Para algunos usuarios, los aisladores de vidrio templado pueden parecer un artículo cuyo nivel de desempeño se asegura con las normas internacionales aplicables. Sin embargo, la experiencia reciente de servicio y la investigación en laboratorios ha revelado que, a pesar de las normas, la calidad de los aisladores de vidrio puede variar significativamente entre los proveedores, lo que depende de factores como las materias primas, el conocimiento del proceso y el control.
Este artículo de INMR, creado a partir de los aportes de empresas de servicios de Noruega y Suecia, así como también según las visitas a fábricas de aisladores de vidrio en todo el mundo, describe los elementos claves para producir estos aisladores y así, asegurar su calidad y desempeño constantes.
Experiencia de servicio con aisladores de vidrio de diferente calidad
El operador del sistema de transmisión noruego, Statnett, monitorea con atención la calidad de todos los aisladores de vidrio que compra. Por ejemplo, sus representantes asisten a las pruebas de las muestras de las entregas más importantes y también han evaluado los resultados de pruebas que abarcan muchos años. A pesar de estas precauciones, los datos de operación sobre la tasa anual de rotura por cada 100.000 aisladores de vidrio muestran que este parámetro puede variar significativamente entre los distintos proveedores y, a veces, incluso entre los diferentes lotes del mismo proveedor.
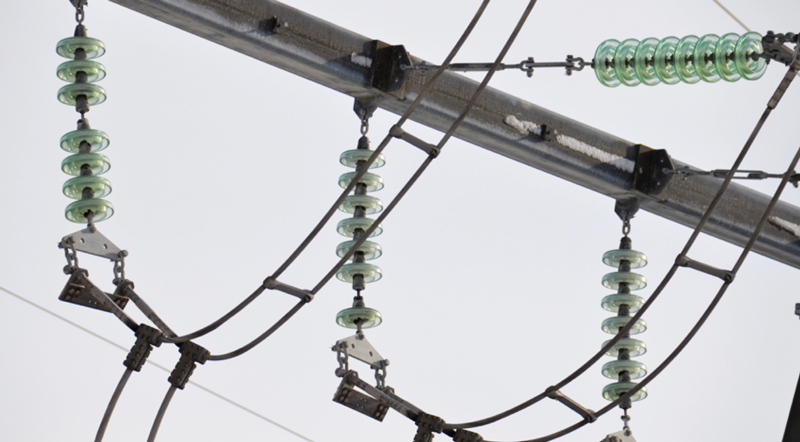
De manera similar, durante la renovación reciente de una línea de 220 kV de la empresa sueca TSO, Svenska Kraftnät, se especificaron aisladores tipo tapa & pasador de vidrio. Los aisladores se suministraron según las prácticas comunes de licitación, lo que incluye el cumplimiento de los requerimientos de la IEC y se instalaron en un área limpia, aunque húmeda, típica de la región. En estos aisladores, después de solo un breve tiempo en servicio, se reportaron actividad de descarga anormal y ruidos, por lo general cuando la humedad era alta. La inspección en terreno confirmó la actividad y sugirió que los aisladores podían estar afectados por defectos en el cemento, lo que podía impactar de manera adversa el desempeño a largo plazo.
La investigación de seguimiento detallada, que incluye pruebas de voltaje a voltaje de operación, reveló actividad de descarga en la superficie de vidrio alrededor del pasador, justo fuera del cemento. Esto era especialmente evidente si la distribución del campo eléctrico en esta parte del aislador estaba expuesta a agua rociada para simular condiciones húmedas de servicio. Las mediciones de resistencia realizadas con una sonda manual mostraron que esta debilidad se debía a la inusual conductividad alta y a la geometría desfavorable del cemento. Por ejemplo, los niveles de radio interferencias (RIV) se habían propagado ampliamente entre los aisladores de diferentes fabricantes y esto se interpretó como un indicador de un mal control de calidad. Dado esto, se propuso expandir los requerimientos de prueba a las futuras ofertas para que se incluyan las mediciones de RIV a 20 kV y 24 kV con el fin de reducir el riesgo de problemas similares en el futuro. Parecía que este requerimiento sería fácil de implementar y ayudaría a asegurar que todos los aisladores comprados fueran más resistentes en cuanto a la actividad de descarga en condiciones húmedas.
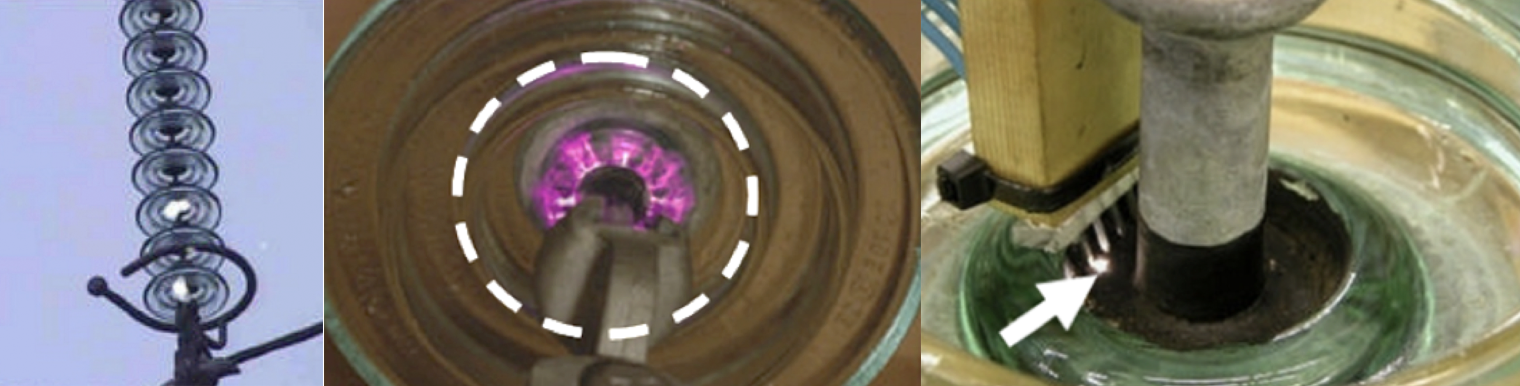
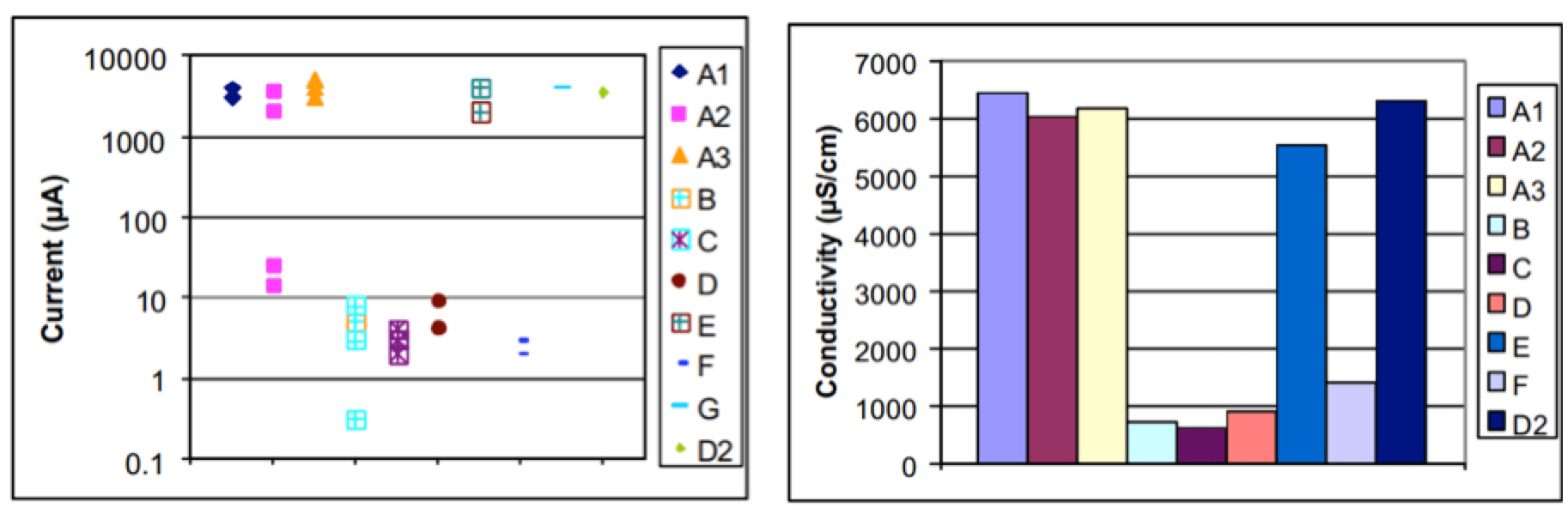
Proceso de Producción & Control de Calidad
La producción de los discos de los aisladores de vidrio templado comienza con un proceso altamente automatizado que pretende asegurar una composición química perfectamente homogénea y consistente. Las materias primas, como cuarzo, arena, ceniza de soda, calcitita, feldespato y dolomita, entre otros, se almacenan en silos computarizados.
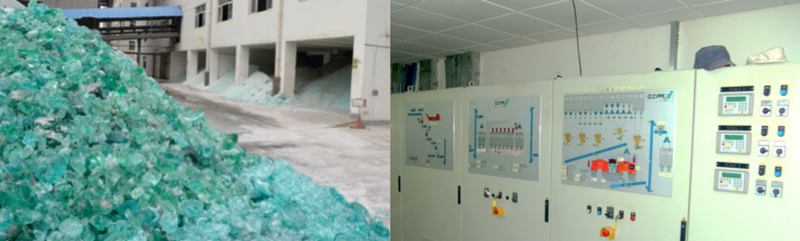
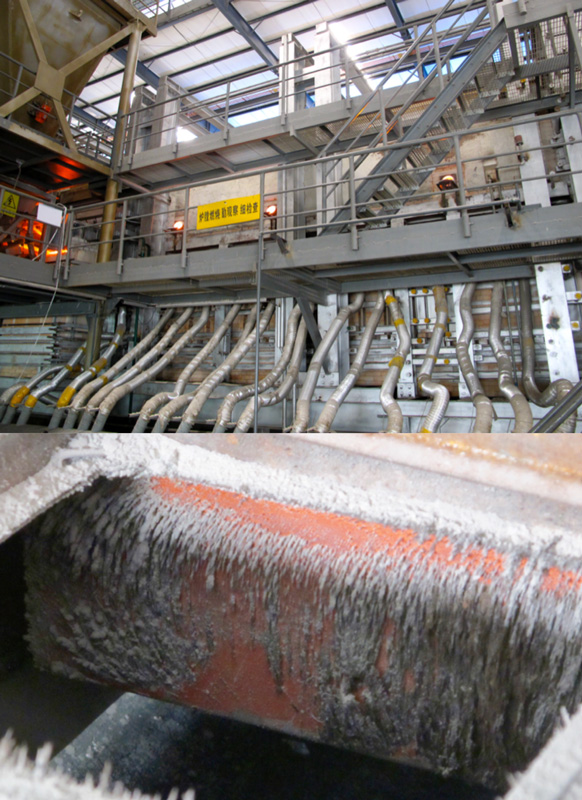
Todas las distintas materias primas pasan por un análisis químico y un tamizado para asegurar que tienen la misma consistencia básica. Luego, estos materiales se combinan con un sistema de lotes computarizado, que asegura que la composición sea precisa y la misma, y se alimentan a un horno que tiene canales equipados con magnetos para eliminar cualquier contaminante metálico. Incluso, la presencia de pequeñas cantidades de metal de unas pocas partes por millón puede generar más óxido de fierro en el vidrio y un tinte verdoso. Alrededor de 1/3 de la masa que se alimenta al horno es vidrio machacado, es decir, discos de vidrio previamente formado que se trituran cuando se forman o que se rechazan aguas abajo durante la inspección, pero también tiene gotas de vidrio no utilizadas generadas en el cambio de moldes. La presencia de vidrio machacado, cuya proporción relativa varía según el tamaño y el diseño del disco de vidrio, contribuye a la estabilidad y la consistencia del proceso de fabricación.
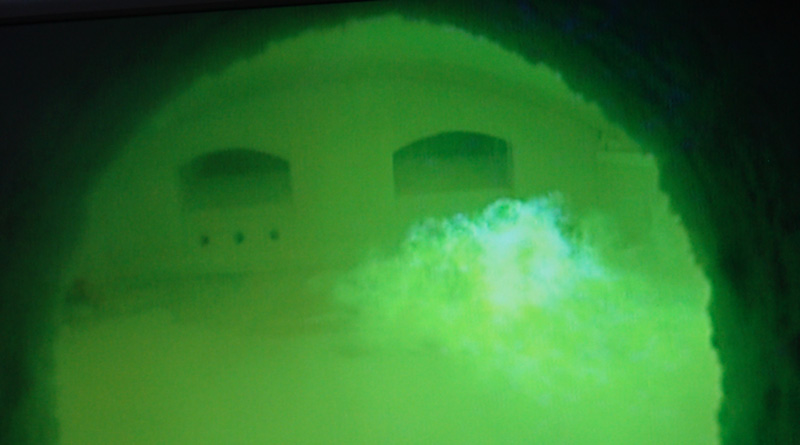
Uno de los activos más críticos en la producción de los aisladores de vidrio es el horno que, comúnmente, está diseñado para ser usado con gas y algún estímulo eléctrico cuando sea necesario. Normalmente, existen dos canales de calentamiento que se alternan alrededor de cada 15 a 20 minutos de manera que las emisiones calentadas que salen de un canal sirven para precalentar el aire de entrada y así, se impulsa la llama del otro canal. Esto genera calentamiento optimizado. Un comando sofisticado y un sistema de control miden todos los parámetros claves para asegurar la completa homogeneidad de la masa derretida. Esto, requiere de una capacidad continua del horno, que está diseñado para operar durante años a temperaturas de hasta 1280 °C sin la necesidad de realizar ninguna parada de mantenimiento. Cada aspecto se monitorea hasta lograr una cantidad precisa de gotas de vidrio fundido, libre de burbujas, inclusiones o impurezas, que se lleva por medio de alimentadores especiales directamente a los moldes precalentados.
Los moldes, que se colocan en una máquina rotatoria, reciben la gota de vidrio y establecen la forma externa y las dimensiones del disco. La geometría interna se determina con dispositivos de sello insertos en la masa fundida dentro de la cavidad de los moldes. El prensado es crítico no solo porque da la forma interna final, sino que también para asegurar un espesor uniforme: un factor que minimizará el riesgo de rotura durante el proceso de templado que le sigue. La temperatura del vidrio en esta etapa es de un poco más de 1000 °C, significativamente más frío que cuando está en el horno.
Cuando sea que se necesite cambiar los moldes para producir un aislador de una geometría diferente, se hace evidente la importancia de un espesor constante. Puede que estos cambios requieran que se arrastren diferentes volúmenes de vidrio fundido desde el horno para cada gota y la tasa de rotura puede subir levemente a medida que se ajusta y estabiliza el proceso.
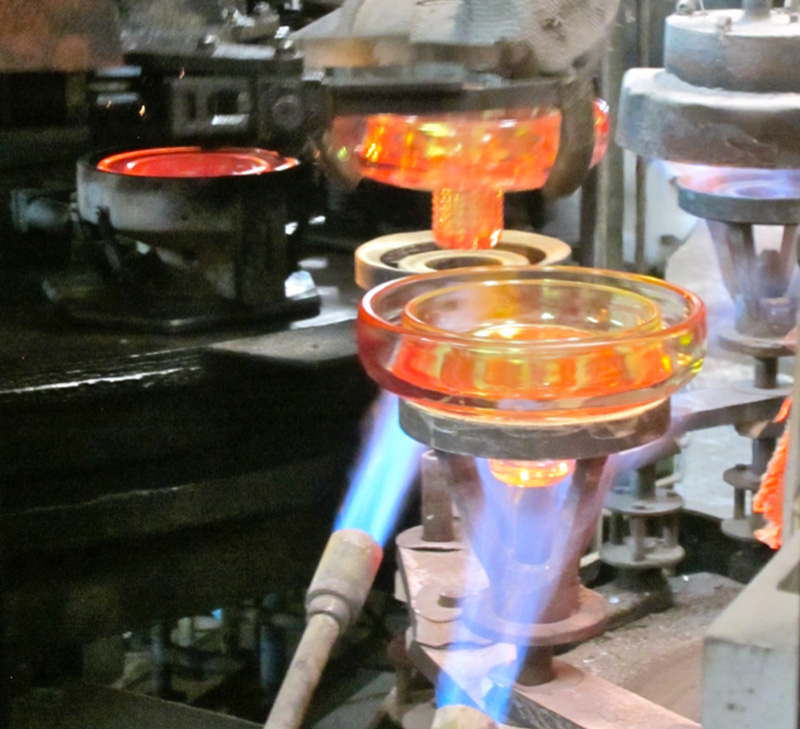
Después del moldeado y la rotación, los discos de vidrio pasan por el proceso crítico de templado, donde se exponen al enfriamiento rápido de la superficie con chorros de aire comprimido, incluso cuando su interior aún está extremadamente caliente. Luego, a medida que el disco se mueve a través de la máquina, su interior se enfría y contrae en un proceso que genera las tensiones compresivas deseadas en la superficie. Para conseguir este efecto por completo, el vidrio debe estar totalmente transparente ya que la presencia de incluso diminutas inclusiones puede llevar a su rotura.
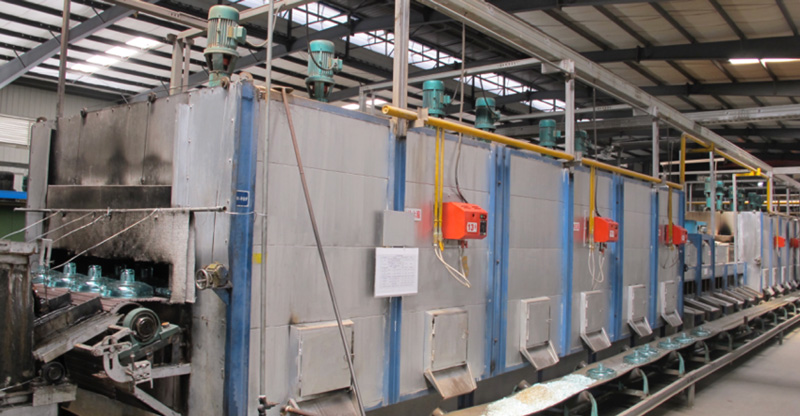
El proceso de templado es un determinante importante del desempeño de servicio ya que asegura que ninguna micro grieta se propague en el dialéctrico con el tiempo y que no haya ciclos de carga-temperatura. Las pre-tensiones compresivas en la superficie de los discos de vidrio aumentan significativamente la resistencia mecánica.
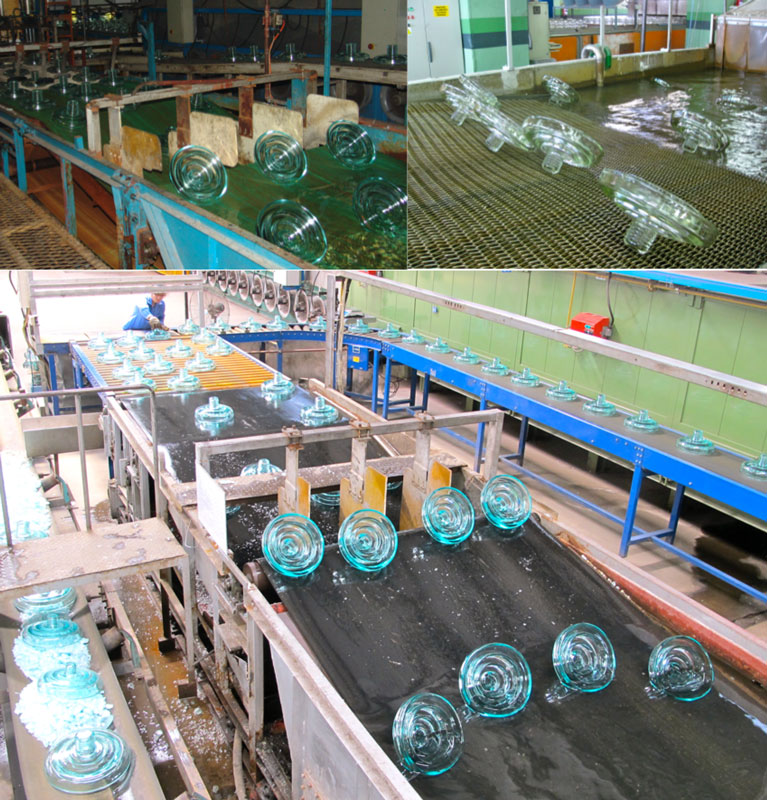
Luego del templado, los discos de vidrio pasan por golpes térmicos sucesivos con inmersión en agua fría, como lo requieren las normas. Este proceso de ciclos repetidos de calentamiento y enfriamiento alternados ayuda a eliminar la mayor parte de las unidades que tienen inclusiones u otros defectos ya que, por lo general, estos se trituran durante los cambios rápidos de temperatura. El golpe térmico destruye tantas piezas defectuosas como sea posible mientras que aún están en la fábrica y aún no se instalan en la línea.
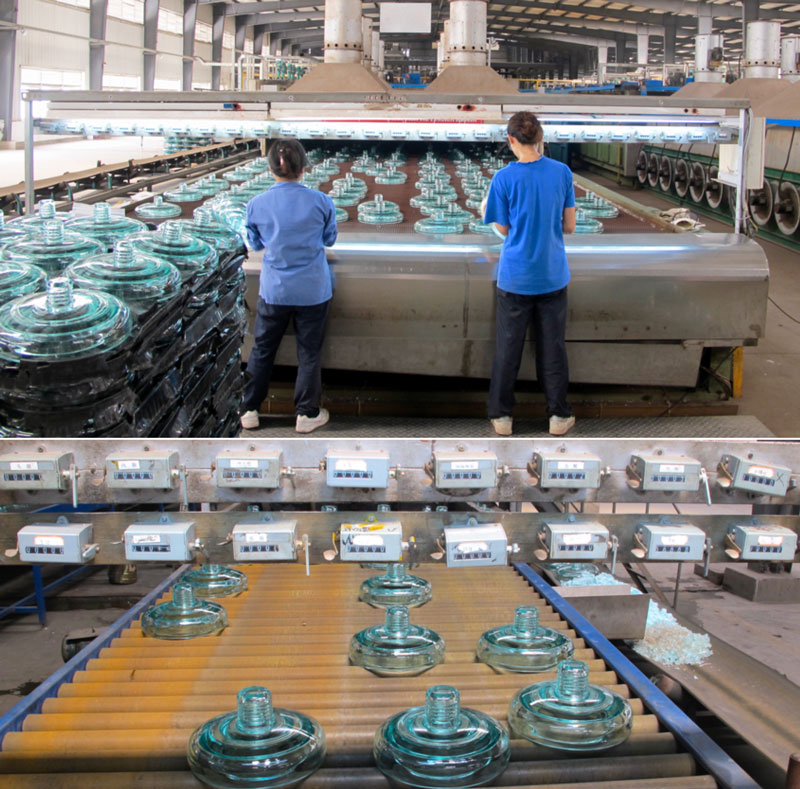
Finalmente, se realiza una cuidadosa inspección visual de cada disco y cualquier unidad defectuosa se coloca en un transportador para ser reciclada como vidrio machacado. Aquellas unidades que pasan la inspección están básicamente terminadas y listas para ser ensambladas con los accesorios. Las tasas de aceptación de las discos en una fábrica de aisladores de vidrio variarán entre los proveedores, pero por lo general, una cifra de alrededor del 90 por ciento se considera satisfactoria. En algunos fabricantes, el personal de control de calidad utiliza contadores que se instalan en cada línea de producción para registrar y rastrear la tasa de cada tipo de defecto que se identifica durante la inspección visual. Luego, el personal de producción estudiará estos datos regularmente y discutirá si es necesario ajustar ciertos parámetros del proceso, como el ángulo de los quemadores, la temperatura del horno o la alimentación de gotas.
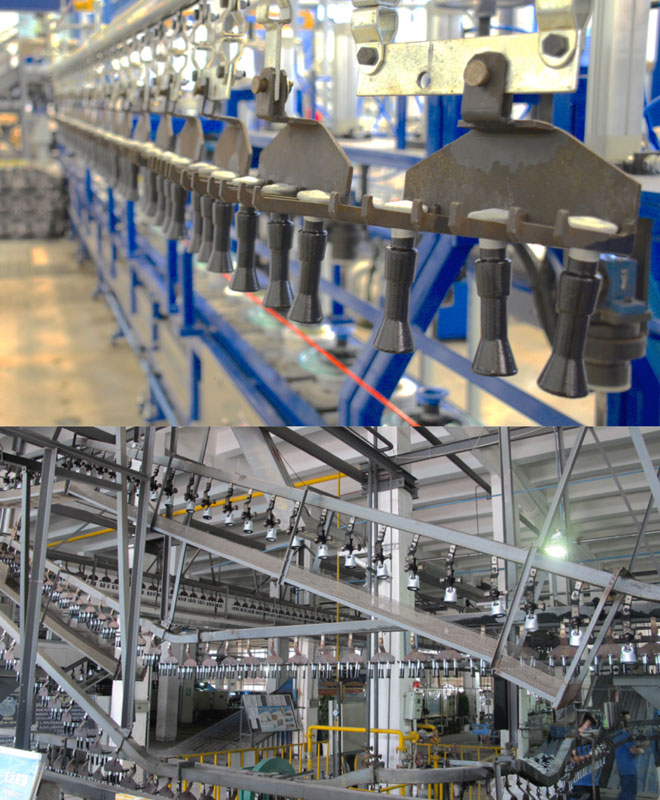
Después de almacenarlas, los discos de vidrio pasan a la etapa siguiente que consisten en adosar la tapa metálica y el pasador a cada unidad. Primero, el ferraje se sumerge en alquitrán (bitumen) para reducir el riesgo de corrosión en las interfaces claves y también para dar protección entre el vidrio y las superficies metálicas que tienen diferentes coeficientes de expansión con cambio de temperatura. Los accesorios se llevan en transportadores aéreos a estaciones de trabajo automatizadas donde se unen a las discos de vidrio con cantidades precisas de cemento especial previamente mezclado.
Después del ensamblaje, se realiza el curado en un baño de agua caliente, cuya temperatura depende de la clasificación mecánica del aislador. Por ejemplo, algunos fabricantes curan discos de 300 kN a alrededor de 70 °C durante 1 hora y media.
La última etapa en la producción consta de pruebas y la mayor parte de ellas se realiza con muestras de producción en laboratorios en cada fábrica. Una prueba que se realiza en cada unidad después del curado es la resistencia mecánica a la tensión, que se hace al 50 % de la nominación de SML. Una operación de ensamblaje bien manejada apunta a una consistencia en la distribución de la carga de falla promedio tal como para cumplir con 3 o incluso 4 criterios de sigma. El comportamiento mecánico de los discos de vidrio de alta calidad es, a menudo, tan bueno que incluso si el disco del dieléctrico se tritura, el “stub” (Caperuza + PIN) continuará cumpliendo con su nominación designada.
Las pruebas se realizan de acuerdo a las normas pertinentes de la industria o para satisfacer las demandas especiales de los clientes cuyos requerimientos pueden ser diferentes entre sí o más estrictos que aquellos mencionados por la IEC. Un ejemplo es la prueba de RIV que comúnmente se realiza a 10 kV, 1 MHz con 34 dB máximo permitido, aunque algunas empresas requieren pruebas a 30 kV, 1MHz y 52 dB. De manera similar, algunos clientes requieren mediciones de resistencia a la aislación o pruebas de impactos, que ya casi no se solicitan,pero que a veces aún se exigen a un nivel incluso más alto que el especificado en las normas. Otro ejemplo de un requerimiento de prueba especial es cuando se cuelgan tiras de vidrio a ángulos de hasta 30° dentro de un túnel y se exponen a vientos de velocidades de 20 m/s. Si se emite cualquier ruido, la tira no pasa la prueba.
Entre los esfuerzos para mejorar el control de calidad en las plantas de aisladores de vidrio en los últimos años, se ha asegurado que todos los discos de vidrio y los códigos de barra del ferraje indiquen la hora y la fecha de producción. Esto se hace para asegurar la completa trazabilidad en caso de que posteriormente ocurra algún problema en el servicio.
/p>