Arresters for application at 52 kV and higher have experienced the same fundamental shifts in technologies as distribution arresters but at a slower pace. In the 10 year period between 1986 and 1996, the distribution arrester market converted almost entirely away from porcelain. However, since their first appearance in the early 1990s, polymeric-housed designs have succeeded in capturing only a share of the total HV arrester business, alhough this is growing rapidly. The different rate of market acceptance has been due to several factors. Unlike the case for porcelain-housed distribution arresters, porcelain designs for station applications have had a good service record. At the same time, users perceive much greater risk in adopting new designs and materials in applications such as station arresters where any failure can severely affect the network. These arresters are protecting major assets and therefore it is critical that they perform properly for periods of up to 25 or 30 years, depending on service conditions. Moreover, while for MV arresters the primary application is line and lightning protection, in the case of HV arresters, lightning is a smaller part of the requirements. Instead, the primary application is dealing with switching and low amplitude surges. Demand for reliability and integrity are key since the arrester is protecting expensive equipment such as high capacity power transformers. Failure of any sort will interrupt a lot more power transfer.
Nevertheless, in spite of the cautious market reception of this technology, suppliers in the HV arrester industry have continued to develop and promote polymeric design alternatives. Indeed, it seems most are convinced that these designs represent the future for this category – just as polymeric MOV arresters became the standard for distribution applications. The latest arrester designs and housings have also opened up a new area of application, namely on transmission lines. While the major proportion of HV arresters have so far been installed at stations, continued emphasis on high reliability will support growing application on overhead networks as well.
Market Factors & Structure
Due to the impact of major HVDC projects on sales of metal oxide devices, there is large variation in annual demand for HV arresters – estimated as high as US$ 300 million. However, this project driven business is accessible only to industry giants awarded design and procurement responsibility. Similarly, not every manufacturer supplies arresters to the highest system voltages, meaning that for some competitors, the realizable 2 From an industry survey presented in INMR No. 57. business is smaller. Finally, large markets such as China and India are seen as closed to external competitors and are not considered available to be supplied by the world industry at large. Still, however one estimates the size of this business, the market is likely smaller than for distribution arresters. While unit prices are much higher, volumes are significantly lower with orders tied in with expansion of networks and construction or upgrading of substations. Due to the higher technical requirements in designing, manufacturing and certifying HV arresters, the field of competitors is also much smaller than for distribution arresters. Barriers to entry into this segment include complex technical issues that do not exist in MV systems and producing and qualifying HV arresters is a more expensive undertaking. For example, there are stringent acceptance and routine tests for HV arresters, often witnessed by the customer. There is also far greater emphasis on performance compared to distribution, where if an arrester breaks down it is simply replaced. This greater required expertise and credibility acts as a barrier to entry by new suppliers, especially as voltage levels rise. Customers for these arresters cannot accept failure and tend to buy only from established manufacturers with the proper manufacturing and testing facilities. Given the above, industry concentration in the HV arrester business is high and several leading suppliers together account for over two-thirds of the global business.
The HV arrester business is aimed at two major applications: substations and transmission lines. The former is by far the larger and use of such arresters directly on lines is a relatively small but growing proportion of the business. Still, the field of line arresters has been opened up with introduction of lightweight polymeric materials in the place of porcelain. As more customers employ sensitive equipment that cannot stand even small disruptions, installing arresters at proper locations along a critical line can eliminate this concern.
Metal Oxide Varistors
Application of zinc oxide varistors to HV arresters began at the end of the 1970s. Within a few years, most major suppliers had changed over completely and gap type technology was rendered obsolete. The major difference in the metal oxide blocks used in these arresters versus for distribution applications is in dimension. Blocks for station arresters typically range in diameter from 48 mm to 99 mm, depending on line discharge class and generally in discrete intermediate sizes. Another important characteristic is thickness since the voltage applied by the system will eventually be distributed across the blocks. This factor is distinct from diameter although, clearly, energy of the surge will be better absorbed if blocks are also larger in diameter and have greater mass. Key performance factors for blocks are protective level, power losses and energy withstand capability. Moreover, due to the consequences in HV applications, failure rate must be kept extremely low. Dimension is not the only difference between blocks used at MV and those for use in HV arresters. Depending on supplier, there may also be slight variations in formulation, which generally consists of about 95 per cent zinc oxide, 4 per cent bismuth oxide and about 1 per cent dopants such as chromium, iron or tantalum to achieve the desired semi-conductor effect. Other ingredients are also added to facilitate manufacturing. Apart from such minor changes in formulation, there are also differences in firing process since larger pieces require greater care in how the temperature is brought up and then lowered. The final discs shrink by up to 20 per cent or more. Working with larger pieces therefore means greater total change in diameter and requires constant process monitoring and control. These blocks are also tested stringently since any minor defects are far more costly in this application.
One of the interesting developments in zinc oxide block technology relates to availability of blocks that have a higher gradient across them. Normally, arresters for open air applications have a residual voltage of 300 V/mm across the blocks. This is adequate since length of arrester column in such applications is determined by creepage distance requirements of the housing. For specialized applications such as GIS, however, where keeping the MOV column as short as possible is desired, blocks have been developed that offer 600 V/mm. Still, high gradient blocks account for only a minor share of the business since the large majority of the arrester business is dominated by open air applications.
Acceptance of Polymeric Housings
The rapid and complete transition from porcelain to polymeric housings in distribution arresters was an exceptional event for the power industry. What drove this transition forward so quickly was the universal unsatisfactory performance of porcelain-housed designs that were subject to problems of moisture ingress and dangerous explosive shattering. In the case of arresters for HV station applications, however, this has not been the case since these have been designed to handle internal failure without catastrophic consequences. The porcelain in these units has the integrity to withstand internal faults and, given the pressure relief mechanisms, any criticism of such station arresters for exploding and causing damage to surrounding equipment is probably unfounded. Rather, whenever there have been such cases, they have likely been due to misapplication. For example, explosive failure of porcelain HV arresters has been known to occur when a network is upgraded without replacing pre-existing arresters. Whenever there is such an upgrade at a station, it is important to review the pressure relief behaviour of existing arresters for any increase in short circuit rating. While pressure relief ratings of most porcelain station arresters have more than doubled in recent years, older models may not be designed to deal with available fault current at a station after an upgrade.
In fact, the excellent pressure relief behaviour of porcelain- housed arresters has been a key factor delaying acceptance of certain designs of polymeric HV arresters. Porcelain HV arresters offer directional venting of exhaust gases from the inside so as not to damage insulation anywhere else in the station. Certain polymeric designs, however, can open up at any point through the housing wall, meaning one cannot be certain where ejected gases may be directed. Much depends on how the arresters are installed. If they are mounted directly on the transformer, for example, it would not be desirable for an arc transferred from inside the arrester to play on the bushing. Directional venting should ensure the arc is always directed away from the bushings. In this regard, it can be stated that a well-designed and properly tested HV arrester is safe, whether polymeric or porcelain-housed. Badly designed porcelain and polymeric arresters are both dangerous.
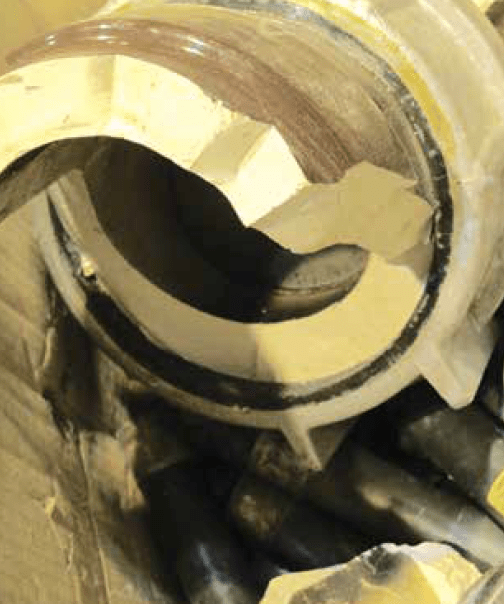
CLICK TO ENLARGE
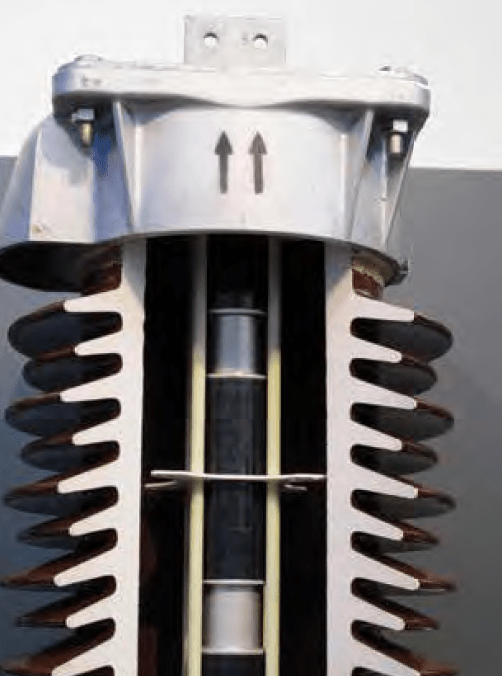
CLICK TO ENLARGE
Another factor that has slowed acceptance of polymeric HV arresters is concern about long-term behaviour of their external housing materials. Porcelain is inert and, if not exposed to vandalism, has long life. By contrast, there are lingering doubts about the service life of polymers. One of the reasons that changeover to polymers has been slower in HV arresters is that customers want to be certain that the arrester does not fail due only to a problem with the housings. Another issue is cantilever strength, which has made some utilities reluctant to move away from porcelain-housed HV arresters. Indeed, some utilities perceive the need for the arrester to bear loads and the cantilever strength of some polymeric arrester designs is not what they want. But should a porcelain-housed arrester fail, while it may not explode, it certainly could crumble and collapse – just as might a polymeric design.
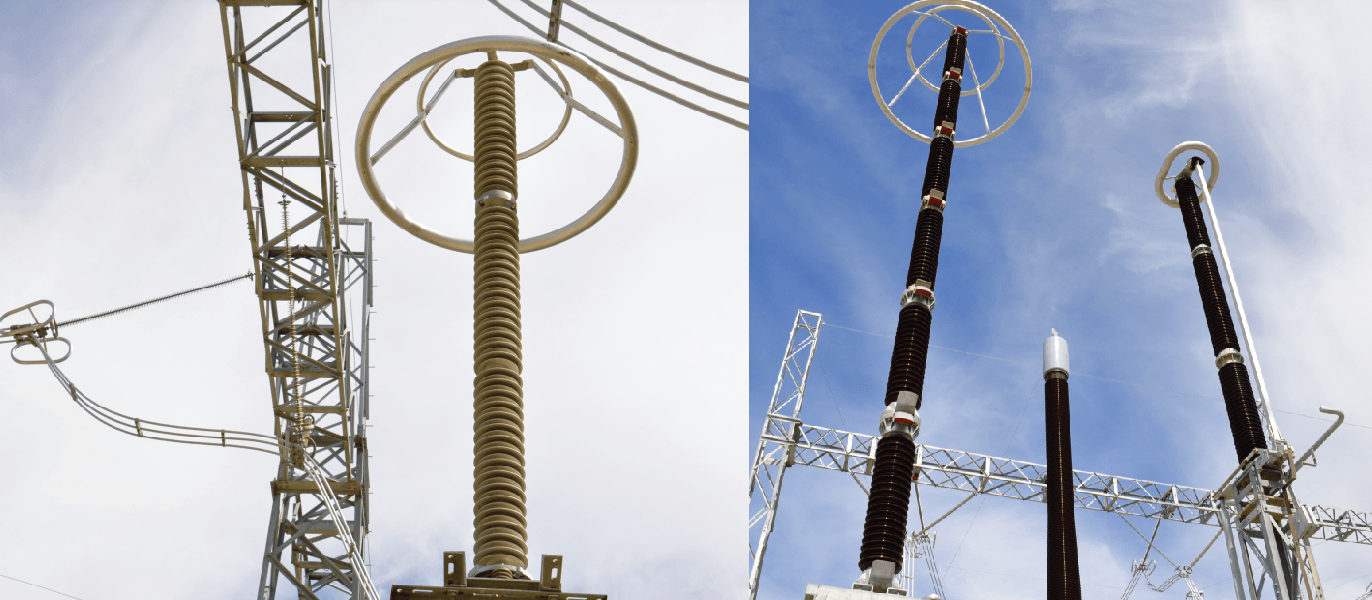
CLICK TO ENLARGE
Given the above considerations, it is not surprising that the penetration rate of polymeric HV arresters has initially been comparatively low – industry sources estimate between 30 and 40 per cent in value terms. Notwithstanding this lower level of penetration, most manufacturers supplying HV arresters expect that polymeric designs will eventually dominate this category and evidence from recent years seems to back this up. Indeed, some industry leaders have chosen to move aggressively into polymeric-housed designs and point out that their acceptance has been growing more quickly than statistics indicate. This is because there are critical voltage levels above which factors promoting conservatism have greatest impact on decision-making. In this regard there has been a stepwise change in penetration by voltage class: at lower transmission voltages polymeric arresters have high acceptance while at the upper range it is still comparatively low. This may indicate that the utility industry has gradually been adopting HV polymeric arresters but in a systematic process. Positive field experience at lower transmission voltages encourages greater acceptance at higher voltages. Conservatism toward polymeric HV arresters by utility customers is often closely related to the extent to which they have accepted other polymeric-housed equipment (e.g. breakers, bushings, CTs). The inverse is also true. Polymeric surge arresters promote acceptance of more such equipment housings at substations.
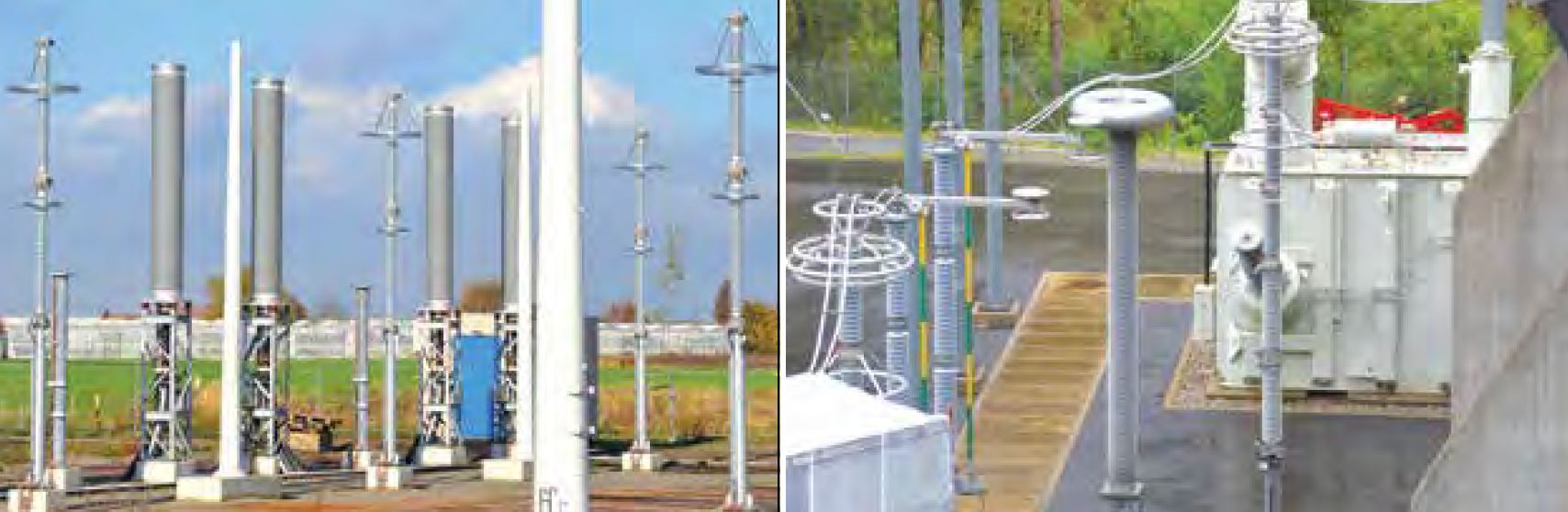
CLICK TO ENLARGE
The main drivers propelling transition to polymers for HV arresters include cost pressures, since customers expect to buy polymeric-housed designs at a lower price than porcelain. Some have even come to view the porcelain housing as too costly an ‘envelope’ for the internal active elements, which is where an arrester’s real value lies. Moreover, customers have come to believe that polymeric arresters are safer – even if this may not be true – while in regard to pollution performance, these arresters are perceived to offer significant advantage.
Polymeric Materials for HV Arresters
Today, the large majority of designs of polymeric HV arresters utilize silicone rubber as the housing material. Since customers for HV arresters tend to be cautious, they prefer silicone to ensure the best performance under pollution. But to better appreciate the value of employing a silicone housing for MOV station arresters with the goal of improving pollution performance, it is useful to look back at performance of gap type arrester designs where electrical activity on the external housing caused individual gaps to spark over. When enough of these had sparked over, the remaining gaps could no longer hold the system voltage and this pattern eventually thermally destroyed the arrester. But MOV type arresters are said to be intrinsically immune to pollution-induced failures. With these arresters, electrical activity outside the arrester is dissipated in the blocks. The amount of energy which is coupled in is small and cannot cause the blocks to fail thermally. At the same time, prolonged corona can degrade insulation, including the insulating collar and this may cause an arrester to eventually fail. However, a properly designed zinc oxide arrester should not suffer from this problem. While an arrester has to perform as an insulator as well, pollution as a cause of internal arrester failure is just not as big an issue with MOV technology.
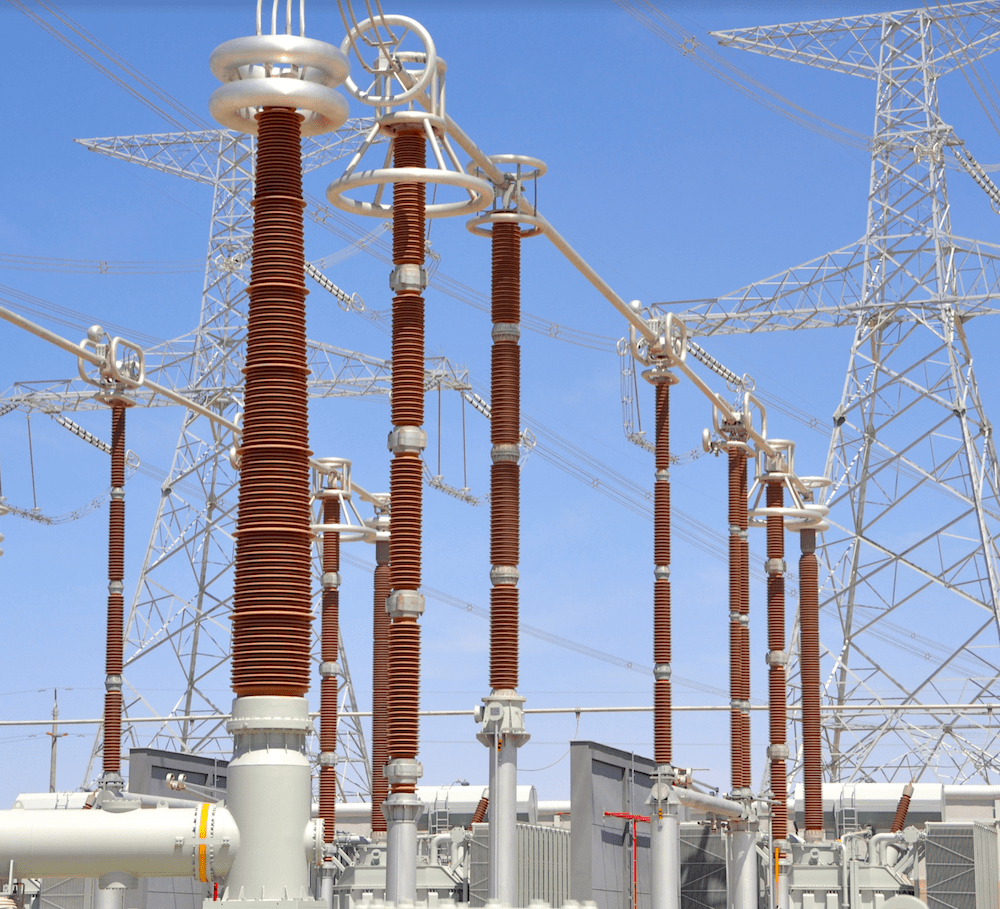
CLICK TO ENLARGE
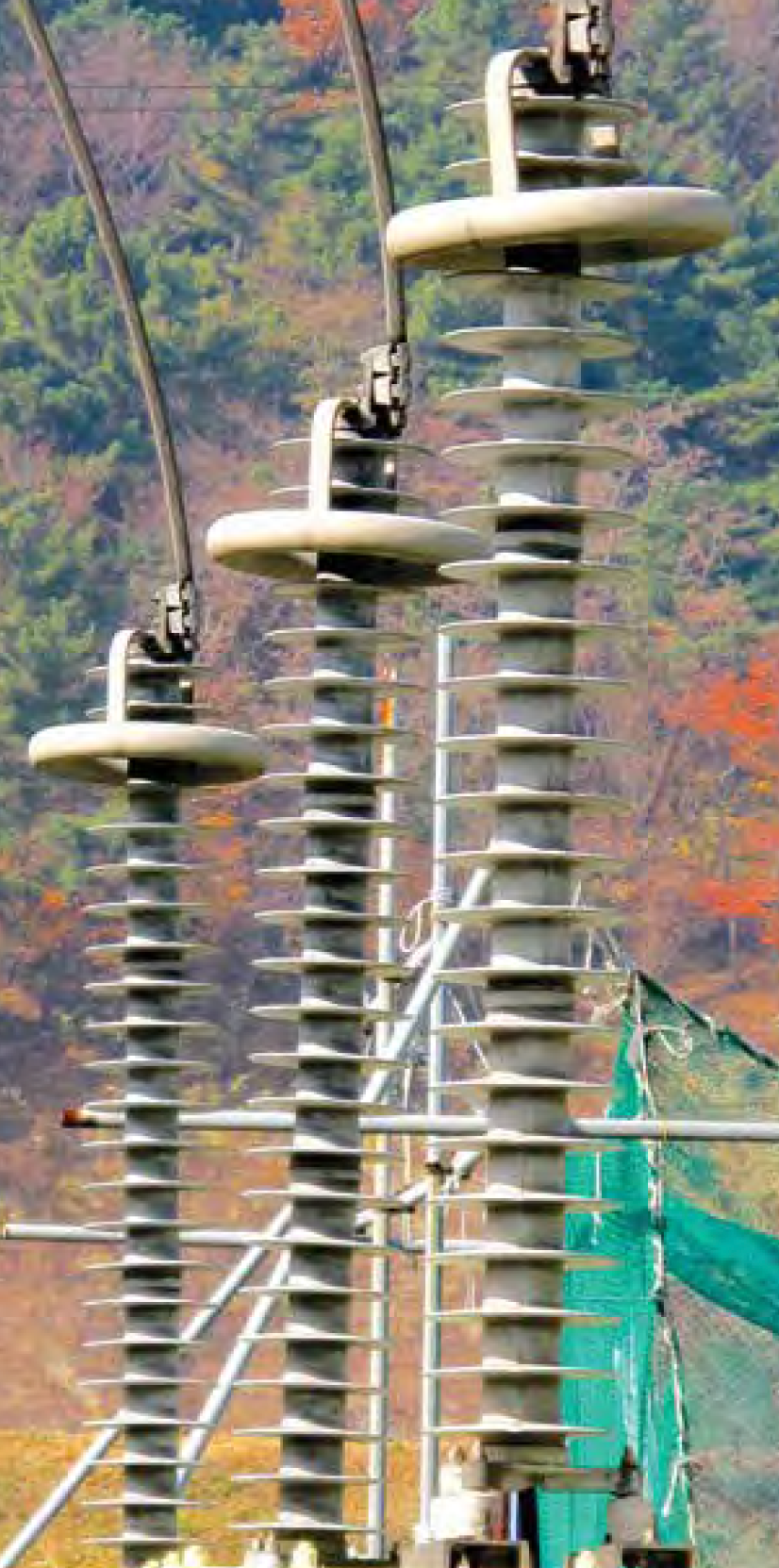
CLICK TO ENLARGE
Another point of view is that a silicone housing offers advantages since pollution performance is more important at higher voltages – particularly given that the arrester is designed in multiple units assembled together. In one scenario, for example, the unit closest to the ground is subject to higher humidity and quicker formation of dew. This leads to higher leakage currents which can then enter into the internal elements of the adjoining module via the flange. This can make the whole arrester thermally unstable and instability of this sort will cause the blocks to become warmer and conduct more current. In the worst case, this can lead to thermal runaway. Others in the industry play down the role of pollution performance as a key driver in the transition toward polymeric designs. While better behaviour in contaminated environments was perhaps the major consideration at the time polymeric housings first became available, other factors such as reduced weight and lower installation costs have since come to take on greater importance in convincing customers to purchase these types of HV arresters.
Design Alternatives in Polymeric HV Arresters
In the gradual movement over the past decade toward employing polymeric housings in HV surge arresters, a number of alternative designs and manufacturing processes have emerged. Basically, these can be classified into one of three principal groups: cage design, wrap design and tube design. The basic concepts behind each are quite similar to those used in manufacturing distribution arresters. Manufacturers supplying these alternative designs have had to review the block containment behaviour of their arresters in light of changes in the IEC short circuit test which now requires that, in the event of failure, no internal parts should be ejected a distance greater than the height of the arrester, i.e. remaining within a 45° angle from the top of the arrester.
Cage Containment of Blocks
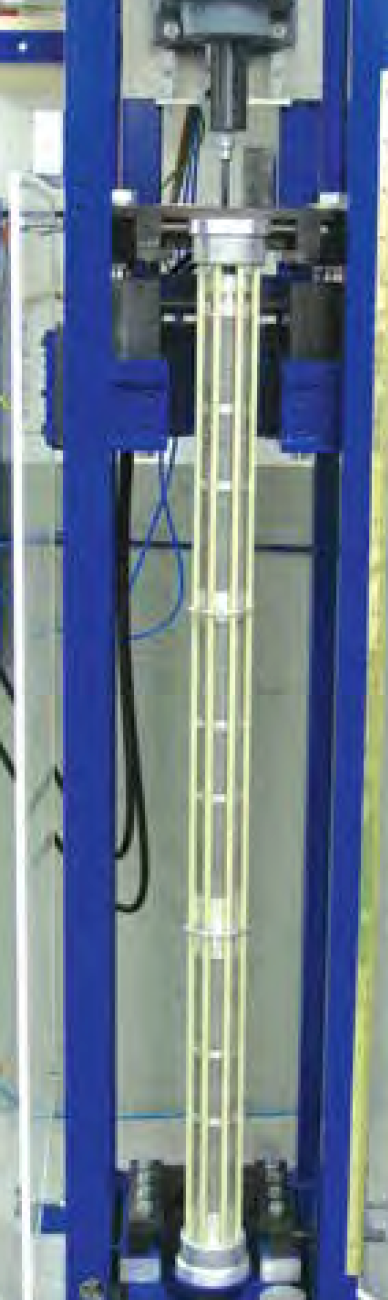
CLICK TO ENLARGE
Some of the leading suppliers of HV polymeric arresters have developed designs that employ a cage consisting of special glass fibres and straps wrapped tightly around or looped over the zinc oxide column. The caged unit is then prepared and primed for the injection step during which the polymeric housing is molded directly onto the cage assembly. Generally, a cage design requires fewer units or modules to build up a HV arrester than a comparable wrap-type design but more than would be necessary with a tube design.
One of the critical variables in this design is that the length of any individual unit is limited by certain physical principles and performance parameters, e.g. the so-called ‘buckling effect’. If a certain critical length is exceeded, there will be no mechanical strength left in the arrester. Basically, this means that the mechanical resistance of a column when exposed to a longitudinal force will collapse above a certain value of the ratio of length to diameter. According to this principle, the maximum length possible of each caged module should be about 1.2 meters. Another limiting variable in length of a cage design is lateral field strength across the polymeric insulation during the salt fog test according to IEC 60099-4. The longer the unit, the higher will be the lateral field strength, until breakdown and puncture of the housing occurs. As a result, it is generally-accepted that arrester designs where insulation is moulded directly onto the metal oxide elements are limited in length to about 1 meter. The cage design is seen by some in the industry as an economic alternative to the tube design, offering a high degree of safety against internal pressure build-up and ejection of large parts from within the arrester. However, while there is no significant pressure build-up, the prestressed fibre rods forming the cage could burn under such circumstances and the arrester will collapse mechanically.
Wrap Design Containment of Blocks
The process of wrapping a column of metal oxide blocks sees a fiberglass cloth impregnated with uncured epoxy resin wound over the blocks in a number of layers and under high tension. The wrapped column is then heated in an oven so that the resin within the tape will cure. There are variants to this process, depending on manufacturer. The external housing is either molded directly over the wrapped column or a slip on technique is used to apply a pre-manufactured polymeric housing over the column. The method by which the wrap is applied determines how good the arrester is since it affects thermal breakdown. For example, if there are any voids created during the wrapping process, partial discharge activity will cause glow discharge and leakage currents. More and more utilities use thermal imaging cameras to look at station arresters and if a rise in temperature is seen, this is interpreted as sign of an incipient problem.
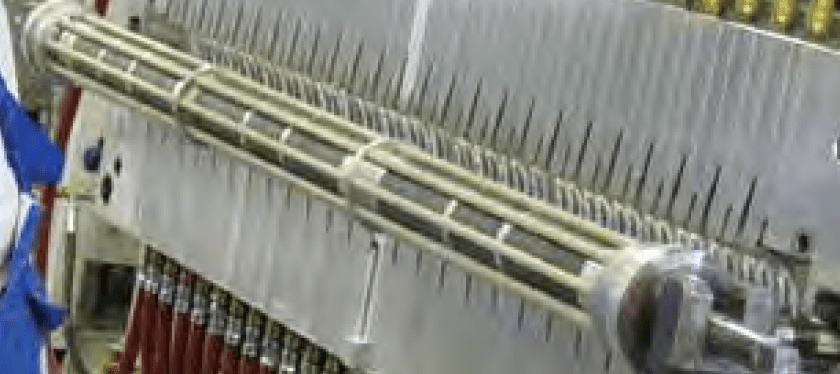
CLICK TO ENLARGE
Critics of wrap type arrester designs point to the possibility for build up of internal pressure in the event of a short circuit since the gases generated cannot easily escape. This can then result in ejection, at high velocity, of pieces from the blocks and cured resin which can cause damage to neighbouring equipment at the station. Manufacturers who utilize this design concept defend it on the grounds that the wrap is an open weave type that, even after curing, still allows venting of internal gases.
Tube Design Containment of Blocks
A third design possibility for a HV polymeric arrester sees the porcelain in a conventional HV arrester design replaced by an FRP tube with silicone sheds either moulded onto it or slipped over it. This design offers the best protection against risk of ejection of internal parts and is comparable in this regard to porcelain. Depending on voltage class, use of a tube allows designs, normally made up of several individual caged or wrapped modules, to be replaced by only one unit, which can be made even longer than the practical limit for porcelain. With any multiple unit arrester, pollution performance becomes that much more important since it can result in a non-linear voltage distribution across the arrester. With a pollution layer and greater dew formation on lower units, most of the voltage drop is at the top and therefore stresses the uppermost part of the arrester. This can, of course, be avoided by good pollution performance of the housing.
Tube-type polymeric HV arresters offer high mechanical strength and are also well-suited for applications in areas prone to seismic activity. One drawback, however, is cost, which can be higher than conventional porcelain having the same mechanical performance and also higher than cage types – especially at lower transmission voltages. This design is best suited for specialized applications where the customer demands high mechanical strength. It does not, however, eliminate the air space between column and housing and therefore sealing the arrester against moisture ingress is critical.
Transmission Line Arresters
HV arresters have traditionally found application only at substations since, due to weight, it was impractical to hang porcelain-housed units on towers. Another issue was safety, given the history of explosive shattering of failed distribution arresters with porcelain housings. The advent of polymeric- housed HV arresters overcame these limitations and opened up a new area for these components – protecting transmission lines against lightning-induced faults. The level of interest in this technical solution has varied and depended on factors such as local isokeraunic activity (IKL); grounding conditions of towers along the line as well as the incidence of back flashover, among others. One place where this combination of factors produced great interest has been Japan. Utilities there had employed a variety of countermeasures to deal with lightning on transmission lines – from shield wires, to improving tower footing resistance, to special designs aimed at reducing number of direct hits to conductors. However, in spite of these measures, lightning still accounted for most faults on overhead transmission systems. As a result, installation of transmission line arresters began in the late 1980s as part of systematic programs to eliminate lightning-induced faults on lines serving key customers.
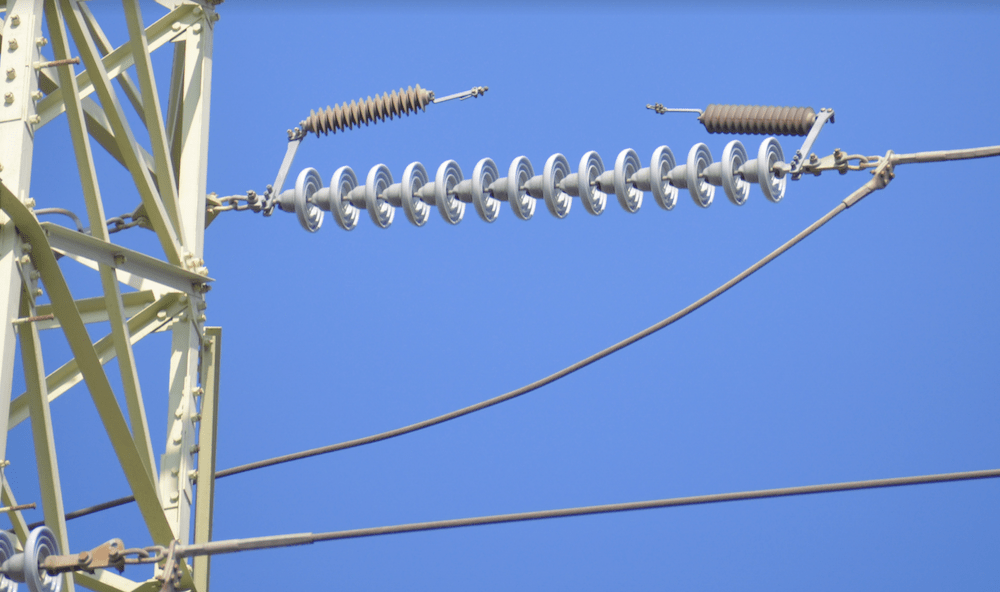
CLICK TO ENLARGE
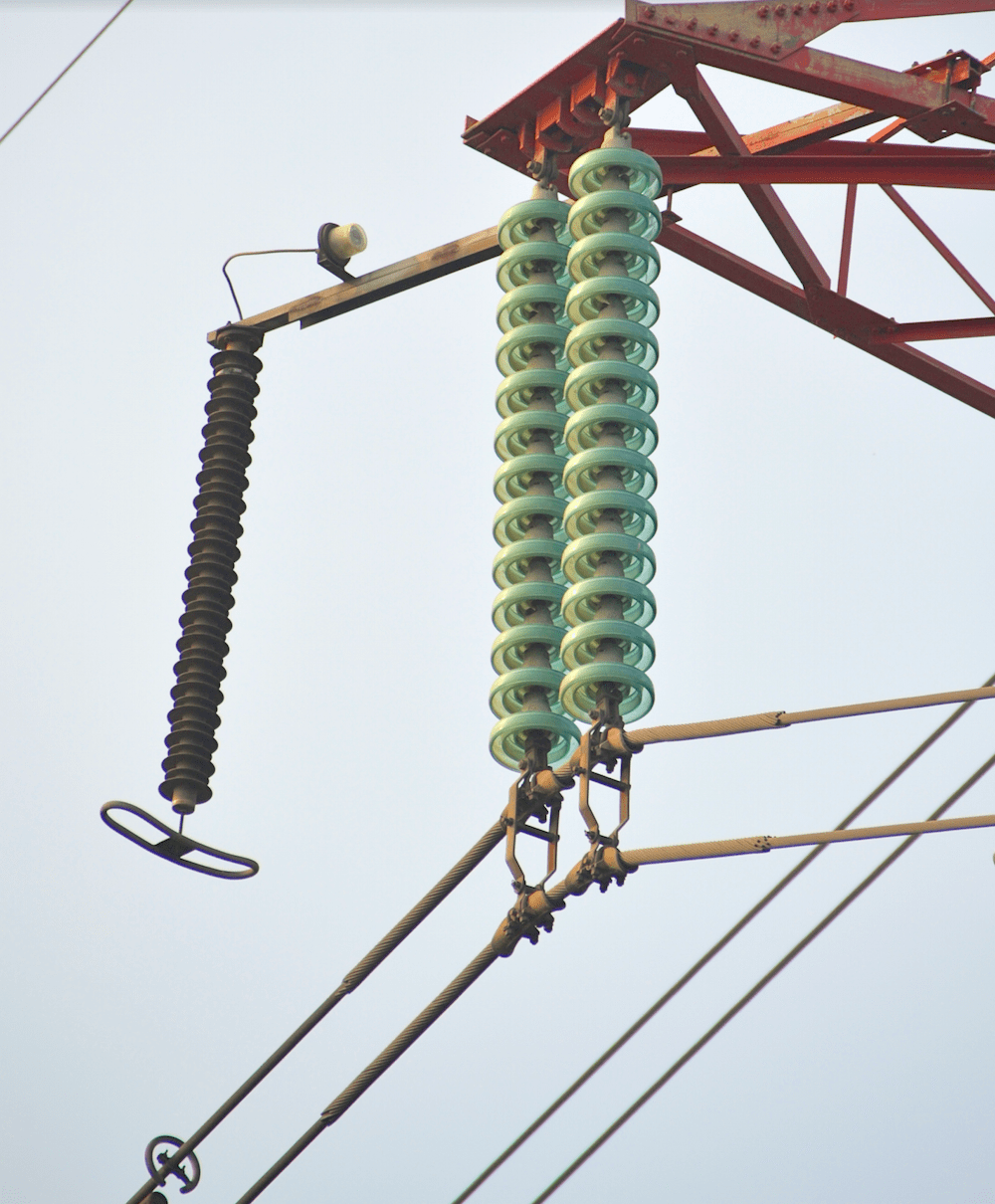
CLICK TO ENLARGE
Suppliers in the arrester industry have been interested in such experience since it demonstrated that newer designs for HV arresters also opened up additional applications. However, notwithstanding this interest, there is still uncertainty about actual sales potential. One stumbling block, depending on country and specific utility customer, has been cost. Interest in markets such as the U.S., for example, has been greatest at the lower end of the transmission range, specifically 69 kV, 115 kV and 161 kV. These lines are constructed differently from those at higher voltages, which are designed to be protected against lightning strikes by employing shield wires. But if a utility wants to improve lightning performance of a lower voltage transmission line, adding a shield wire along the route becomes an expensive solution.
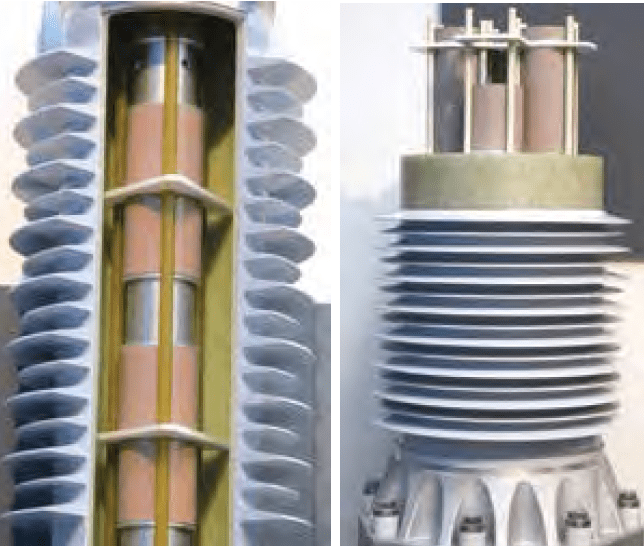
CLICK TO ENLARGE
Looking at this business requires a somewhat different thought process than used for HV arresters at stations. For example, since the arresters are now dealing mostly with lightning rather than switching surges and since they are sharing the duty with other such arresters installed in parallel blocks can be of the same dimensions as used for distribution arresters. Also, while in stations engineers look for the lowest protective levels so that insulation is not stressed, in transmission line applications they want the protective level to be high since the insulation is self-restoring. Basically, in this case they want to get the voltage high enough so that the insulators do not flashover.
There are differing configuration possibilities in regard to how HV arresters are installed on transmission lines: the gap type (EGLAs) sees a series gap between the arrester and the conductor; and the gapless type (NGLAs) which rely on a disconnector device to induce re-closing of the circuit in the event of failure. The gap type has been the preferred solution among Asian utilities since the metal oxide blocks are not continuously energized. This allows reduction of column length while still meeting the requirements for interruption of the follow current. While a gapless arrester design offers instantaneous operation, in spite of a slight time delay in operation the gap type offers equivalent basic performance.
Future Expectations
As with arresters in the MV range, no technological breakthroughs are foreseen for HV arresters. Rather, most in the industry anticipate growing acceptance of the polymeric design innovations that have been introduced over the past 20 to 25 years. For example, porcelain and polymers are well on the way to exchanging their relative market shares, so that polymeric-housed designs will soon come to represent twothirds of this business. Certain suppliers may develop blocks capable of handling higher energies but this could result in a hot system, meaning thermal issues would then take precedence. Developing smaller blocks means that there would be a need for a better thermal system, which would likely be difficult since the entire arrester design becomes more complex. Some in the industry believe that the only way to drive the value equation for HV arresters more in the direction of customers is to move away from comparatively expensive porcelain housings and possibly greater movement toward designs with a solid dielectric system directly moulded onto the blocks. Work has been underway to develop designs which, while no longer based on porcelain housings, still offer the high cantilever strength required by many customers.
Future developments in both materials and designs will probably focus mainly on design issues associated with reducing costs while still meeting customer specifications. Everybody in this field, it seems, looks to transmission lines as a relatively untapped application where those arrester suppliers with the most suitable designs and lowest production costs can achieve big gains in volume. However, this optimism is tempered by the reality that much will depend on whether utilities agree to invest to increase reliability using this technology. Will polymeric HV arresters follow the path of their MV counterparts and eventually take over this category? Perhaps. However, it does not seem likely for at least another decade. Moreover, for this to occur, users may have to re-think how they install these types of arresters in order to take full advantage of the possibilities offered. As long as customers look at polymeric station arresters as a one-for-one replacement for porcelain-housed units and meeting the same mechanical requirements, they may never realize all the benefits offered by the new designs. For example, the lighter weight made possible by polymeric designs means that substation arresters can be installed in more innovative ways, such as being suspended. This would allow HV arresters to become much more versatile in meeting the changing needs of utilities worldwide.