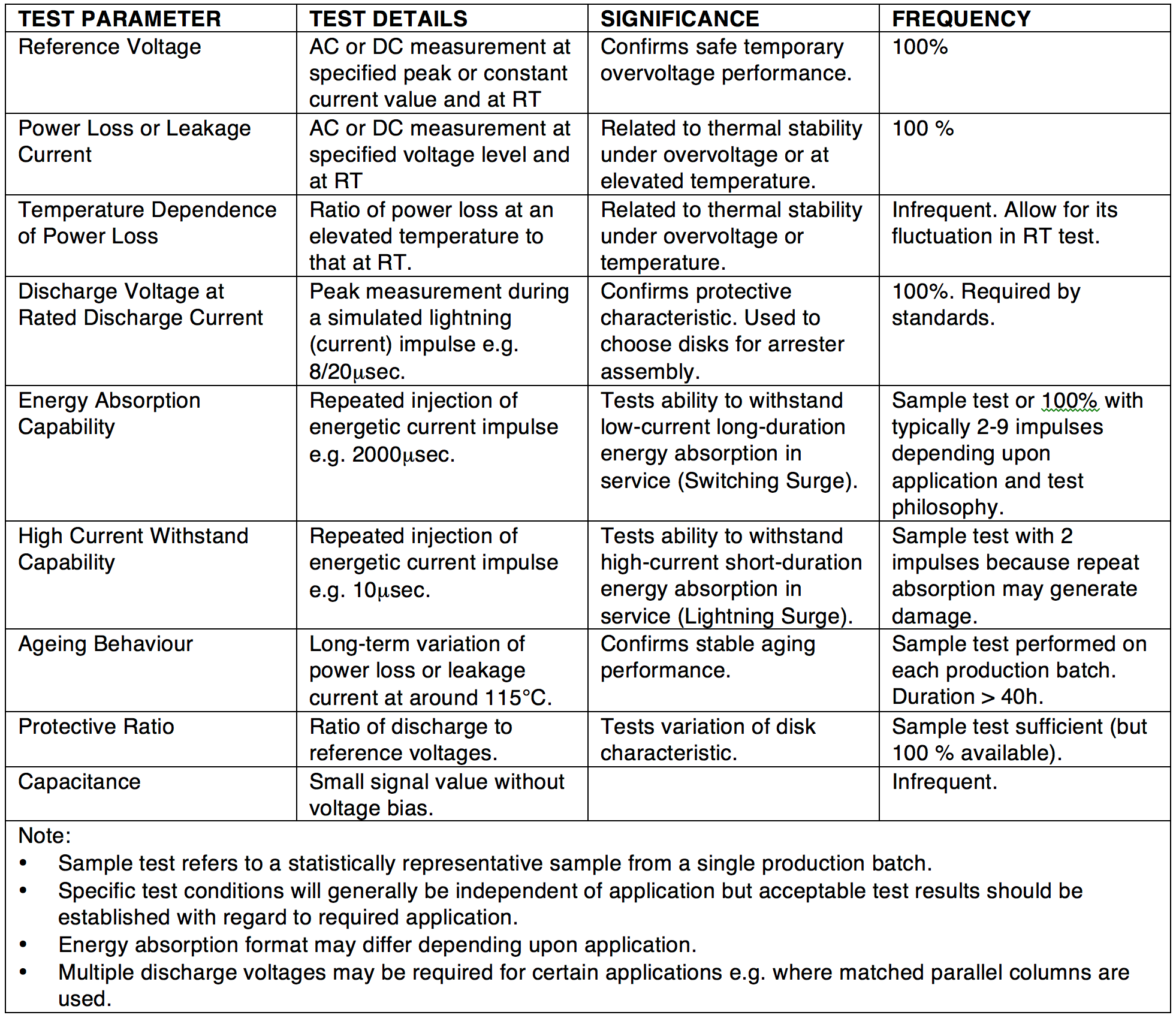