This edited past contribution to INMR by KEMA Labs discusses how testing can help reduce risk of catastrophic failure of a power transformer.
Failure of a large power transformer is a nightmare scenario for any transmission system operator due to the enormous possible repercussions. The initial outage, if in a major urban centre, can cost tens of millions – per hour. And that does not even begin to account for the hardships faced by customers, potential liability issues or long-term damage to the energy supplier’s image.
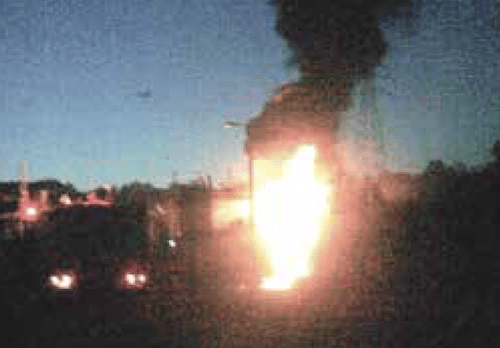
What is more, if large transformers fail, they often do so in frightening fashion. For example, according to a study by CIGRE Working Group A2.37, more than one in every 8 large transformer failures result in fire or explosion, putting public safety at risk. Such events therefore attract much negative publicity. Then comes the cost and effort to replace the failed component. Transformers of such size typically cost millions and are often custom-designed and built to order. Lead times for replacements can be up to 24 months during which the power system must continue to operate reliably but now with one less transformer.
While the standard N-1 approach to network design means that a reduced power mode is possible, the system will operate less effectively and with elevated risk. Not only are the remaining components under greater stress, another failure might take down the grid. Clearly, whatever is possible must be done to mitigate risk of large transformer failure. Yet the numbers of failures remain high. Reports of failures that make headlines in the U.S. alone occur about once each week while CIGRE has estimated that the overall global rate is around one major failure per 200 transformers per year. The rate and consequences of failures place large power transformers among the top types of equipment covered by insurance claims and underwriting investment for them is a growing challenge. Can the industry reduce the rate and impact of large transformer failures?
The two most common causes of failure, according to CIGRE, are ageing and external short circuits, with each accounting for some 12% of failures. While ageing is best tackled through proper asset management, ensuring that a transformer can withstand an external short circuit is mostly a matter of quality assurance. There are essentially two basic ways to verify a transformer’s short circuit withstand capabilities: design review and physical testing. The first uses calculations based on design parameters to estimate how a transformer will behave during a short circuit situation. The second involves exposing the transformer to the conditions it would face during a real-life short circuit and measuring response. Both techniques have their place. Design review is invaluable in the design phase, helping ensure the transformer meets general requirements. But it can struggle to give sufficient verification of performance during fault conditions. There are a number of explanations for this, including over-simplification of a complex and highly dynamic situation within the transformer, reviewing an incomplete list of sub-components and the inability to cover material or production faults.
Full power short-circuit testing, by contrast, looks at the actual, complete transformer under realistic fault conditions. This yields more accurate verification of the transformer’s quality and is borne out by reviewing test results, such as those carried out at testing laboratories. For example, testing at a major laboratory over a 20-year period and covering some 300 short-circuit withstand tests on power transformers found initial failure rates of around 23%. All these transformers were designed using methods similar to those used in design review. It is noteworthy that among those transformers that failed initially, the pass rate in re-testing after modification by the manufacturer was close to 100%. That means full power physical testing helped manufacturers improve quality of their transformers. Testing is also a vital learning phase for manufacturers by allowing lessons from one failure to be applied to improve product quality.
Indeed, data from across the globe show that short-circuit related failures fall after introduction of short-circuit testing. For example, the advent of short-circuit testing in China during the mid-1990s led to a reversal of what had been a rising trend of short circuit failures. Similarly, while the U.S. was reporting that short circuits accounted for from 50 to 85% of transformer failures during the 1960s, this figure subsequently dropped to 20%. Key to the value of short circuit withstand testing is the ability to test full-scale transformers under the fault conditions actually faced in service. With the dawn of super-grids and as transmission voltages continue to increase, the need for testing facilities that deliver more power and higher voltages will only grow.
[inline_ad_block]